System overview, 6 supplied system software, 2 vehicle detection applications (output #1) – Banner A-GAGE MINI-ARRAY Series User Manual
Page 5: 3 trailer hitch detection applications (output #1), 4 system self-diagnostics (output #2)
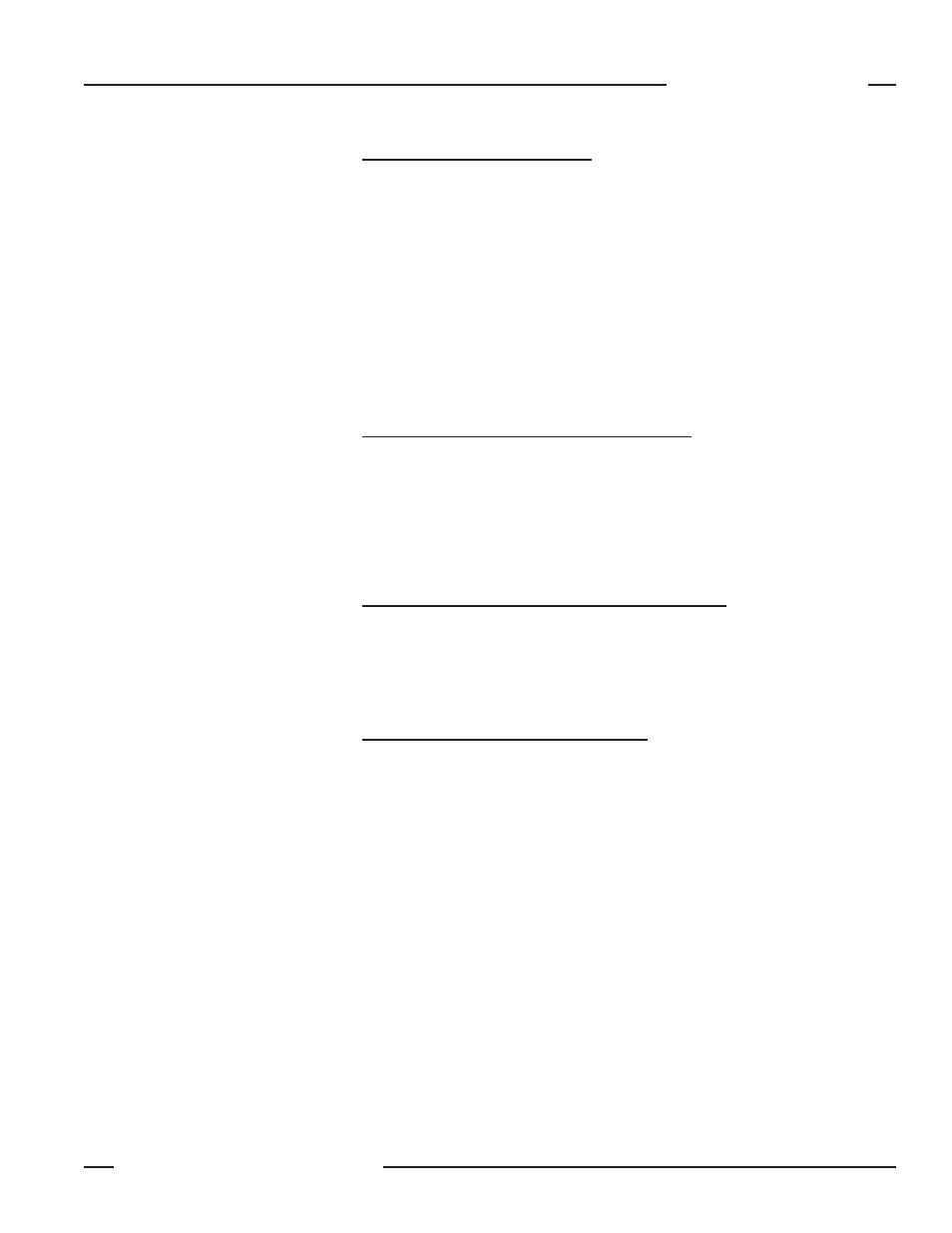
P/N 117167 rev. A
5
Banner Engineering Corp.
•
Minneapolis, MN U.S.A.
www.bannerengineering.com • Tel: 763.544.3164
MINI-ARRAY
®
Two-Piece Measuring Light Screen
System Overview
1.1.6 Supplied System Software
The system provides other scanning modes and operation features, which are not
optimized for vehicle separation but are useful for other applications.
These features are easily accessed via a simple-to-use Banner-supplied PC
software program and an appropriate EIA-485 interface (consult a Banner
Engineering representative for more information). The PC software can be run
on any computer running Windows
®
98, NT, ME, XP or 2000. The menu-driven
program walks the user through the many scanning and output options. After the
desired options are selected, download the settings to the receiver; the receiver will
store the configuration settings in non-volatile memory.
This software also enables the user to check sensor alignment, obtain sensor
readings, and verify sensor status. The built-in system diagnostics can be used to
assess emitter and receiver hardware errors or dirty lens locations.
1.2 Vehicle Detection Applications (Output #1)
The MINI-ARRAY Two-Piece Light Screen features a superior interlaced (cross-
hatched) beam pattern. When the light screen is clear (no object is obstructing
the receiver’s view of the emitted beam pattern), the sensor will ignore small
objects while waiting to detect the beginning of a vehicle. Up to 125 mm (5”) of
consecutive light channels must be blocked before a valid object is detected; once
the sensor detects 125 mm or more of consecutive blocked light, Output # 1 will
become active (output ON).
1.3 Trailer Hitch Detection Applications (Output #1)
Once an object is detected (see Section 1.1.1), Output #1 will remain active until
the receiver again detects the entire emitter beam pattern (sensor is clear). The
interlaced scan pattern will detect smaller objects after initially detecting a vehicle,
even if only one beam is obstructed. Once the receiver detects a fully unobstructed
light screen, Output #1 again will become inactive (output OFF).
1.4 System Self-Diagnostics (Output #2)
Advanced electronic and data processing allows the receiver to continually monitor
and evaluate light signal quality and alert the user to light signal degradation or
sensor faults. The sensor can detect marginal alignment, permanently blocked
channels, a faulty emitter element, or a non-functioning emitter.
This receiver was designed to detect system failures and remain operational.
Potential problems include a dirty lens that totally blocks (occludes) the optical
light signal or a light signal failure (caused by either the emitter or receiver).
Although sensor failures are rare, the Two-Piece MINI-ARRAY has been designed
to continue to function while warning the user of fault conditions, minimizing
system down time and providing advance notice that system maintenance or
repairs are required.
Whenever the receiver detects proper operation, Output #2 is active (ON). When
the sensor detects a system problem (either a sensor fault or a degraded signal),
Output #2 is disabled (goes OFF, an alarm condition).
A system problem is acknowledged in three ways:
1. The condition of the diagnostic LEDs,
2. Output #2 will be inactive (OFF), and
3. The condition can be transmitted to the monitoring system, via the EIA-485
interface (see Appendix A, System Status Information: command 0x66).