Assembly instructions – ebm-papst VDC-3-49.15 User Manual
Page 12
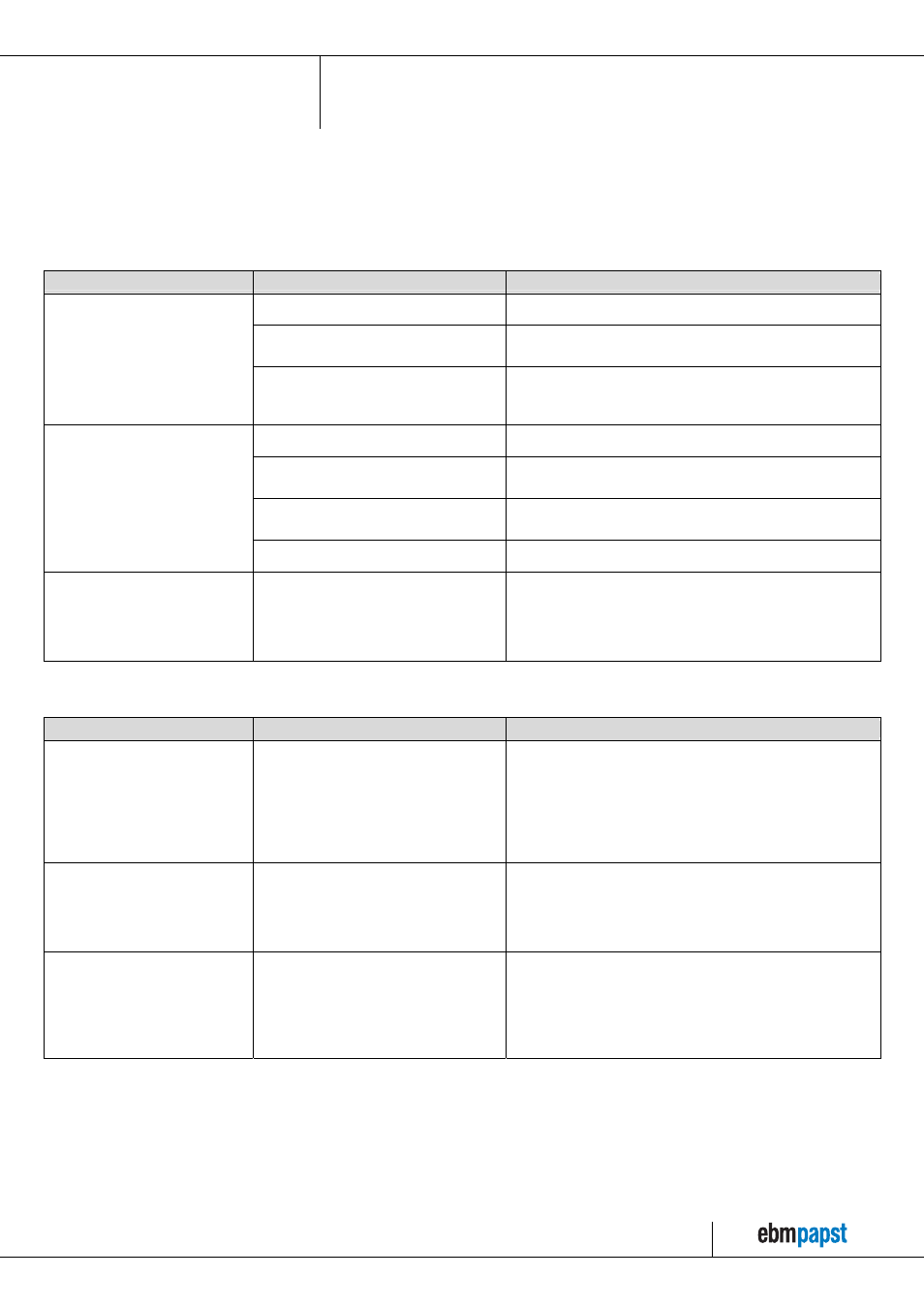
VDC-3-49.15
Assembly instructions
Article No.: 194 0005 008 · Version: V1.0 · dated 08.11.2011 · Page 12 of 14
ebm-papst St. Georgen GmbH & Co. KG · Hermann-Papst-Straße 1 · 78112 St. Georgen · Phone: +49 7724 81-0 · Fax: +49 7724 81-1309 · www.ebmpapst.com · [email protected]
Ori
g
inal installation
7 MAINTENANCE, MALFUNCTIONS, POSSIBLE CAUSES AND REMEDIES
⇒ Do not perform any repairs on your drive system.
⇒ Return the drive system to ebm-papst for repair or exchange.
7.1 Troubleshooting
When switching on
Malfunction / error
Possible cause
Possible remedy
Motor does not start, the power
supply is switched on and within the
specified range
Missing set value signals at inputs S1 and S2
Specify desired set value
Missing digital signal at one of the inputs
(A / B)
Connect at least one of the two inputs for the desired operating
mode/direction of rotation
Missing signal level change (change from
0 to 1) at input "C" to set the motor to ready
state.
Switch on signal level at Input C again (change from 0 to 1)
The motor does not turn, the power
supply and control signals are
connected.
Load/required start-up torque are too high.
Reduce load or check motor dimensioning.
Mechanical blockage
Switch off drive, remove mechanical blockage in the powertrain and
attempt to restart
Faulty connection
Check that pin configuration and control signals are correct, see
Chapter 4 and Chapter 6
Drive defective
Replace drive
Motor accelerates briefly, then
switches off and runs down, fault
signal "D" is set.
High load or high acceleration with power
supply that is not designed to bear this.
Power supply reaches performance limit,
voltage drops sharply and drive detects
undervoltage.
If possible, reduce load or acceleration.
In the other case, check the dimensioning of the power supply and
use a more powerful power supply.
In operation
Malfunction / error
Possible cause
Possible remedy
Motor makes "clacking noises" when
braking function is activated or there
is a negative set value jump
Braking function:
Motor goes into brake operation, the fed-
back energy causes a voltage increase in the
intermediate circuit; when the max. reverse
voltage is reached, controlled brake
operation begins in order to protect the
system (refer to Chapter 5.8).
Use set value ramps instead of set value jumps. If a fast brake
reaction is needed, the fed-back energy can be removed more
quickly via an additional brake chopper in the intermediate circuit.
When operated for longer periods,
the motor torque output declines
Thermal overload: Motor is operated too long
at high load/at elevated ambient
temperature. Motor heating causes lowering
of the winding current by the I
2
t peak current
limitation
Check load point, ambient conditions and possibilities for heat
dissipation.
Reduce load, lower ambient temperature or provide better heat
dissipation.
When operated for longer periods,
the motor stops turning
Thermal overload: Motor is operated too long
at high load/at elevated ambient
temperature. Motor heating finally causes a
shutoff via the integrated temperature
monitoring.
Check load point, ambient conditions and possibilities for heat
dissipation.
Reduce load, lower ambient temperature or provide better heat
dissipation.
The drive cannot be switched on again until the NTC temperature
falls back to <100 °C.