Warning – Banner OMNI-BEAM Series User Manual
Page 8
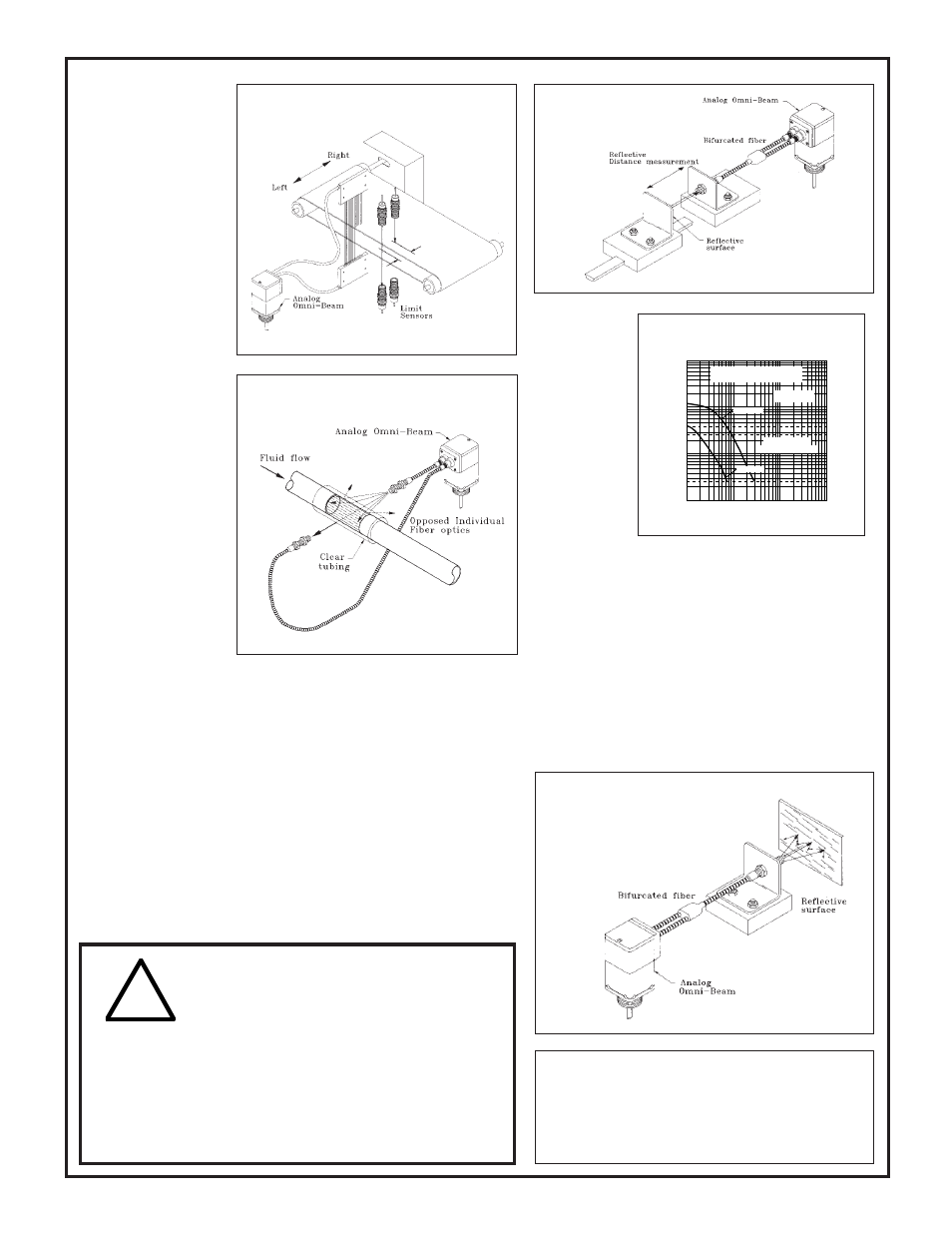
Banner Engineering Corp., 9714 10th Ave. No., Minneapolis, MN 55441
Telephone: (612) 544-3164 FAX (applications): (612) 544-3573
WARRANTY: Banner Engineering Corporation warrants its prod-
ucts to be free of defects for one year. Banner Engineering Corportaion
will repair or replace, free of charge, any product of its manufacture
found to be defective at the time it is returned to the factory during the
warranty period. This warranty does not cover damage or liability for
the improper application of Banner products. This warranty is in lieu
of any other warranty, either expressed or implied.
!
WARNING
These analog photoelectric sensors do
NOT include the self-checking redundant circuitry necessary
to allow their use in personnel safety applications. A sensor
failure or malfunction can result in either a high or a low sensor
output voltage.
Never use these products as sensing devices for personnel protection. Their use
as safety devices may create an unsafe condition which could lead to serious injury
or death.
Only MACHINE-GUARD and PERIMETER-GUARD Systems, and other sys-
tems so designated, are designed to meet OSHA and ANSI machine safety
standards for point-of-operation guarding devices. No other Banner sensors or
controls are designed to meet these standards, and they must NOT be used as
sensing devices for personnel protection.
Figure 15.
Fiber optic opposed edge guiding
Figure 17.
Fiber optic diffuse
distance measurement
Figure 19.
Surface reflectivity monitoring
Figure 16. Turbidity monitoring
Fotonic™ is a trademark of MTI Instruments Division
of Mechanical Technology Incorporated
1
.1
DISTANCE
10
100
.1 IN
1 IN
10 IN
100 IN
OASBF
Range based on 90%
reflectance white test card
Diffuse mode
with BT23S fiber
E
X
C
E
S
S
G
A
I
N
I
Max. NULL
4
2.7
.25
Min. NULL
Figure 18. Excess gain:
OASBF
grees, etc) from the perpen-
dicular to the specular sur-
face that is to be monitored
for angular skew.
Opposed fiber optics may
be used to measure the width
(profile) of an object as a
function of the percentage
of the beam that it blocks.
This same approach is used
for monitoring the position
of the edge of an opaque
material. One common ap-
plication is edge-guiding, as
shown in Figure 15. Glass
fiber optics with rectangu-
lar terminations serve an
important role in many size
and position monitoring
applications.
Opposed fiber optics are
commonly applied for
monitoring the optical clar-
ity of a material. For ex-
ample, a clear section of tub-
ing is often inserted along a
gas or liquid pipeline, and
opposed fiber optics are used
to establish a light path
across the centerline of the
tubing (Figure 16). Turbid-
ity, chemical change, pol-
lutants, etc. may affect the
amount of light transmitted
across the clear section. The
light source of models
OASBF and OASBFX is
infrared (invisible) and the light source used for models OASBFV and OASBFP is
visible red. The light-absorbing characteristics of the material being monitored may
dictate the use of either visible red or infrared light. Whenever necesary, please contact
your Field Sales Engineer or the Banner Application Engineering staff to discuss your
particular sensing requirements.
Bifurcated fiber optics:
Bifurcated fiber optics may sometimes be successfully applied to monitor distance to
a surface (Figure 17). As the excess gain curve in Figure 18 suggests, distance
measurement with bifurcated fiber optics is possible only over relatively short ranges.
Repeatability of distance sensing with bifurcated fiber optics demands that the reflectivity
of the surface and the viewing angle to the surface remain constant. Once the relative
reflectivity of the surface to be monitored is known, the desired response to the predicted
displacement can be obtained through selection of sensor head and fiber (or fiber bundle)
size. Your Banner Field Sales Engineer or Factory Applications Engineer can assist you
with the best selection.
Bifurcated fiber
optics may be
used for moni-
toring the reflec-
tive characteris-
tics of a material
surface that
maintains ists
distance and ori-
entation to the
sensing end tip
(Figure 19). The
visible red light
sources of mod-
els OASBFV
and OASBP are particularly useful for monitoring reflectivity
differences due all or in part to color change.
Fotonic
™
sensors are laboratory grade systems which use a bifur-
cated fiber optic assembly as the sensing component for non-
contact measurement of surface conditions or any variable (e.g.
force, temperature, pressure, etc.) that can be converted to dis-
placement. Banner Analog OMNI-BEAM sensors are not meant
to replace fotonic systems. However, with careful selection of
sensor head and fiber optic assembly, a fiber optic analog OMNI-
BEAM system may function adequately in some small displace-
ment sensing applications.