A caution – Carrier 50QQ User Manual
Page 11
Attention! The text in this document has been recognized automatically. To view the original document, you can use the "Original mode".
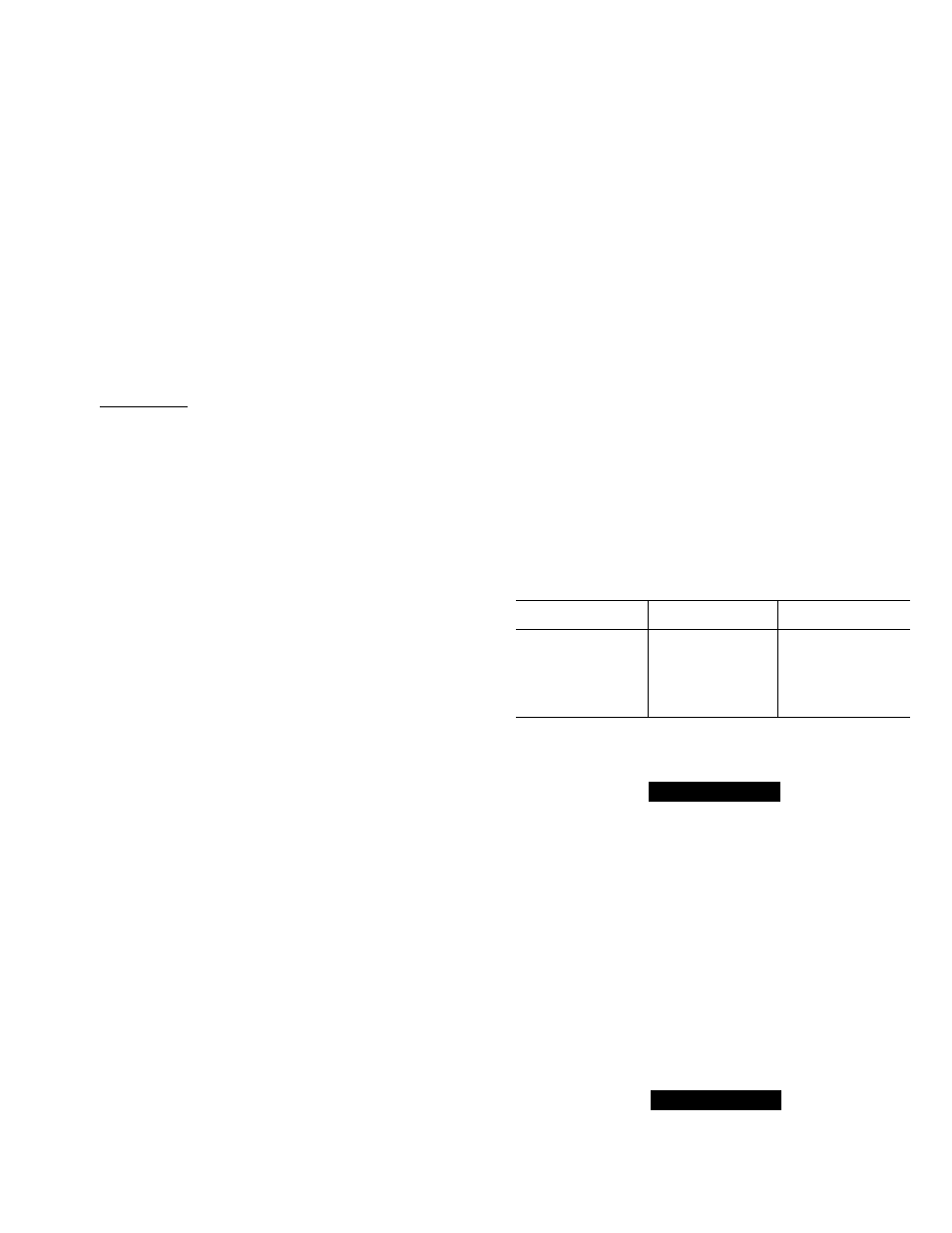
2. Start unit and allow to operate until operating condi
tions stabilize and pressures level out.
3. Evaluate system performance and refrigerant charge
level by determining following conditions:
a. High- and low-side pressure gage reading.
b. Dry-bulb temperature of inlet air at outdoor coil.
c. Dry-bulb temperature of inlet air at indoor coil. This
may be read at central return-eiir grille.
d. Compare readings to those listed in Heating Operat
ing Pressures section of charging chart inside unit
(refer to Table 6, part A). The Heating Operating
Pressures portion of the chart is for checking charge
only when unit is in heating mode and outside tem
peratures are below 60 F.
If charge adjustment is necessary, charge can be adjusted
accurately only by blowing the charge, evacuating system,
and recharging unit with correct charge as listed on unit rat
ing plate. A volumetric charging device such as Dial-a-
charge is recommended for use when recharging.
Cooling Mode—A superheat charging label is affixed to elec
trical access door. The label includes a Field Superheat
Charging table (see Table 6, peirt B) and a Required Suction
Tube Temperature (F) chart (see Table 6, part C).
An accurate superheat-, thermocouple-, or thermistor-type
thermometer, a sling psychrometer, and a gage manifold are
required when using superheat charging method for evalu
ating unit charge. Do not use mercury or small dial-type
thermometers. They are not adequate for this type of
measurement.
Proceed as follows:
1. Remove caps from low- and high-pressure service
fittings.
Using hoses with valve core depressors, attach low-and
high-pressure gage hoses to low- and high-pressure
service fittings, respectively.
Start unit in cooling mode. Let unit run until system
pressures stabilize.
Measure and record following;
Outdoor ambient air dry-bulb temperature (F).
Evaporator inlet air wet-bulb temperature (F).
Suction tube temperature (F) at low side service
fitting.
Suction (low side) pressure (psig).
Using Field Superheat Charging table, compare out
door air dry-bulb temperature (F) with evaporator inlet
air wet-bulb temperature (F) to determine desired sys
tem operating superheat temperature.
Using Required Suction Tube table, compare desired
superheat temperature (F) with suction (low side) oper
ating pressure (psig) to determine proper suction tube
temperature.
Compare actueil suction tube temperature with proper
suction tube temperature. Using a tolerance of ± 3 F,
add refrigerant if actual temperature is more than 3 F
higher than proper suction tube temperature, or
remove refrigerant if actueJ temperature is more than 3
F lower than required suction tube temperature.
Metering Device (Dual-Piston Type) Servicing—
See Fig. 11
for dual-piston components. The pistons have a refrigerant
metering orifice through them. The retainers form a stop for
the pistons in the refrigerant bypass mode, and a sealing
surface for liquid line flare connection. To check, clean or
replace piston:
1. Shut off power to unit.
2.
3.
4.
a.
b.
d.
5.
6
.
7.
2. Remove refrigerant from unit using approved refriger
ant removal methods.
3. Remove liquid line flare connections from metering
device.
4. Note position of arrow on metering device body with
respect to unit.
5. Pull retainer out of body. Be careful not to scratch flare
sealing surface. If retainer does not pull out easily,
carefully use locking pliers to remove retainer. Replace
scratched or deimaged retainer.
6. Slide piston out by inserting a small soft wire through
metering hole (18-gage thermostat wire). See that
metering hole, sealing surface around piston cones and
fluted portion of piston are not damaged.
7. Chart on unit access panel illustrates proper arrange
ment and sizes of piston.
8. Clean piston refrigerant metering orifice.
9. Replace retainer 0-ring before reassembling metering
device. 0-ring Part No. is 99CC501052.
LIQUID LINE STRAINERS (to protect metering device),
are made of wire mesh and located in the liquid line on each
side of the metering device. The strainers are pressed into
the line. Remove strainer by threading a #10 sheet metal
screw into strainer and pulling the screw with pliers.
Compressor Removal—
See Table 7 for compressor informa
tion and Fig. 12 for component location. Follow safety
codes, and wear safety glasses and work gloves. Have
quenching cloth available (step 8).
Table 7—Compressor Data
MODEL
SOQQ
PRODUCTION
COMPRESSOR*
OIL
RECHARGE (oz)
018
H22B173
37
024
JD25
44
030
JD30
44
036
JD37
44
042
JD42
44
048
JD45
44
060
H23A623
47
*Refer to compressor nameplate for complete model number.
A CAUTION
Copper tubing is used in unit coils. Do not overheat or
place excessive strain on tubing or damage may result.
1. Shut off power to unit. Remove compressor access
panel to expose compressor. See Fig. 12.
2. Remove refrigerant from unit using approved refriger
ant removal methods.
3. Remove core from suction and discharge line Schrader
fittings.
4. Disconnect compressor wiring at compressor terminal
box.
5. Using a tubing cutter, cut suction and discharge lines
at convenient place near compressor for easy reassem
bly to new compressor with copper slip couplings.
A CAUTION
Excessive movement of copper lines at compressor may
cause a break where lines connect to other system
components.
11