Canopen interface description – Baumer GK473 User Manual
Page 9
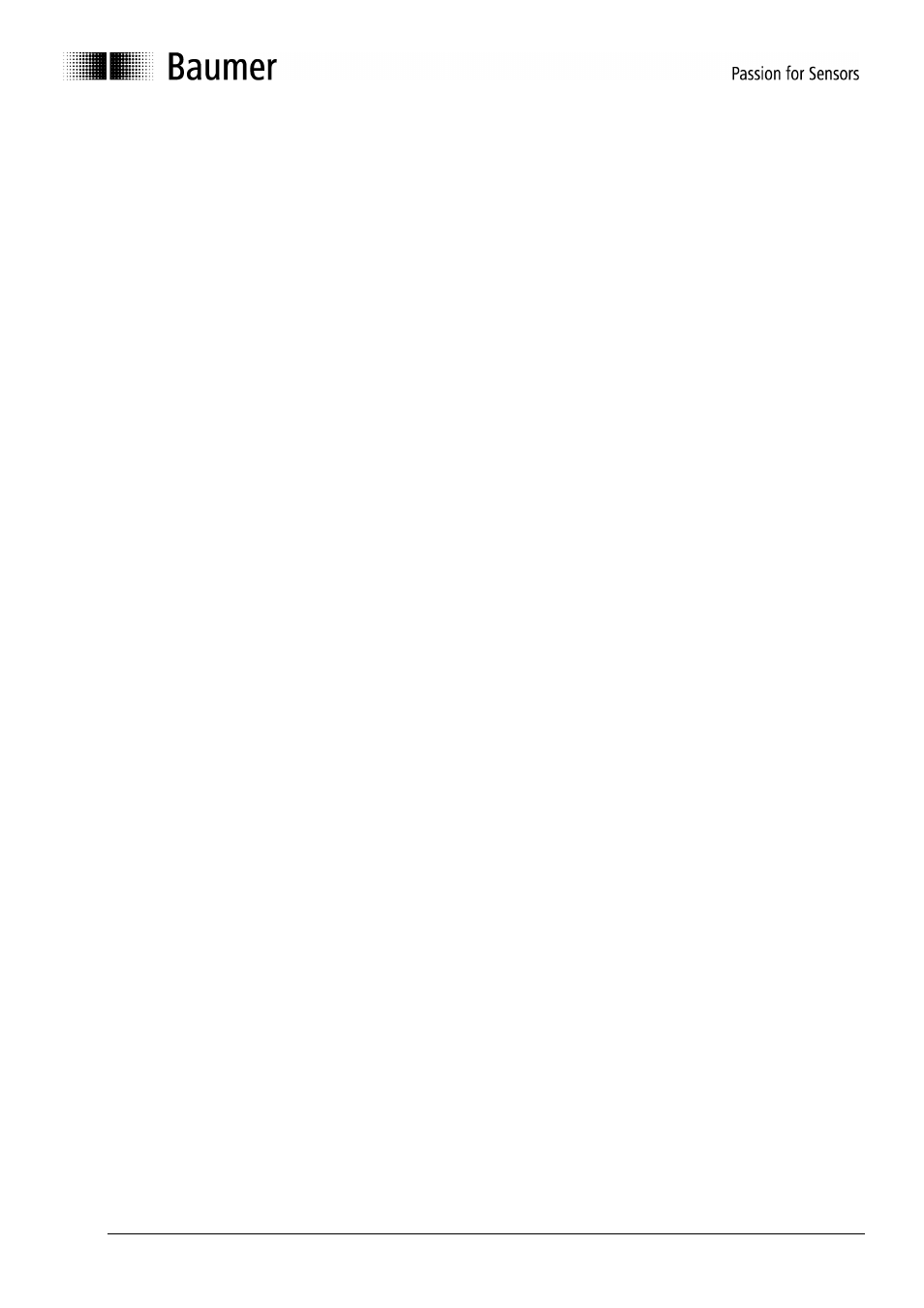
Manual_GK473_CANopen_EN.doc
9/24
Baumer IVO GmbH & Co. KG
04.05.11
Villingen-Schwenningen,
Germany
5. CANopen interface description
5.1. General
information
The gateway enables data communication between the SPA’s RS485 protocol and the CAN bus
protocol.
CAN bus (CAN: Controller Area Network) was originally designed by Bosch and Intel as rapid and
cheap means of data transmission in automotive industry. Today, CAN bus is also applied in industrial
automation.
CAN bus is a fieldbus (with standards defined by the CAN in Automation Association CiA) where
devices, actuators and sensors of different manufacturers communicate with each other.
The CANopen profile based on layer 7 of the CAL (CAN-Application Layer) was developed under the
technical administration of the Steinbeis Transfer Centre for Automation. Compared to CAL, CANopen
provides only the functions appropriate for applications in automation. This way CANopen is a CAL
excerpt optimized for use in automation. It enables improved system init as well as utilizing simplified
devices. CANopen is optimized for rapid data exchange in real-time systems.
CANopen means:
• Easy access to all device and communication parameters
• Synchronisation of several devices
• Automatic network configuration
• Cyclic and event-triggered process data traffic
CANopen comprises four communication objects (COB) with different characteristics:
• Process data objects for real-time data (PDO)
• Service data objects for parameter and program transmission (SDO)
• Network management (NMT, Heartbeat)
• Pre-defined objects (for synchronisation, emergency signals)
Since there is no standard profile for this kind of gateway it is manufacturer-specific.
5.2. Data transfer structure
The PLC data message (by the CANopen Master) output to the gateway implies the complete
command for the intended spindle position display. The command is completed by header and footer
info as well as CRC check sum and transmitted by the gateway via RS485.
Vice-versa, header and footer info together with the CRC check sum are deleted from the RS485
message. All other contents remain unchanged and are transmitted as data block of a CANopen
message available at the PLC as consistent input data.
The gateway further provides some supplementary functions to relieve the master PLC and to simplify
programming operations.