Tweco PAK 10 User Manual
Page 23
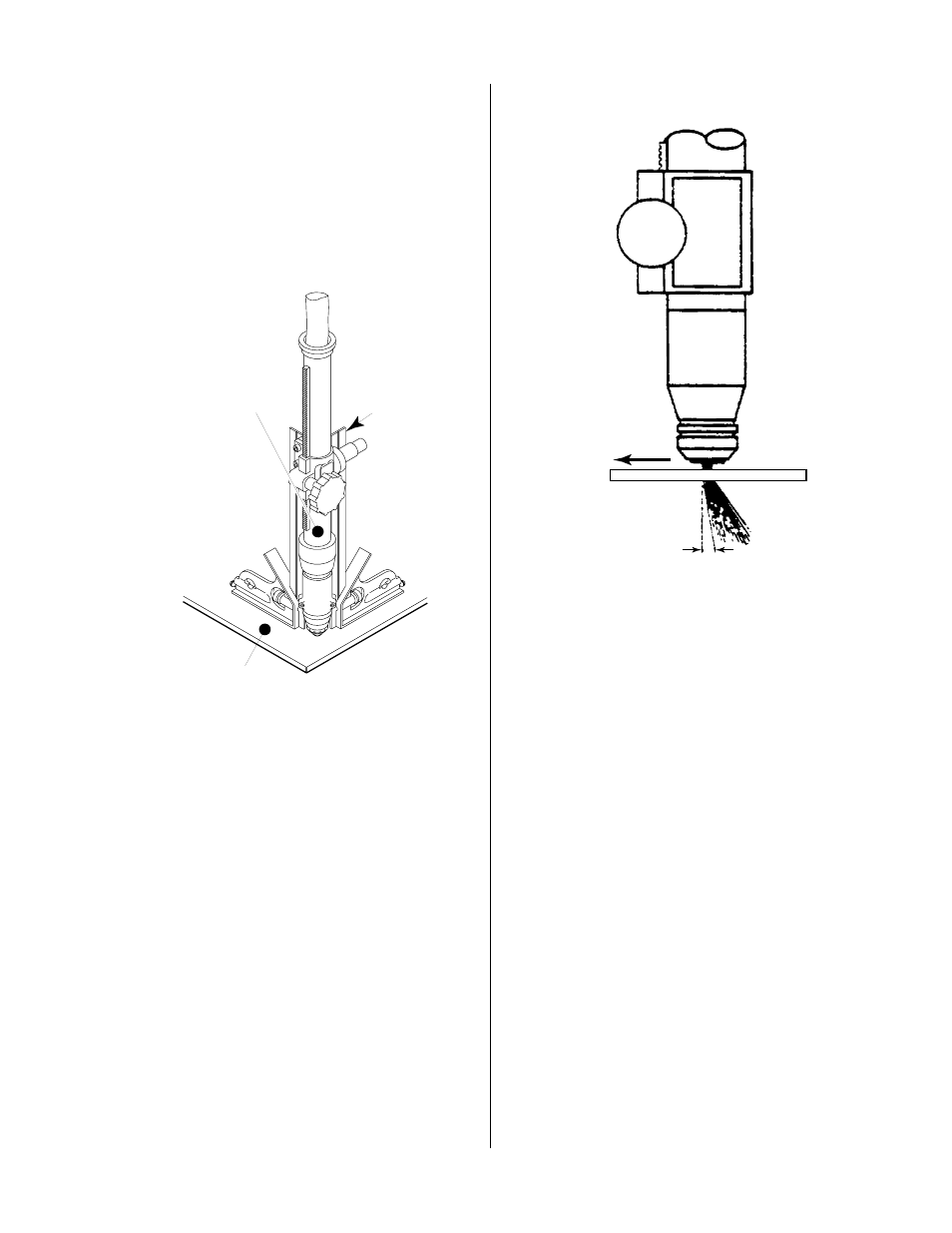
Manual No. 0-0515
11
Operation
MACHINE TORCH OPERATION
When cutting with a machine torch, the torch must be
at right angles to the plate to obtain a clean, vertical
cut. Use a square, as shown in Figure 3-D, to align the
torch. It is good to start a cut at a slow speed and in-
crease the speed to obtain the desired cut quality. Table
3-B gives typical cutting speeds for various materials
and material thicknesses.
A-00175
Rack and
Pinion Mounting
Assembly
Square
Workpiece
Figure 3-D Using a Square to Set Up the Machine
Torch
To start a cut at the plate edge, line up the torch away
from the plate, and press the control switch. The trans-
ferred cutting arc will then be established at the plate
edge. Adjust cutting speed for good cutting perfor-
mance, as indicated by a trailing arc of approximately
5° (Figure 3-E). When cutting expanded metal the cut-
ting arc and pilot arc will alternate establishing them-
selves automatically.
5˚ Approximately
Direction Of
Travel
A-01919
Figure 3-E A Good Cut Will Produce a Trailing
Arc of Approximately 5°
PIERCING
In some cutting operations, it may be desirable to start
the cut within the plate area rather than at the plate
edge. Piercing the plate is not recommended on plates
thicker than 3/4" (19 mm), based on a 5/16" (7 mm)
standoff, using a mechanized torch with a “running
start” and a maximum time to complete pierce of 3 sec-
onds). Blowback from the piercing operation can
shorten the life of torch parts. All piercing should there-
fore be done as quickly as possible with current set at
100 amperes.
A method called “running start” is recommended when
piercing with a machine mounted torch. Position the
torch off the cutting line a sufficient distance to allow
the pierce to be made before reaching the cutting line.
This allowance depends on the thickness of the mate-
rial and the travel rate of the mechanized torch.