Out of production – LAARS HP-M2 Series - Installation, Operation and Maintenance Instructions User Manual
Page 25
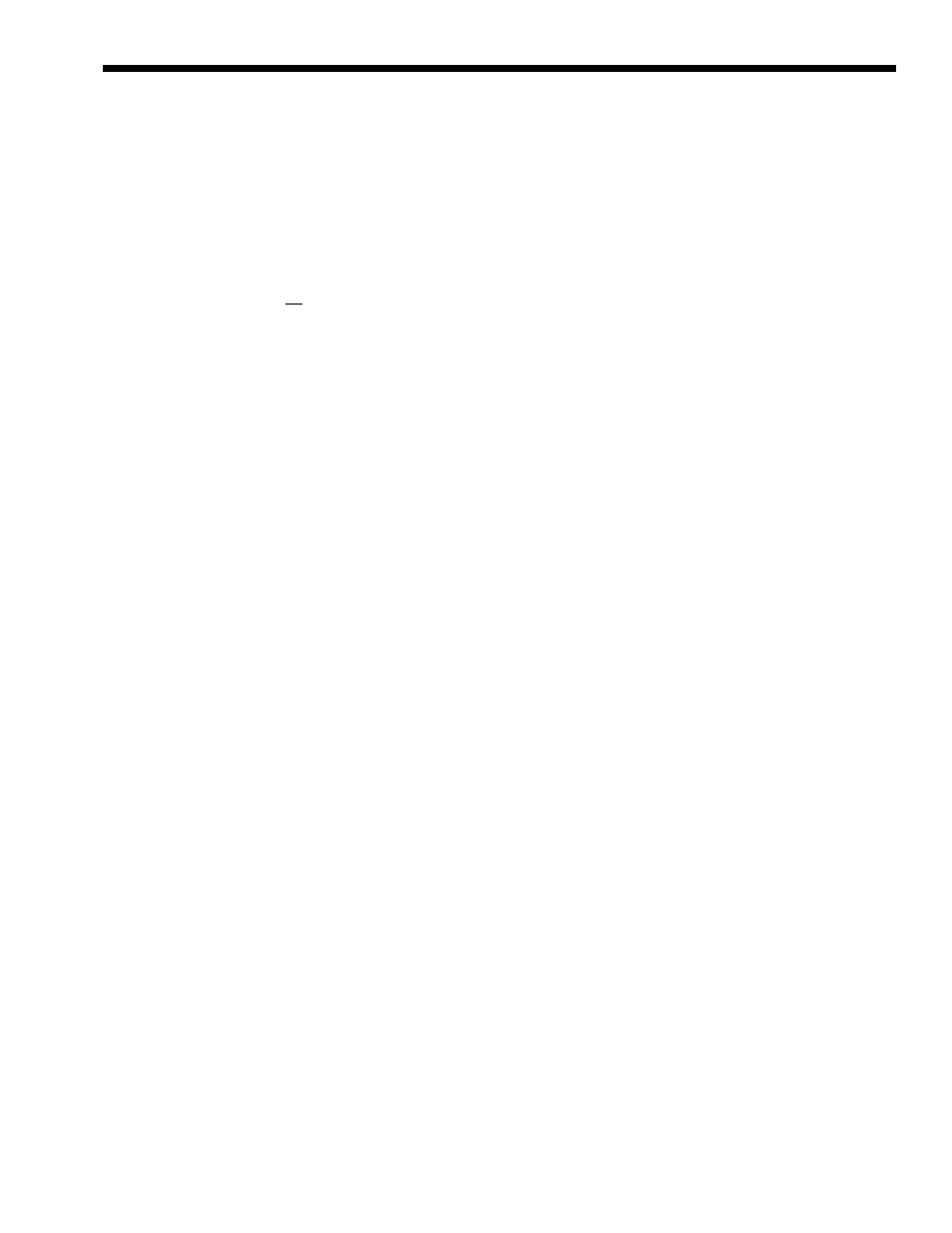
H Series
Page 25
the pressure to go positive (above 0 IN. W.C.). If the
pressure spikes positive when the solenoid opens then
the gas valve regulator is faulty and may be the cause
of the delayed ignition (assuming inlet tested OK).
A defective burner (flameholder) can cause a
delayed ignition however not often. If the gas supply
pressure and the gas valve are functioning properly
and the air and gas orifices are correct the burner
should be inspected. To inspect, remove the blower
and the burner will drop out of the bottom of the
chamber. There should be no perforations other than
the punched holes. When replacing the burner the
insulating pad must be on the top of it. If none was on
the burner when it was removed check to see if it fell
off during burner removal and has stayed in the
combustion chamber. Never leave an insulating pad
lying in the combustion chamber as this can cause
burner overheating and perforation.
12B. Noisy Operation
There are two principal sources of noisy
operation:
a.
Combustion - high pitched noise - whistle or hoot
b.
Boiling (kettling) - lower frequency noise which
varies with temperature - moan.
Combustion noise occurs at any boiler discharge
temperature and is heard the loudest at the flue outlet
(especially on units with side wall venting). There are
two basic causes for the noise, rich mixture and cross
contamination. To check for a rich mixture, it will be
necessary to measure the percent O² or CO² in the flue
products. O² readings lower than 4½ % or CO²
readings higher than 9¼% (natural gas) and 10.8%
(LP) will often cause combustion noise. To eliminate
the noise it will be necessary to install a smaller gas
orifice so that the O² will rise above 4½% or the CO²
will drop to 8½% (natural) or 9½% (LP).
Sometimes the readings are influenced by cross
contamination and a check for cross contamination
should be done before changing orifices if it is
suspected. A strong smell from the flue products is
generally an indication. Check for cross contamination
using the procedure listed in the index. If there is no
cross contamination, reorificing should be done.
Boiling (kettling) may occur at boiler discharge
temperatures from 170°F to 210°F. The temperature at
which it starts will vary from one installation to
another. The primary cause of the problem is poor heat
transfer on the inside of the boiler coil. This may be
caused by foaming of antifreeze in the system or
scaling from the boiler water if no antifreeze is
present.
There are many manufacturers of plumbing and
boiler antifreezes. Plumbing antifreezes should never
be used in a boiler system because they have no
antifoamants in them. Not all boiler antifreezes have
an effective antifoamant either so the noise may exist
with boiler antifreezes also.
The cure for the boiling noise is the same
regardless of the cause. However, if antifreeze in the
system is suspected of being the cause, the
concentration and type should be investigated before
attempting to eliminate the noise. The most effective
means of cleaning the combustion coil utilizes the
siphon cleaning method. Concentrations of antifreeze
should be kept as low as possible because antifreeze
will reduce heat transfer and efficiency.
Many times it is difficult to determine if the
noise is combustion or boiling related. The best clue is
when in the cycle the noise appears and if its
frequency changes with boiler discharge temperature.
Combustion noises always have the same frequency,
however, their volume may change from the time that
the burner first fires to the time that it shuts off.
Boiling noises have a frequency that varies with boiler
discharge temperature and sometimes they will
disappear completely at higher temperatures just
before the boiler goes off on limit. Vibration of the
boiler pressure gage needle may also occur with
boiling noises.
12C. Insufficient Hot Water
(HW - M2 - series only)
Possible Cause:
a.
No Flow Restrictor
b.
Low limit Failure
c.
Incorrect Wiring of System Circulator
d.
No Flow Check in System Supply
e.
Coil Contamination
The most common cause for insufficient hot
water complaints results from failure to install a flow
restrictor. If there is no flow restrictor water passes
through the coil at a greater volume than the boiler
output is capable of heating to the desired temperature
rise.
Failure of the low limit to operate within its
normal calibration points will have the same effect as
incorrect system circulator wiring.
Incorrect wiring for the system circulator can
also cause the problem. If the blue wire in the field
wiring box is not used to control the circulator or
circulators then the low limit cannot prevent boiler
water temperature from dropping to a point that is
insufficient to provide enough heat for the domestic
hot water coil. The blue wire interrupts power to the
system circulator through the priority relay R-1. R-1 is
controlled by the low limit which should limit
minimum tank temperature to 140°F.
Flow checks in single zone systems and
multizone systems with zone circulators prevent
gravity circulation of heated boiler water from the
OUT OF
PRODUCTION