6 boiler management system (bms), Mode of operation – AERCO BMK 2.0 LN Natural Gas 2008 User Manual
Page 40
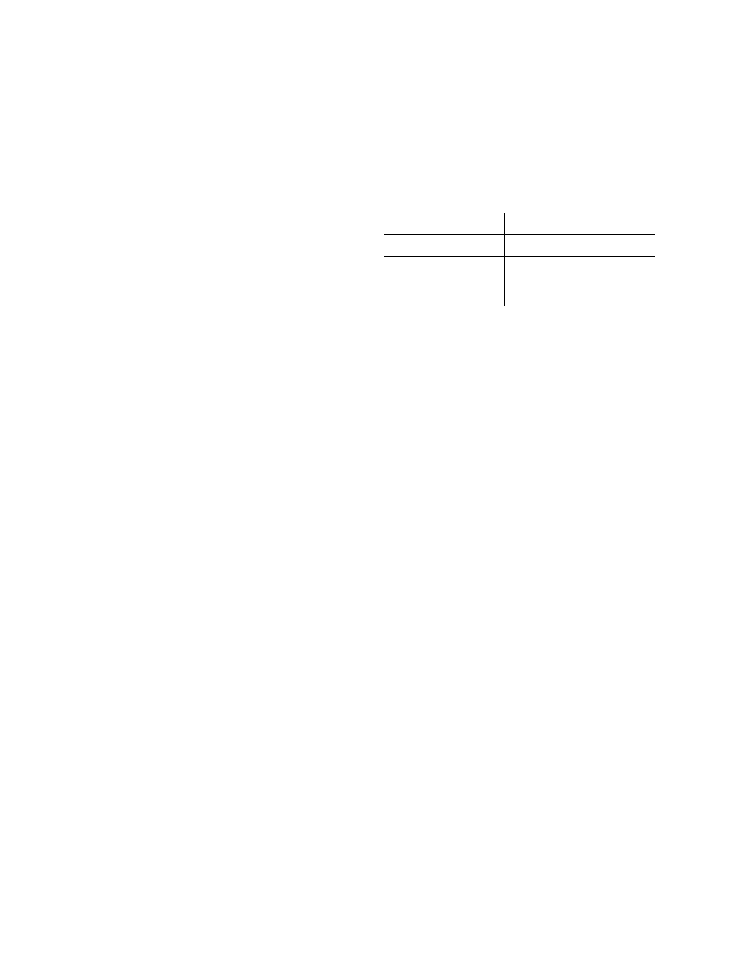
MODE OF OPERATION
If the Network setting is selected for RS485
Modbus operation, a valid Comm Address must
be entered in the Setup Menu. Refer to Modbus
Communication Manual GF-114 for additional
information.
5.5.1 Direct Drive Field Wiring
The only wiring connections necessary for Direct
Drive mode are connection of the remote signal
leads from the source to the unit’s I/O Box. For
either a 4-20mA/0-5V or a 0-20mA/0-5V setting,
the connections are made at the ANALOG IN
terminals in the I/O Box. For a Network setting,
the connections are made at the RS-485 COMM
terminals in the I/O Box. The signal must be
floating, (ungrounded) at the I/O Box and the
wire used must be a two wire shielded pair from
18 to 22 AWG. Polarity must be observed. The
source end of the shield must be connected at
the source. When driving multiple units, each
unit’s wiring must conform to the above.
5.5.2 Direct Drive Startup
Since this mode of operation is factory preset
and the fire rate is being externally controlled, no
startup instructions are necessary. In this mode,
the REMOTE LED will light when the signal is
present.
To operate the unit in manual mode, press the
AUTO/MAN switch. The REMOTE LED will go
off and the MANUAL LED will light.
To change back to the Direct Drive mode, simply
press the AUTO/MAN switch. The REMOTE
LED will again light and the MANUAL LED will
go off.
5.6 BOILER MANAGEMENT SYSTEM
(BMS)
NOTE
BMS Model 168 can utilize either pulse
width modulation (PWM) or RS485
Modbus signaling to the Boiler. BMS II
Model 5R5-384 can utilize only RS485
signaling to the Boiler.
The BMS mode of operation is used in
conjunction with an AERCO Boiler Management
System. The BMS mode is used when it is
desired to operate multiple units in the most
efficient manner possible. The BMS can control
up to 40 boilers; 8 via pulse width modulation
(PWM) and up to 32 via Modbus (RS485)
network communication. For BMS programming
and operation, see GF-108M (BMS Model 168)
and GF-124 (BMS II Model 5R5-384), BMS
Operations Guides. For operation via an RS485
Modbus network, refer to Modbus Communica-
tion Manual GF-114.
To enable the BMS Mode, the following menu
settings must be made in the Configuration
Menu:
MENU OPTION
SETTING
Boiler Mode
Direct Drive
Remote Signal
BMS (PWM Input)
or
Network (RS485)
Refer to paragraph 3.3 for instructions on
changing menu options.
5.6.1 BMS External Field Wiring
Wiring connections for BMS (Model 168) control
using PWM signaling are made between
connector JP2 on the BMS (boilers 1 through 8),
and the B.M.S. (PWM) IN terminals in the I/O
Box on the front of the Benchmark 2.0LN
Boilers. Refer to the wiring diagram provided on
the cover of the I/O Box.
For the BMS (Model 168), RS485 Modbus
control wiring connections are made between
BMS connector JP11 (boilers 9 – 40) and the
RS485 COMM terminals in the I/O Box on the
front of the Benchmark 2.0LN Boilers.
For the BMS II (Model 5R5-384), RS485
Modbus control wiring connections are made
between the BMS II 485 B+/485 A- terminals
and the RS485 COMM terminals in the I/O Box
on the front of the Benchmark 2.0LN Boilers.
Wire the units using shielded twisted pair wire
between 18 and 22 AWG. Observe the proper
polarity for the B.M.S. (PWM) IN and/or RS485
COMM wiring connections. Shields should be
terminated only at the BMS and the boiler end
must be left floating. Each unit’s wiring must
conform to the above.
5.6.2 BMS Setup and Startup
This mode of operation is factory preset and the
AERCO BMS controls the firing rate. There are
no setup instructions for each individual unit.
To operate the unit in manual mode, press the
AUTO/MAN switch. The REMOTE LED will go
off and the MANUAL LED will light
5-4