Rockwell Automation SA500 AC Power Modules User Manual
Page 41
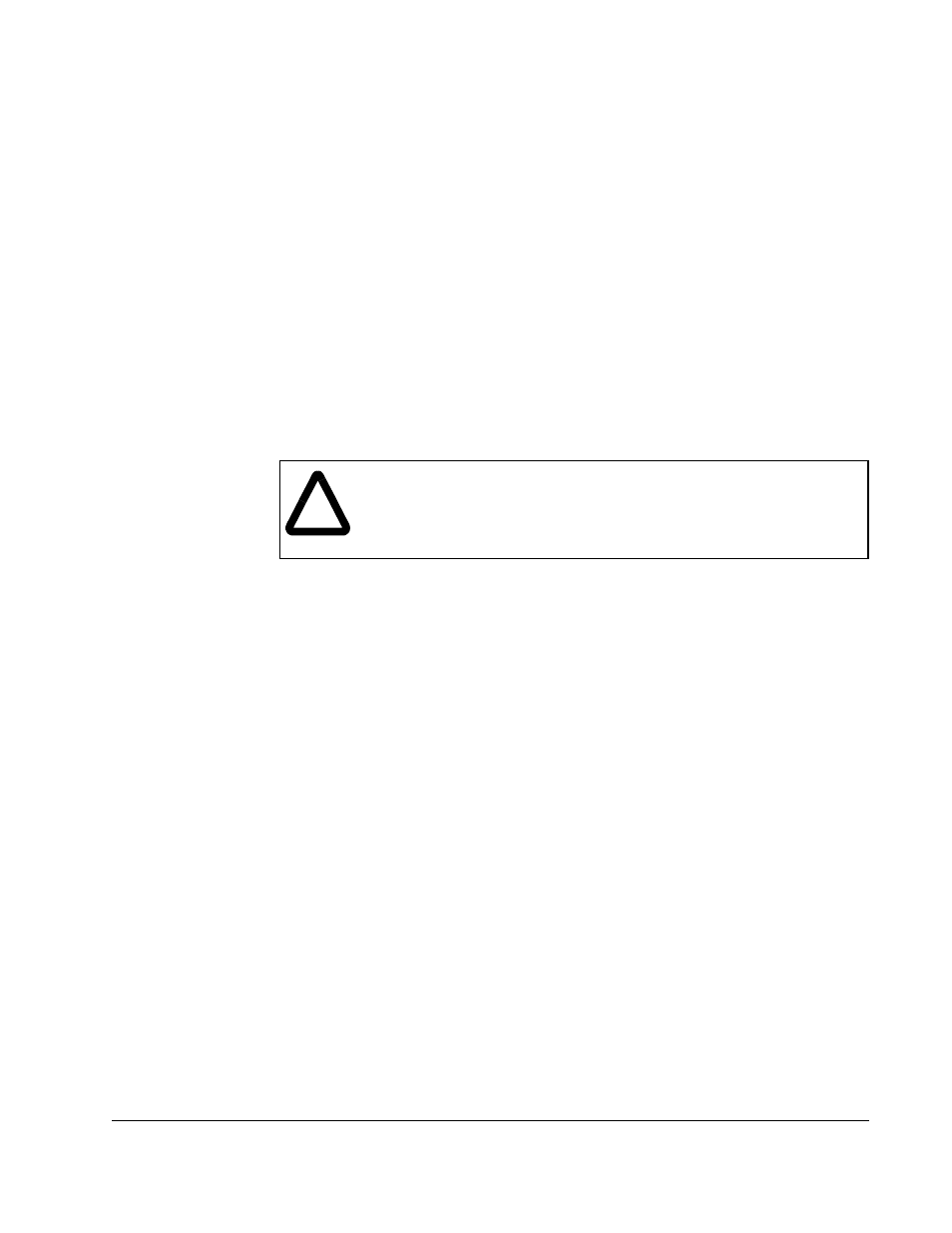
Installation Guidelines
4-13
The result of the resolver alignment test is written to the reserved tunable RES_ALN%
by the PMI. The value in the variable represents the offset. See the SA500 Drive
Configuration and Programming instruction manual (S-3044) for more information
about the RES_ALN% tunable variable.
The alignment test is commanded by the programmer by setting bit 1 in register
100/1100. When the test is successfully completed, the PMI will set the Alignment OK
bit (bit 1 in register 200/1200). The programmer can then turn off the enable bit in
register 100/1100. The Tuning Aborted bit (bit 5 in register 203/1203) will be set if the
range or travel during the test does not correspond properly to the number of motor
poles and resolver type configured for the drive.
Note that the resolver alignment procedure for brushless motors must be performed
whenever the resolver is disconnected from the motor for any reason.
4.6.1.3 Resolver Feedback Precautions
This section describes the resolver types and maximum motor speed supported by
the SA500 drive, as well as precautions against loss of resolver feedback.
Maximum Safe Operating Speed
The user must determine the maximum safe operating speed for the motor, connected
machinery, and material being processed. Then the user must either verify that the
system is incapable of reaching that speed, or ensure that the correct overspeed
parameter value has been entered during configuration.
Loss of Resolver Feedback
If resolver feedback is lost, brushless motors will remain relatively still and induction
motors will rotate close to their slip frequency. Because the PMI is receiving no speed
feedback, it will continue to provide current to the motor in an attempt to increase the
motor speed. This will raise the temperature of both the motor and the Power Module.
The Power Module overtemperature fault bit (bit 0 in register 202/1202) will be set if
the PMI detects that the motor current exceeds 100% of its continuous capacity for a
preset amount of time. At maximum rated current, this fault will be detected in 0.5
seconds, or less if the motor is stalled instead of rotating. (Note that the same fault bit
will be set if the PMI heatsink temperature exceeds a preset value.)
It is recommended that the programmer use the THERMAL OVERLOAD control block
in the UDC task to provide additional protection against overheating of the motor that
can result from loss of resolver feedback. This block can also protect against
overheating of the Power Module due to sudden increases in current. Refer to the
Control Block Language instruction manual (J-3676) for more information.
!
ATTENTION: The user is responsible for ensuring that the driven
machinery, all drive train mechanisms, and the material in the machine
are capable of safe operation at maximum speeds. Failure to observe
these precautions could result in damage to equipment and severe bodily
injury.