Assembly instructions – ebm-papst VDC-3-49.15 User Manual
Page 8
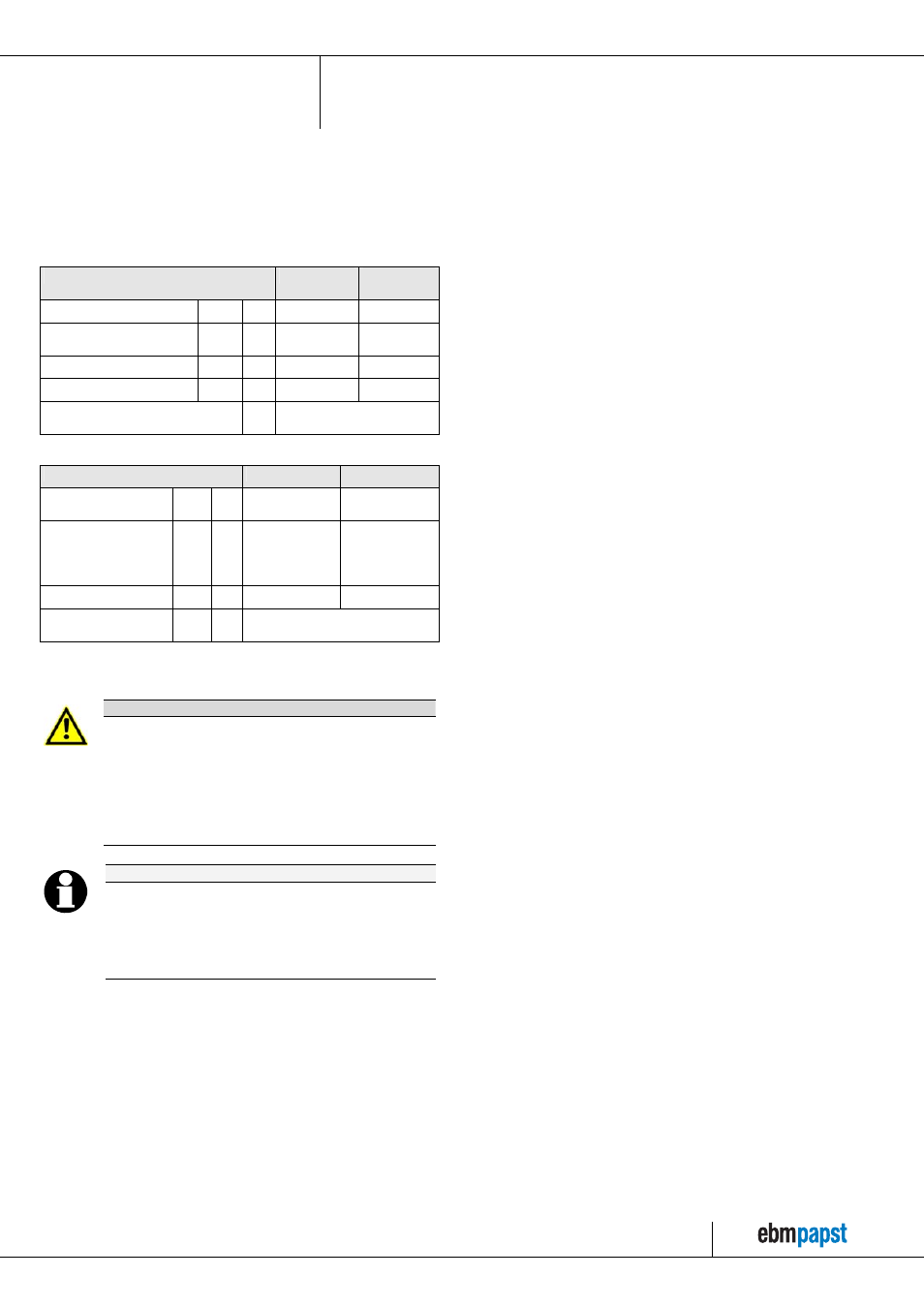
VDC-3-49.15
Assembly instructions
Article No.: 194 0005 008 · Version: V1.0 · dated 08.11.2011 · Page 8 of 14
ebm-papst St. Georgen GmbH & Co. KG · Hermann-Papst-Straße 1 · 78112 St. Georgen · Phone: +49 7724 81-0 · Fax: +49 7724 81-1309 · www.ebmpapst.com · [email protected]
Ori
g
inal installation
4.3 Requirements for the power supply of the drive system
The VARIODRIVE Compact VDC-3-49.15 is designed such that it can be
operated with separate power supplies for the power and logic. This allows,
for example, the power supply to be shut off while the logic power supply for
the motor sensors can remain active.
Power supply
24 V version 48 V
version
Operating voltage range
U
ZK
V
18 to 30
18 to 55
Max. intermediate circuit
voltage ripple
U
ZK
V
≤ 1
≤ 1
Reverse polarity protection
U
ZK
-
No
No
Max. supply current
I
ZK
A <10 <10
Assignment power supply
-
Blue (AWG 16) - "Gnd"
Black (AWG 16) - "U
ZK"
Logic power supply
24 V version
48 V version
Auxiliary voltage supply
range
U
B
V
> 9.5 to < 75
> 9.5 to < 75
Auxiliary voltage supply U
B
-
Short-circuit
proof and
protected from
polarity reversal
Short-circuit
proof and
protected from
polarity reversal
Max. auxiliary current
I
B
mA
< 175
< 175
Assignment of logic
power supply
-
Blue - "Gnd"
Brown (AWG 16) - "U
B
"
Note: When using one voltage source, U
B
and U
ZK
must be bridged. The
bridge is important as otherwise the logic or power supply will be missing
and the drive will not run.
CAUTION
When using two independent voltage sources without a
low-resistance ground connection, potential shifts and
associated compensation currents may result.
Danger of malfunctions or damage to the internal motor
electronics.
Æ
If two separate voltage sources are used for U
B
and U
ZK
,
make a low-resistance connection between the ground of
both voltage sources.
NOTE
Feeding back of power when braking or if in controlled
brake or cycle operation.
A reverse voltage of up to 36 V (for 24 V version) or up to 63 V
(48 V version) can occur. Danger for the power supply.
Æ
When selecting the power supply, ensure corresponding
feedback protection.
5 FUNCTIONAL DESCRIPTION
The VDC-3-49.15 drive system is an electronically commutated external
rotor motor with integrated operating and control electronics. Commutation
takes place in sinus commutation based on a field-oriented control (FOC).
The drive system works as a speed controller with speed limiter and ramp
function as well as with a current controller (torque controller) with torque
limitation.
5.1 Speed set value input function
Note: Specify the speed set value to operate the motor.
According to the illustration in Chapter 4.2 (analogue set value input "S1"),
this input can be used to specify a set value that corresponds to a speed in
the range from 0 rpm to n
max
. Within the power and speed range of the motor
listed in the specification and the listed control accuracy, the drive attempts
to adjust the speed to the specified set value, even when there are load
fluctuations. The same function is also available for the drives in the version
with set value input as a frequency signal. Here, a defined frequency signal
corresponding to the product specification must be applied at input "F+".
5.2 Torque set value input function
Note: Specify the torque set value to operate the motor.
According to the illustration in Chapter 4.2 (analogue set value input "S2"),
this input can be used to specify a set value via this input that corresponds to
a torque in the range from 0 to 100 % (peak torque, see "I
2
t peak current
limitation"). Within the specified tolerance range, the maximum attainable
torque of the drive can be configured. In this way, movement operations can
be limited to a maximum permitted torque if necessary.
In conjunction with a corresponding speed set value, this function enables
torque-controlled winding or coil processes to be implemented, for example.
5.3 Actual value output/encoder signal function
For external monitoring of the actual speed of the drive, the two outputs "E"
and "IST" are available. Each of the two outputs, which are switched as open
collector, deliver a frequency signal with 6 pulses per revolution, for which
the following relationship applies:
Signal frequency * 10 = speed in rpm.
Via the electrical phase offset of 90° of both signals to each other, when
evaluating both channels, an encoder replacement signal with rotation
direction information and 12 pulses per revolution are obtained. For special
designs, a higher number of pulses can also be implemented with a limited
speed range and limited maximum speed. For detailed information in this
regard, refer to the respective product specification.