Bard Bayrd Furnace 403293A User Manual
Page 30
Attention! The text in this document has been recognized automatically. To view the original document, you can use the "Original mode".
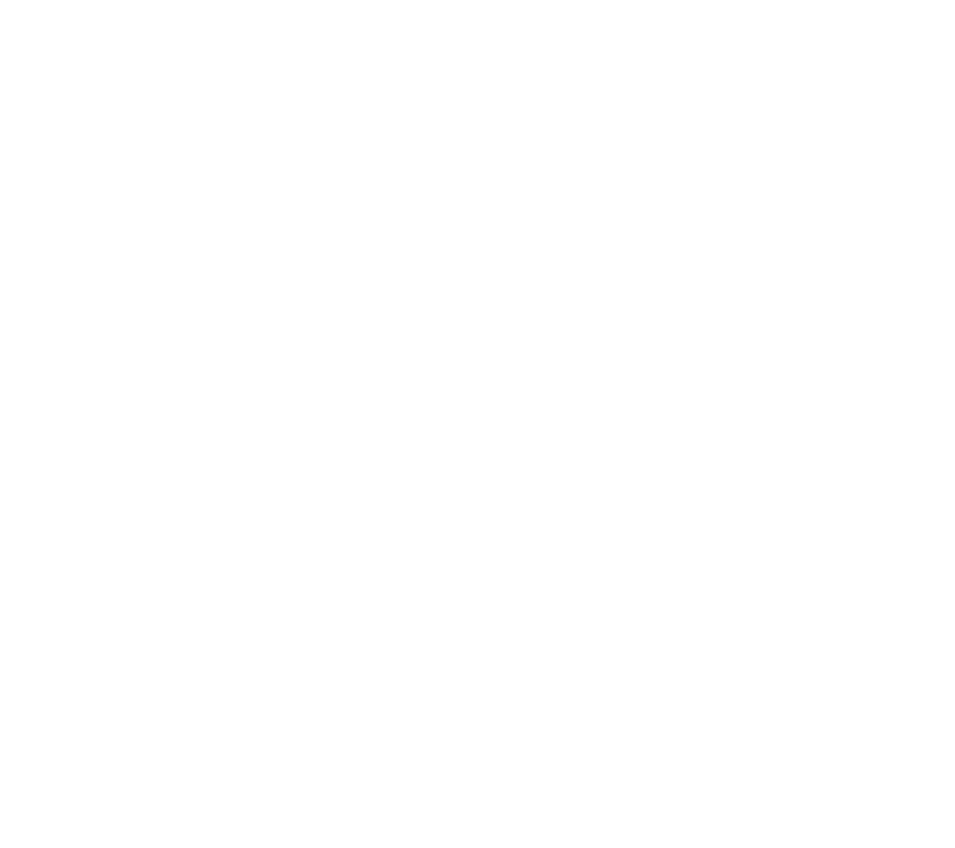
Example:
Assume it took
29 seconds for one cubic foot of
gas to flow and heating value of 1,000 BTU/
CU.FT.
Gas Input -
1,000 x 3,600
29
124,138 Btuh
10
.
11
.
b.
If you left no other pilots on, this is the furnace
gas input.
If you left water heater, dryer or range pitots on,
allow for them in calculating correct furnace gas
input. A quick way is to allow 1,000 Btuh for a
water heater. Allow 500 Btuh for dryer and 500
Btuh for each range burner pilot.
Example:
If you left gas water heater, dryer, four range
burner pilots and one oven pilot on, allow:
Water heater pilot
Dryer pilot
4 range burner pitot
1 range oven pilot
1.000 Btuh
500 Btuh
2.000 Btuh
500 Btuh
4.000 Btuh
Subtracting 4,000 Btuh from 124,138 Btuh
measured above equals 120,138 Btuh. This
would be the correct furnace gas input after
allowing for pilots left on.
Manifold pressure may be adjusted within the range
of 3.2 inches W.C. to 3.8 inches W.C. to get rated
input. If you cannot get rated input with manifold
pressure within the allowable range, you will need
to change orifices. See Section 23.
Turn off gas. Remove 1/8"-pjpe manual shut-off
valves you used. Install 1/8”-pipe plugs In gas con
trol inlet and outlet pressure taps. Tighten to torque
of 50 inch-pounds. Turn on gas. Check both pipe
plugs for gas leaks. Use a commercial soap solution
made for leak detection.
WARNINOi
Never use an open flame to check
for gas leaks. A gas leak could cause a fire or
explosion, resulting In damage, Injury or death.
B. Propane (LP) Gas.
WARNING
t Propane (LP) gas Installations do not
have gas meters to double check Input rate. Measure
manifold pressure adjustment with an accurate "U"
tube water manometer. Failure to accurately adjust
pressure could cause heat exchanger failure, as
phyxiation, fire or explosion, resulting In damage,
injury or death.
NOTE: For operation at elevations above 2,000 feet,
follow instructions in Section 23.
1. Make sure you have correct pilot orifics and main
burner orifices. Be sure that gas piping is large
enough for all appliances connected to it to operate
at once without lowering the main line pressure.
Failure to do so could causa lighting or burning
problems on any of the appliances.
2.
Gas control inlet pressure must be between 11
inches and 13 inches for propane (LP) gas. See
Section 19A to check gas supply line pressure.
3.
Turn off all other gas appliances. Pilots may be left
on. Start furnace following Operating Instructions
on front door or in Users' Information Manual.
4.
As furnace warms up, watch gas supply line (gas
control inlet pressure) using "U" tube water manom
eter in gas control inlet pressure tap. See Section
19A. Supply line pressure must stili be between 11
inches and 13 inches W.C. for propane (LP) gas.
5.
After verifying correct gas control inlet pressure,
close shut-off valve tn gas control inlet pressure
tap. Move manometer to gas control outlet pressure
tap. See Section 20. Open shut-off valve in gas
control outlet pressure tap. Let furnace warm up for
6 minutes,
6.
Manifold pressure should be 10.0 inches W.C.
+/-
0.3 inches W.C. Adjust by removing regulator cover
screw on gas control. Save screw for re installation.
Turn inner adjustment screw counter-clockwise <-
to decrease manifold pressure; turn clockwise -> to
increase manifold pressure. Set correct manifold
pressure. Install cover screw and tighten to torque
of 5 inch-pounds to prevent gas leakage.
CAUTIONi
Many Installers' set propane (LP)
manifold pressure at 11.0 Inches W.C. Do not
do this. It could cause heat exchanger failure or
nuisance callbacks.
WARNINGS
Propane (LP) gas Installsttons do
not have gas meters to double check Input rats.
You must measure manifold pressure adjustment
with an accurate "U" tubs water manometer.
Failure to accurately adjust pressure could cause
hast exchanger failure, asphyxiation, fire or ex
plosion, resulting In damage. Injury or death.
7.
Turn off gas before removing the 1/8"-pipe manual
shut-off valves. Install 1/8*-ptpe plugs In gas control
inlet and outlet pressure taps. Tighten to torque of
50 inch-pounds. Turn on gas. Check both pipe plugs
for gas leaks. Use a commercial soap solution made
for leak detection.
WARNINGS
Never use an open flame to chock
for gas leaks. A gee leak could ceuee a fire or
explosion resulting In damage, Injury or death.
28