A warning – Carrier 48N User Manual
Page 11
Attention! The text in this document has been recognized automatically. To view the original document, you can use the "Original mode".
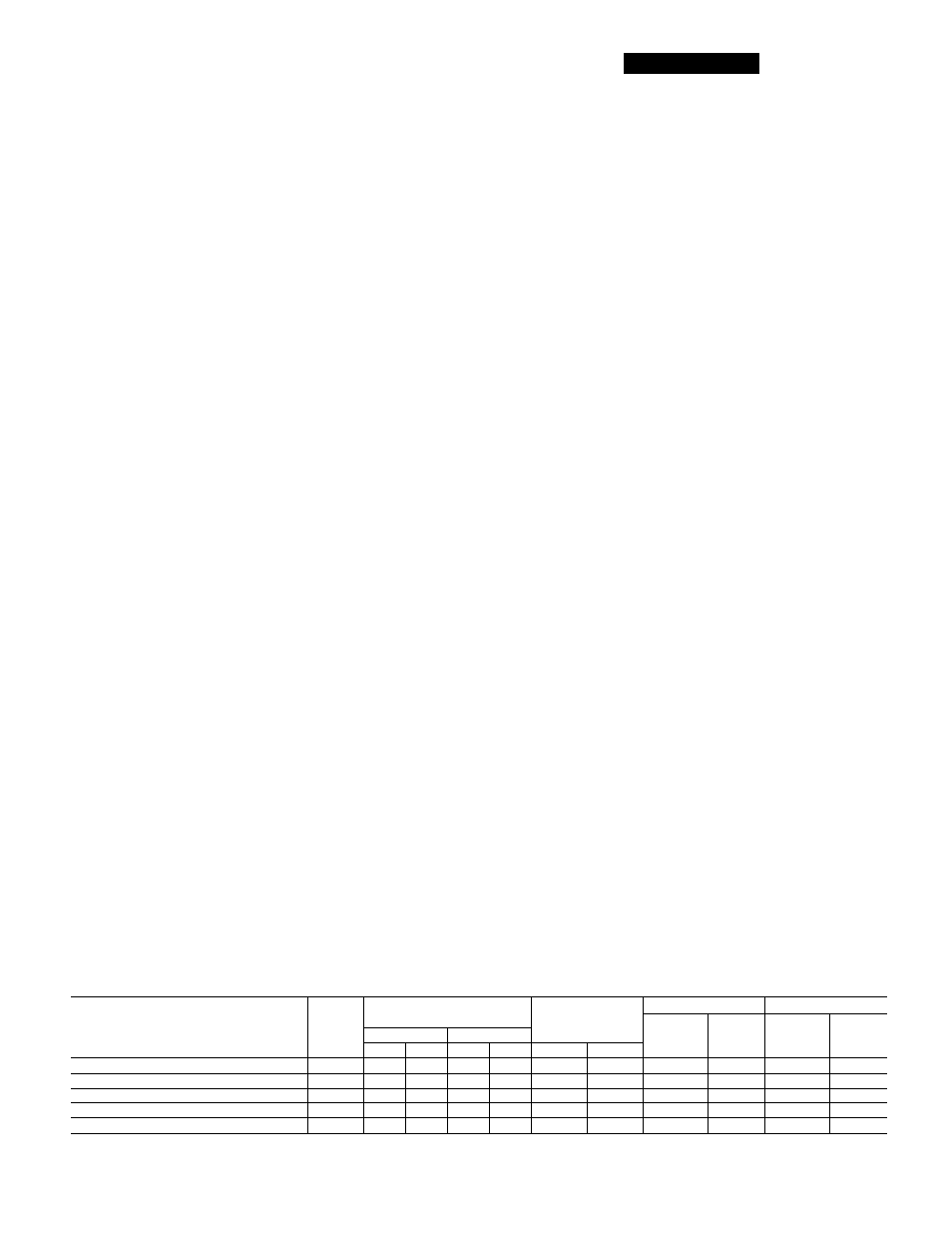
codes, or contact your Distributor or Branch to determine
the required orifice size.
C. Adjusting Gas Input
The gas input to the unit is determined by measuring the
gas flow at the meter or by measuring the manifold pres
sure. Measuring the gas flow at the meter is recommended
for natural gas units. The manifold pressure must be mea
sured to determine the input of propane gas units.
1. Measuring Gas Flow at Meter Method—Natural Gas
Units
Minor adjustment can be made by changing the manifold
pressure. The manifold pressure must be maintained
between 3.2 and 3.8-in. water. If larger adjustments are
required, change main burner orifices following the recom
mendations of national and local codes.
NOTE:
All other apphances that use the same meter must
be turned off when gas flow is measured at the meter.
Proceed as follows:
Turn off gas supply to unit.
Remove pipe plug on outlet of gas valve, then con
nect manometer at this point. Turn on gas to unit.
Record number of seconds for gas meter test dial to
make one revolution.
Divide number of seconds in step c into 3600 (num
ber of seconds in 1 hour).
Multiply result of step d by the number of cubic ft
shown for one revolution of test dial to obtain cubic
ft of gas flow per hour.
f. Multiply result of step e by Btu heating value of gas
to obtain total measured input in Btuh. Compare
this value with heating input shown in Table 8.
(Consult the local gas suppher if the heating value
of gas is not known.)
Example:
Assume that the size of test dial is 1 cubic ft, one
revolution takes 30 seconds, eind the heating value of the
gas is 1050 Btu/ft®, then proceed as follows:
a. 30 seconds to complete one revolution.
b. 3600 -30 = 120.
c. 120 X 1 = 120 ft® of gas flow/hr.
d. 120 X 1050 = 126,000-Btuh input.
If the desired gas input is 125,000 Btuh, only a minor
change in the manifold pressure is required.
Observe manifold pressure and proceed as follows to adjust
gas input:
Remove cover screw over regulator adjustment
screw on gas valve.
Turn regulator adjustment screw clockwise to
increase gas input, or turn regulator adjustment
screw counterclockwise to decrease input. Manifold
pressure must be between 3.2 and 3.8-in.-water.
a.
b.
c.
e.
a.
b.
A WARNING
Unsafe operation of the unit may result if manifold
pressure is outside this range. Personal injury or unit
damage may result.
c. Replace cover screw cap on gas valve.
d. Turn off gas supply to unit. Remove manometer
from pressure tap. Replace pipe plug on gas valve.
Turn on gas to unit. Check for leaks.
2. Measuring Manifold Pressure—Propane Gas Units
The main burner orifices on a propane gas unit are sized for
the unit rated input when the manifold pressure is 10.5-in.
water.
Proceed as follows to adjust gas input on a propane gas
unit:
a. Turn off gas to unit.
b. Remove pipe plug on outlet of gas valve then con
nect memometer at this point.
c. Turn on gas to unit.
d. Remove cover screw over REG ADJ screw on gas
valve.
e. Adjust regulator adjustment screw for a manifold
pressure reading of 10.5-in.-water. Turn adjusting
screw clockwise to increase manifold pressure, or
turn adjusting screw counterclockwise to decrease
manifold pressure.
f. Replace cover screw.
g. Turn off gas to unit. Remove manometer from pres
sure tap. Replace pipe plug on gas valve, then tmrn
on gas to unit. Check for leaks.
D. Check Burner Flame
Observe the unit heatmg operation, and watch the burner
flames through the observation port to see if they are light
blue and soft in appearance, and the flames are approxi
mately the same for each burner. See Fig. 10.
E. Blower Heat-Relay Operation
Blower relay PCI (See the unit wiring diagram.) is located in
the control box and adjusts to permit either longer or
shorter “off” cycles. The “on” cycle is factory set for 1 min
ute on timing. The adjusting dial on the relay (See Fig. 9) is
factory-set at the minimum position to provide optimum
performance for most installations. On unusual installa
tions, the length of time the blower remains on may require
increasing. To increase blower operation time, rotate the
adjusting dial counter-clockwise. To decrease blower opera
tion time, rotate dial clockwise. (Minimum time 1 minute.)
Maximum time 3 minutes.)
F. Airflow and Temperature Rise
The heating section of each size of unit is designed and
approved for heating operation within the temperature rise
range stamped on the unit rating plate.
Table 8—Rated Gas Inputs at Indicated Manifold Pressures
Model
No.
Number
of
Orifices
Gas Supply Pressure
(in. wc)
Manifold
Pressure
(In. wc)
Natural Gas
Propane Gast
Orifice
P/N
Heating
Input
(Btuh)*
Input
P/N
Heating
(Btuh)*
Natural
Propane
Min
Max
Min
Max
Natural
Propane
48NLT018, 024, 030
2
5.0
13.6
11.0
13.0
3.5
10.5
55365-44
40,000
55365-55
40,000
48NHT024, MT030, LT036, LT042
3
5.0
13.6
11.0
13.0
3.5
10.5
55365-44
60,000
55365-55
60,000
48NHT030, MT036, MT042, LT048, LT060
4
5.0
13.6
11.0
13.0
3.5
10.5
55365-44
80,000
55365-55
80,000
48NHT036, HT042, MT048, MT060
5
5.0
13.6
11.0
13.6
3.5
12.5
55365-44
100,000
55365-55
100,000
48NVT036, VT042, HT048, HT060
6
5.0
13.6
11.0
13.6
3.5
10.5
5536544
120,000
55365-55
120,000
♦Based on altitudes from sea level up to 2000 feet above sea level. For altitudes above 2000 feet, reduce input rating 4% for each 1000 feet above sea
level. In Canada, from 2000 ft. above sea level to 4,500 ft. above sea level, derate the unit 10%.
fWhen a 48N is converted to propane, the burners must be modified. See kit instructions.
11