06 basic welding technique, Basic welding technique -5 – Tweco FP-165 Mini MIG Portable MIG Welder User Manual
Page 36
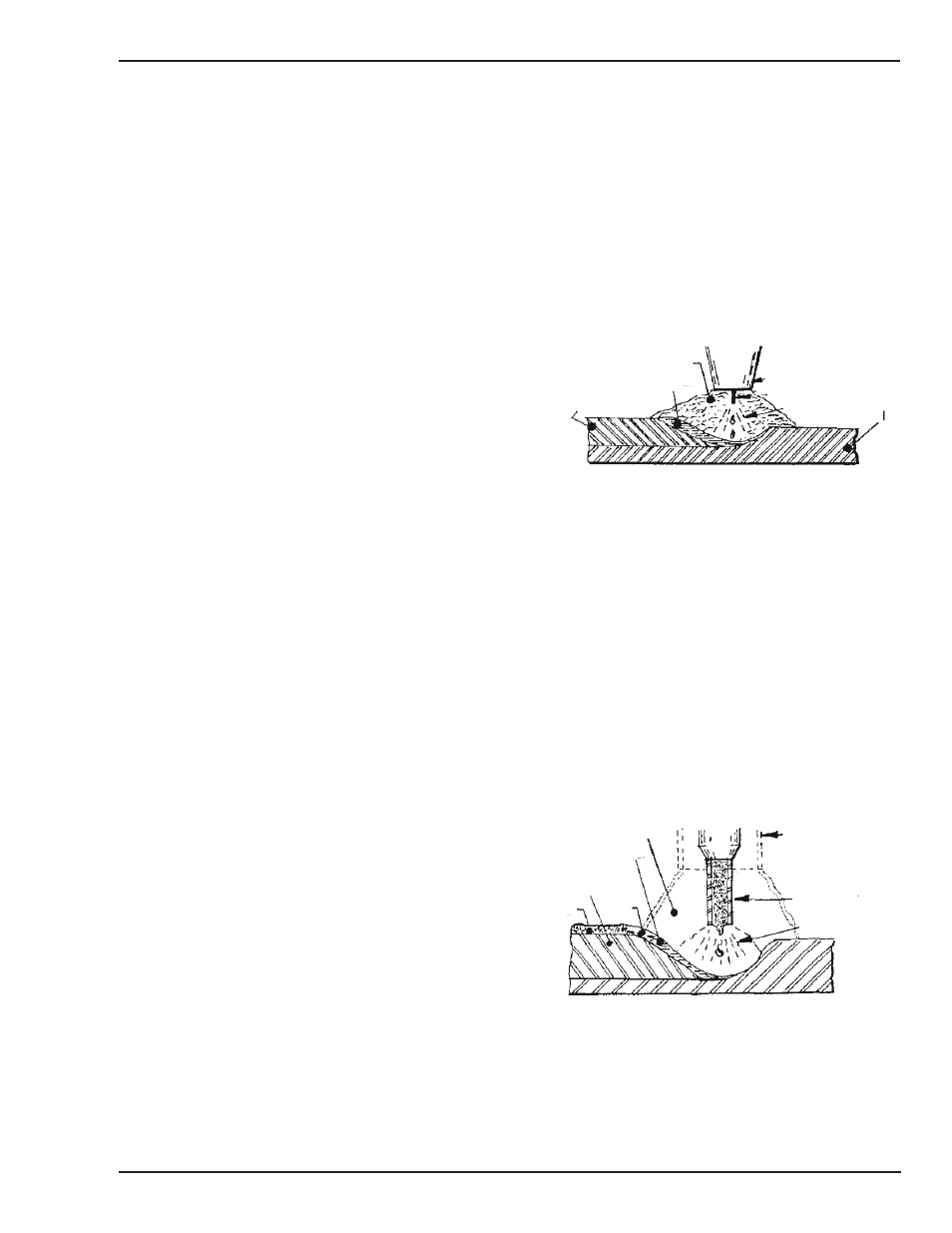
OpERATION
FIREpOwER Fp-125, 135, 165
Operation
4-5
Manual 0-5123
4.06 Basic Welding Technique
General
Two different welding processes are covered in this
section, with the intention of providing the very basic
concepts in using the semi-automatic mode of welding.
In this mode, the welding gun is hand-held. The electrode
(welding wire) is then fed into a weld puddle and the arc
is shielded by a gas or gas mixture.
Setting of the power Supply
The settings of the FirePower requires some practice by
the operator in that the welding Power Supply has two
control settings that need to balance. These are the Wire
Speed control and the Voltage Control switches. The
welding current is determined by the Wire Speed control
(i.e., the current will increase with increased wire speed,
resulting in a shorter arc). Slower wire speed will reduce
the current and lengthen the arc. Increasing the welding
voltage hardly alters the welding current level, but length-
ens the arc. By decreasing the voltage, a shorter arc is
obtained with little change in welding current.
When changing to a different electrode wire diameter,
different control settings are required. A thinner electrode
wire needs more wire speed to achieve the same current
level.
A satisfactory weld cannot be obtained if the wire speed
and voltage switch settings are not adjusted to suit the
electrode wire diameter and dimensions of the work
piece.
If the wire speed is too high for the welding voltage,
“stubbing” will occur as the wire dips into the molten pool
and does not melt. Welding in these conditions normally
produces a poor weld due to lack of fusion. If however,
the welding voltage is too high, large drops will form on
the end of the electrode wire, causing spatter. The cor-
rect setting of voltage and wire speed can be seen in the
shape of the weld deposit and heard by a smooth regular
arc sound.
GAS METAL ARC WELDING (GMAW)
This process, also known as MIG welding, CO2 welding,
Micro Wire Welding, short arc welding, dip transfer weld-
ing, wire welding etc., is an electric arc welding process
which fuses together the parts to be welded by heating
them with an arc between a solid, continuous, consum-
able electrode and the work. Shielding is obtained from
an externally supplied gas or gas mixture. The process is
normally applied semi-automatically; however the process
may be operated automatically and can be machine oper-
ated. The process can be used to weld thin and fairly thick
steels, and some non-ferrous metals in all positions.
Base Metal
Arc
Electrode
Nozzle
Shielding Gas
Weld Metal
Solidified Weld
Metal
Art: A-05103
Figure 4-3: GMAW Process
FLUX CORED ARC WELDING (FCAW)
This process also known as Open arc, Innershied, FAB
Shield, etc., is an electric arc welding process which fuses
together the parts to be welded by heating them with an
arc between a continuous flux filled electrode wire and
the work. Shielding is obtained through decomposition of
the flux within the tubular wire. The process is normally
applied semi-automatically; however the process may be
applied automatically or by machine. It is commonly used
to weld large diameter electrodes in the flat and horizontal
position and small electrode diameters in all positions. The
process is used to a lesser degree for welding stainless
steel and for overlay work.
Arc
Flux Cored
Electrode
Nozzle (optional)
Gas (optional)
Molten Metal
Molten
Slag
Solid Weld
Metal
Slag
Art: A-05104
Figure 4-4: FCAW Process