Assembly instructions – ebm-papst VDC-3-49.15 User Manual
Page 10
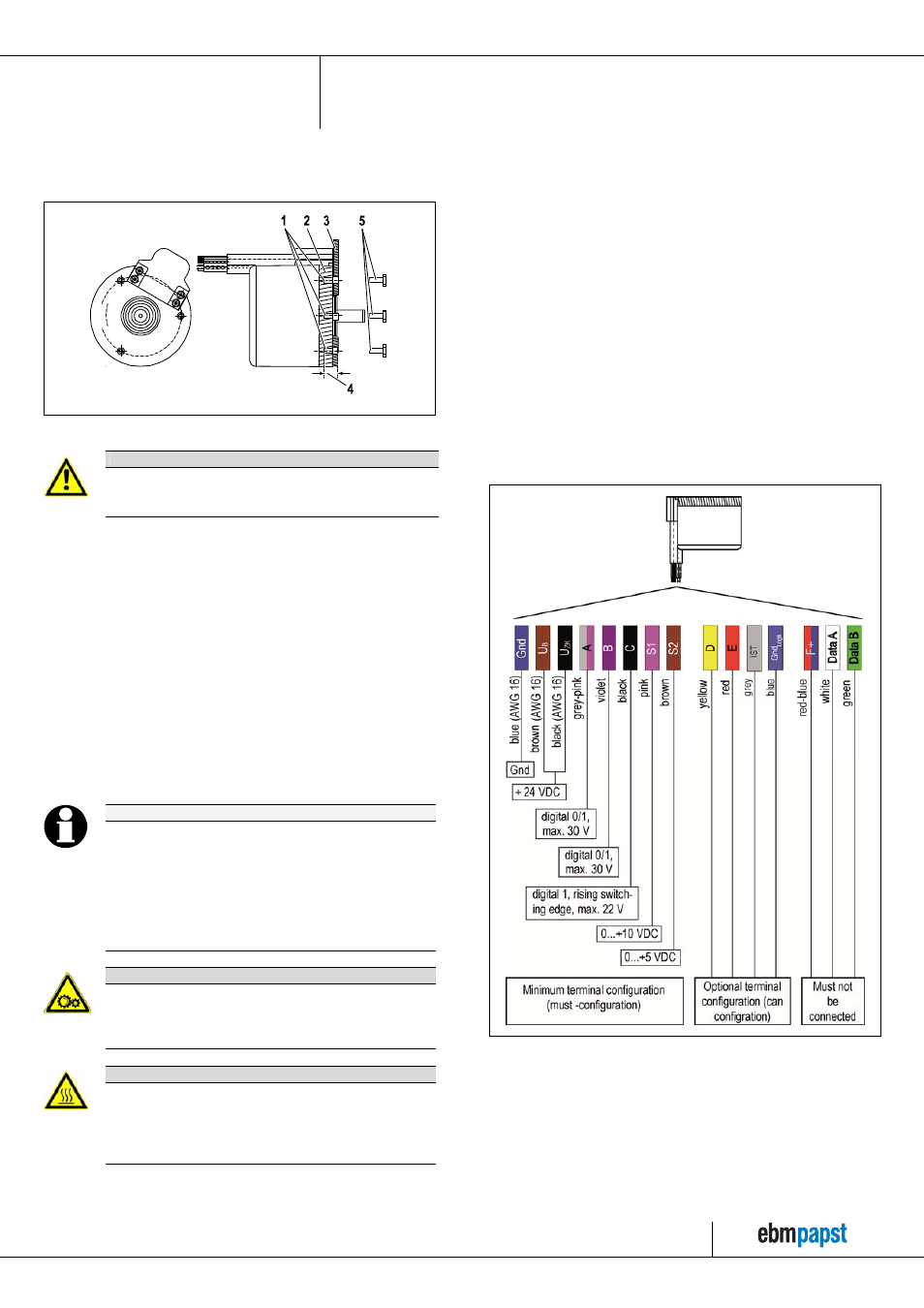
VDC-3-49.15
Assembly instructions
Article No.: 194 0005 008 · Version: V1.0 · dated 08.11.2011 · Page 10 of 14
ebm-papst St. Georgen GmbH & Co. KG · Hermann-Papst-Straße 1 · 78112 St. Georgen · Phone: +49 7724 81-0 · Fax: +49 7724 81-1309 · www.ebmpapst.com · [email protected]
Ori
g
inal installation
6 CONNECTION AND START-UP
6.1 Connecting the mechanical system
Fig.10: Connecting the mechanical system
CAUTION
Motor is heavy.
The motor can fall down and cause crushing injuries.
Æ
Wear safety shoes.
Dimensions and specifications from the product drawing (refer to
Chapter 3.1)
⇒ Adapt the mounting plate [3] to the centring diameter of the motor, pitch
circle and size of the mounting holes.
⇒ Drill the holes into the mounting plate [3].
⇒ Determine the suitable screw length [4]:
Minimum screw length [4] = minimum depth of screw (6.5 mm) +
material thickness of the mounting plate [3].
Maximum screw length [4] = maximum depth of screw (9.5 mm) +
material thickness of the mounting plate [3].
⇒ Screw the self threading screws [5] through the mounting plate [3] into
the motor flange [2].
Use self threading screws according to DIN 7500.
⇒ Tighten the screws [5] equally and tightly, maximum screw-in torque 3
+/- 0.2
Nm.
NOTE
Danger of damage to the bearing system.
When mounting mechanical elements on the motor shaft,
the maximum permitted static axial load of the bearing
system can be exceeded.
Danger of increased running noises, reduced life expectancy of
the drive.
Æ
Observe the maximum permitted static axial load of
300 N.
CAUTION
Danger of being drawn in by rotating shaft.
The rotating shaft can draw in body parts.
Æ
Ensure adequate protection against accidental contact
when installed.
CAUTION
The motor gets hot during operation.
Danger of burn injuries from hot surface.
Æ
Ensure that sufficient protection against accidental
contact is provided.
Æ
Let the motor cool down before touching it.
6.2 Connecting the electrical system
The extensive electrical interface of the motor offers a wide variety of options
for operating the motor and evaluating the signals provided via the interface.
The information from Chapter 4 must be observed.
⇒ Connect the drive system as outlined in Chapter 4.1.
⇒ Before switching on the voltage, ensure that the supply voltage is within
the permitted range (refer to Chapter 3.2 Terminal configuration)
The following illustration shows an overview of the possible terminal
configurations of the motor. For additional information about the individual
inputs and outputs, refer to Chapter 4 of these assembly instructions.
The minimum terminal configuration includes the terminals that have to be
connected at minimum in order to operate the drive.
The optional terminals provide additional options that can be used,
depending on the requirement, as status information, for evaluating the
actual speed or for the separate feed of the logic power supply.
These terminals are not necessary for basic operation.
The last 3 terminals are intended for design variants or for factory-internal
programming and must not be connected on the application side.
Fig.11 Terminal configuration
Note: The unconnected strands must be shortened and/or routed such that
no electrical contact between the wire ends can occur.