Bendix Commercial Vehicle Systems COMPACT 500 9/87 User Manual
Page 23
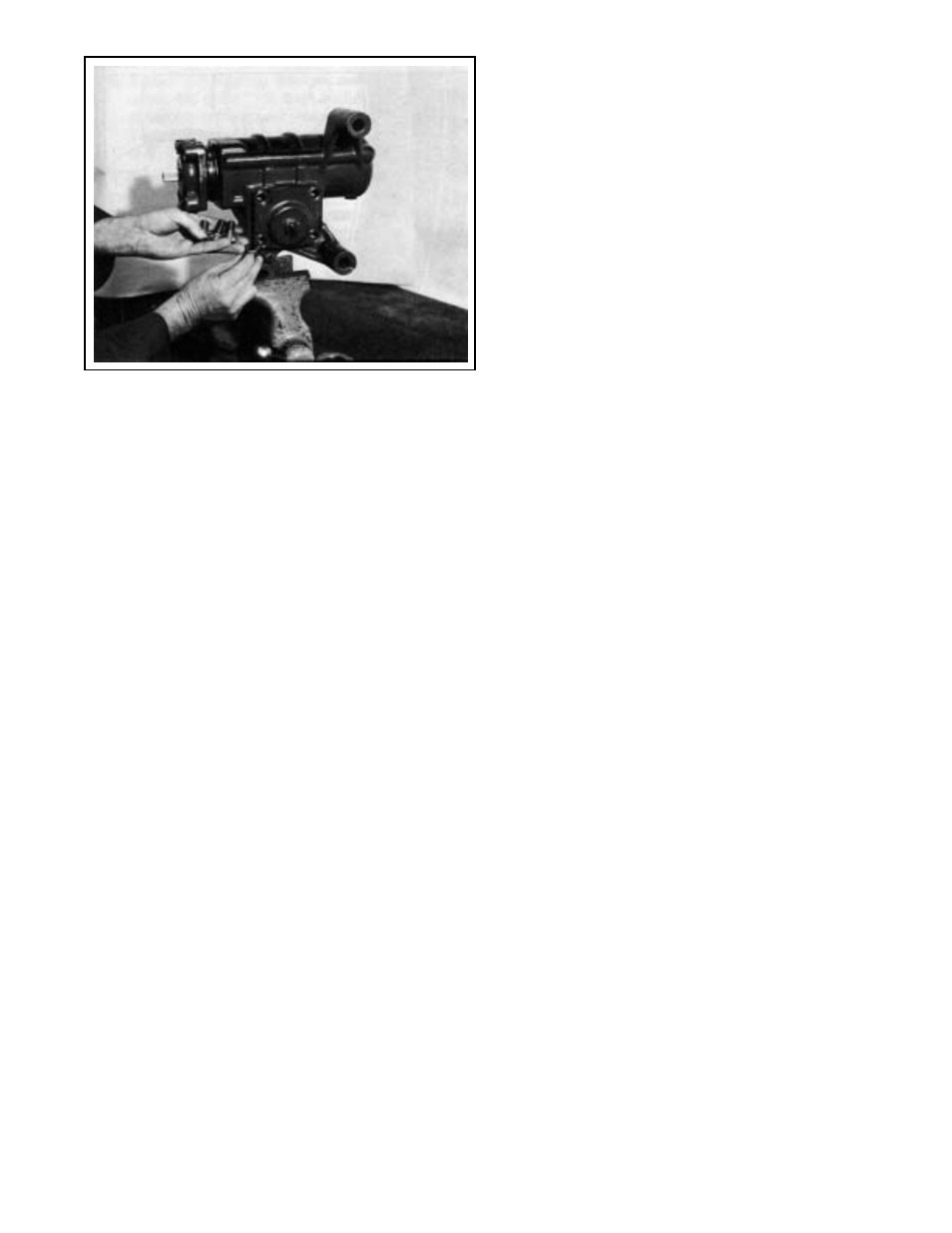
23
FIGURE 48
Install the four washers(2) and the four bolts(42) that
secure the side cover to the housing and torque to 96
ft.lbs. with a 22mm wrench. (See Figure 48)
ADJUSTING THE PISTON - SECTOR TOOTH
BACKLASH
11. The piston and output shaft gear backlash is correct
when a 4 to 18 inch pound increase in torque is noted
as the input shaft is rotated and the piston passes
through the mid point of its total travel in the housing.
The torque increase on the input shaft will occur only
as the piston travels through the mid point of its travel
and should disappear as the piston moves past the mid
point.
To obtain the above adjustment, rotate the input shaft
180° in both directions past the mid point of piston travel.
(The mid point of piston travel is approximately one half
the number of input shaft revolutions possible.)
Each time the direction of input rotation is changed, turn
the output shaft adjustment screw(36) clockwise 1/8 to
1/4 turn. Continue this procedure until the 4-18 inch pound
increase in torque is noted.
NOTE: A 19mm 12 point socket wrench can be used
to rotate the input shaft.
When the adjustment is correct, install lock nut(43) and
apply a torque of 103 ft. lbs with a 24mm torque wrench
while holding the adjusting screw in position with the
9mm socket.
12. After all the described steps have been performed, check
that the power steering unit runs smoothly throughout
its entire motion and that the backlash at the center
position is as prescribed in Step 11 above.
13. Install the pitman arm(22) on the output shaft and secure
it using washer(21) and nut(20). Torque nut to 370-410
ft. lbs.
14. Install the gear on the vehicle and test for flow and
pressure values shown in Section III of Technical Data.
X. PRESSURE, FLOW AND LEAKAGE TESTS
PRELIMINARY
1. Connect Rotunda analyzer kit 14-0230 or equivalent to
the power steering system as shown in Figure 49. Be
sure shutoff valve is fully open.
2. Put front wheels in straight ahead position, transmission
in neutral, parking brake engaged.
3. Start engine and partially close the pressure line shutoff
valve until 800-1000 p.s.i. is read at the pressure gauge.
When temperature of power steering fluid in the
reservoir reaches 120°F, fully open shutoff valve and turn
engine off.
SYSTEM BACK PRESSURE CHECK
1. Insure shut off valve is fully open.
2. Start engine and increase speed to 2200 r.p.m. When
fluid temperature reaches 130°F (55°C), record flow
rate and pressure.
A. If flow is below 3.5 g.p.m. (13.2 L/min.). Check to
see if correct pump is installed. If correct, continue
testing to find problem.
B. If pressure exceeds 80 p.s.i. (552 kPa), check lines
for kinks or obstructions. If none are found and
pressure remains high, continue testing to find
problem.
MINIMUM PUMP FLOW
1. Decrease engine speed to 600 rpm.
2. Slowly close shutoff valve to increase pressure to 1200
p.s.i.
3. Record flow rate at 130°F (55°C).
4. If flow rate is below 2.2 g.p.m. (8.3 L/min), then verify
correct pump is installed. Pump may require repair or
replacement especially if flow at 2200 r.p.m. was also
below specification.
RELIEF PRESSURE TEST - POWER STEERING
PUMP
1. With the engine running at 600 r.p.m. close the shutoff
valve and read the pressure gauge and note the flow
rate is 0. OPEN THE SHUTOFF VALVE QUICKLY after
reading the gauge pressure and note the flow rate returns
to normal. If the pressure reading is below 1800 p.s.i. or
above 2250 p.s.i., repair or replacement of the relief valve
is necessary.
CAUTION: The shutoff valve must not remain closed
longer than FIVE SECONDS or damage to the pump
may result.