Rice Lake MSI6260cs Digital Crane Scale Operator Manual User Manual
Page 13
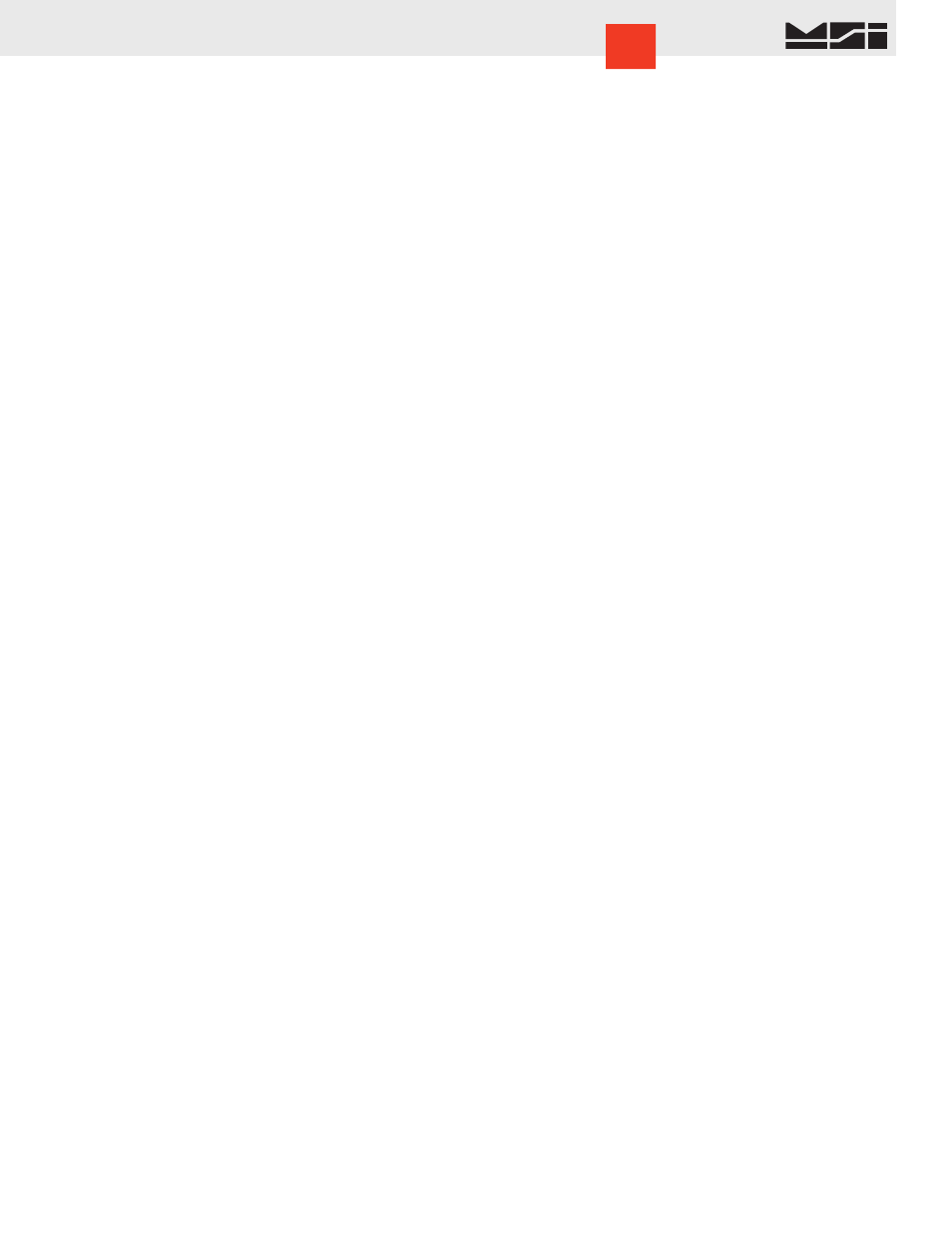
MSI-6260CS Crane Scale™
•
User Guide Page 13
MEASUREMENT SYSTEMS INTERNATIONAL
Rev 1 4/14/06 for SW Ver 5-xx
Calibration Tips
1) Before calibration, exercise the load cell at least 5 times by lifting a test weight having a weight approxi-
mately equal to the system capacity.
2) Make sure that the scale and load are stable (not swinging or vibrating) for every calibration step.
3) Prevent off-center loading during calibration. The scale must be perpendicular to the earth to prevent
cosine theta errors. Adjust the rigging as necessary so that the pull is straight through the center of the
scale.
4) Calibration always starts with the zero load. Remove all rigging that is not always present on the scale.
However, it is sometimes best to calibrate zero with the rigging necessary for picking up the test weights
attached to the scale. It’s effect on dead load can be zeroed out later.
5) If the rigging has not been zeroed out, make sure you add its weight to the test weight when entering the
calibration weight.
6) Multi-point calibration can be done in any random order, as long as the zero step is first.
LEGAL-FOR-TRADE
The 6260CS is designed to meet NTEP requirements (COC pending). The “STANDARD” setting in the
embedded CellScale must be set to NTEP. See the 9000 User Guide for details on NTEP operation and setting
the operating Standard.
Enabling the NTEP mode requires that you designate a control device for the crane scale. Only one control
device is allowed to change metrologically significant parameters such as Zero or Tare. All other remote
devices can display weight but cannot control the scale.
Unless you are actively involved in Legal-For-Trade activity, do not enable the NTEP mode due to the limi-
tations it causes in the use of peripheral equipment. The Industrial standard is just as accurate if calibrated
properly, and allows multiple controller/indicators.
SEALING THE MSI-6260CS CRANE SCALE
The 6260CS is sealed with a standard lead-wire seal. The seal is used to prevent removal of the seal screw cov-
ering the calibration enable switch. The wire is passed through the seal screw and through two adjacent screws
in the front casting (figure 3-1). Use seal wire with a maximum diameter of .040” (1mm). 20 Gauge or smaller
wire is appropriate.
Once all channel parameters are set and calibrations completed replace the seal screw and tighten down
securely to ensure a water proof seal.
The rear casting assembly (Battery Well) must also be sealed to prevent access to the electronics (figure 3-2).
This seal does not need to be broken to calibrate the system. Only the front casting wire must be broken to
provide access to the calibration menus.