Assembly instructions – ebm-papst VDC-3-49.15 User Manual
Page 9
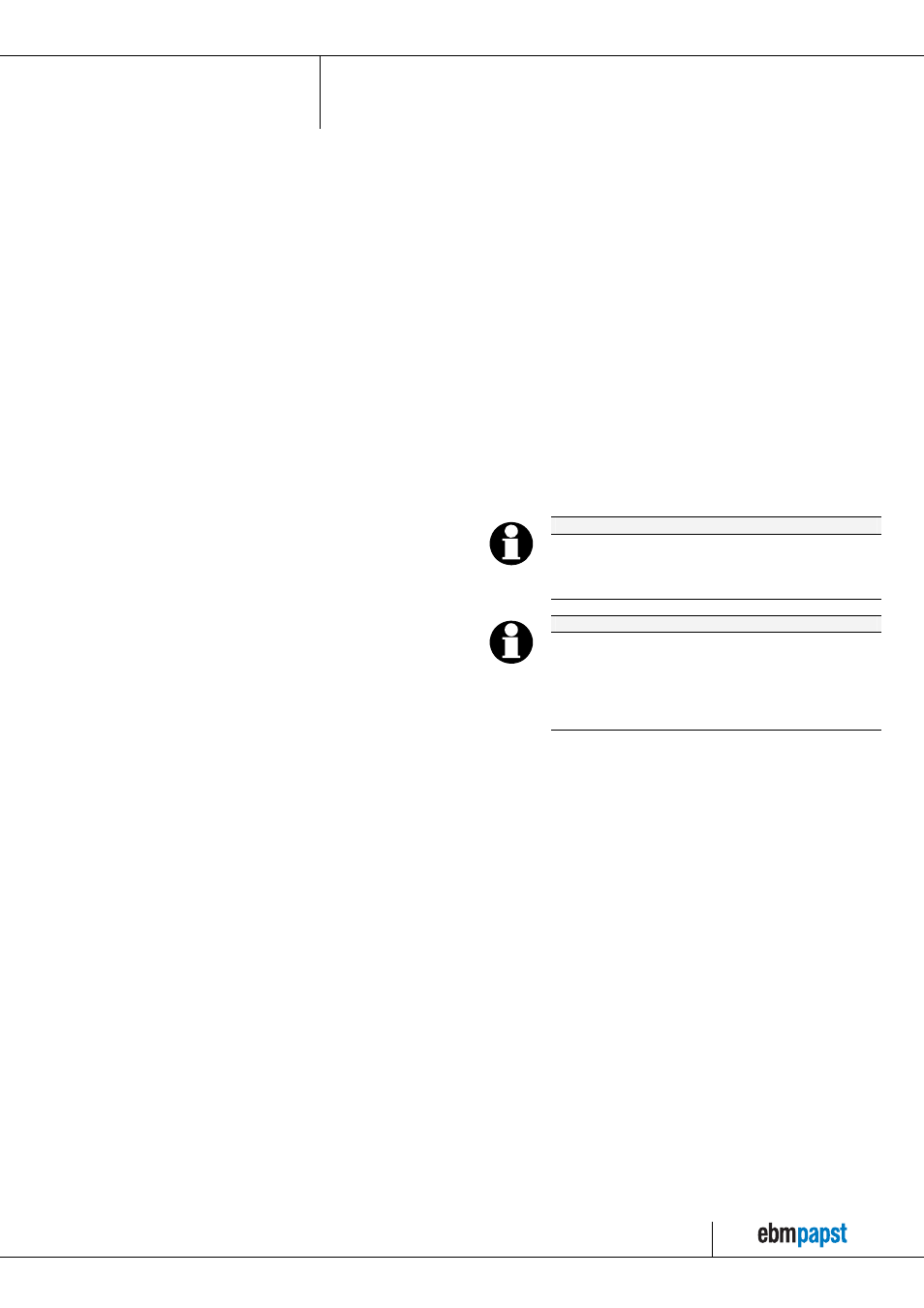
VDC-3-49.15
Assembly instructions
Article No.: 194 0005 008 · Version: V1.0 · dated 08.11.2011 · Page 9 of 14
ebm-papst St. Georgen GmbH & Co. KG · Hermann-Papst-Straße 1 · 78112 St. Georgen · Phone: +49 7724 81-0 · Fax: +49 7724 81-1309 · www.ebmpapst.com · [email protected]
Ori
g
inal installation
5.4 Overvoltage/undervoltage protection function
The protection function takes effect at the limit values listed in the
specification (relative to the terminal voltage U
ZK
).
If one of the switching thresholds is reached, the output stage is switched off
to protect the system and the drive starts freewheeling.
If the drive exceeds the limits for short periods (< 250 ms, occurrence of any
fault peaks in the power supply), it resumes running if the voltage range
returns to a permitted level within this time.
If the limits are exceeded for a longer period (>= 250 ms - interpreted as a
fault in the system), the output stage is shut off and an fault-signal is output
at status output "D".
By acknowledging the enable input "C" (change of signal level 0 to 1), status
output "D" is reset and the drive is again ready for operation.
5.5 Overtemperature protection function
An NTC on the printed circuit board (close to the power stage) protects the
drive from gradual overheating.
If the NTC reaches a temperature of approx. 110 °C, the output stage is shut
off. The status output "D" outputs an fault-signal that remains pending until it
is acknowledged successfully.
After enable input "C" is "acknowledged" with a rising switching edge, the
drive can be switched back on.
If the motor switches off due to overtemperature, for thermal protection of the
drive, successful acknowledgement is not possible until the NTC
temperature falls back below 100 °C.
5.6 I
2
t peak current limitation function
The I
2
t peak current limitation function enables an increase of the torque to
the respective specified peak torque. A so called threshold current is used to
determine the amplitude at which the squaring of the portions of the current
that lie above the threshold value begins.
In the initial state, the threshold current is close to the maximum permitted
winding current, so that depending on the environmental and operating
conditions, it is well possible for the motor to be operated at peak torque for
a number of minutes. If the internal temperature threshold value is reached,
the threshold value of the current is lowered and squaring of the portions of
the current in excess of the threshold value begins. With loading of the I
2
t
memory, the available winding current is then lowered successively; as a
result, the drive is increasingly limited in order to prevent an overload.
5.7 Acceleration and braking ramp function
The maximum possible dynamic behaviour of the drive is defined via an
internally defined parameter value that affects acceleration and braking in
the same way. The slope of the ramp, specified as a max. possible change
of speed per unit of time, is thus limited to the following values:
24 V drive version: max. 16 rpm/ms
48 V drive version: max. 25 rpm/ms
Ex. for the 24 V drive version:
For an external set value jump from 0 to 1600 rpm, the internal set speed of
the motor increases from 0 to 1600 rpm via a corresponding ramp function
within 100 ms.
Usually, this limitation is noticeable only when the motor without load. In this
case, it serves to optimise the control and transient response to the target
speed.
5.8 Safe braking operation
Activating the braking function via control inputs "A/B" or via a negative set
value jump activates a controlled braking operation.
The energy released during braking is fed back and the intermediate circuit
voltage increases. To protect the drive, when the max. reverse voltage is
reached, the braking operation is interrupted and the power stage is disabled
for a short period (freewheeling).
As soon as the voltage falls back below a threshold value defined by a
hysteresis, the braking function is automatically re-enabled, braking energy
is fed back and the intermediate circuit voltage increases again.
This process repeats itself at short intervals until the motor has reached the
new set value speed or has come to a standstill.
5.9 "Zero speed" function
The "Hold zero speed" function can be activated either by specifying a
corresponding speed set value or corresponding signal on the two digital
inputs "A / B".
If an attempt is made to move the motor shaft in this state, the deviation from
the control-set-value is recognized and integrated over the time. The drive
responds with a counterholding torque which increases to the peak torque
depending on the displacement.
NOTE
The "Zero speed" function does not guarantee that a set
position will be maintained exactly.
Æ
Ensure that any slight movement does not have any
harmful consequences.
NOTE
As a result of disturbances, even when the motor is
without load, the rotor can turn a few degrees out of the
original position over time in "Zero speed" operating state.
Exactly maintaining a set position can not be guaranteed.
Æ
Ensure that any slight movement does not have any
harmful consequences.
5.10 Optional functions
According to prior agreement, additional and/or customer-specific functions
can be implemented.
Examples of possible options here include:
• Adaptation of speed control ranges
• Adaptation of application-specific control parameters
• Adaptation of resolution for actual value or encoder signal (possible
depending on speed)
• Speed set value input via PWM signal
• RS-485 as programming and communication interface
For design details of such specific adaptations, refer to the corresponding
product specification.