Install the replacement encoder – Rockwell Automation HPK-Series Motor Encoder Replacement Installation Instructions User Manual
Page 10
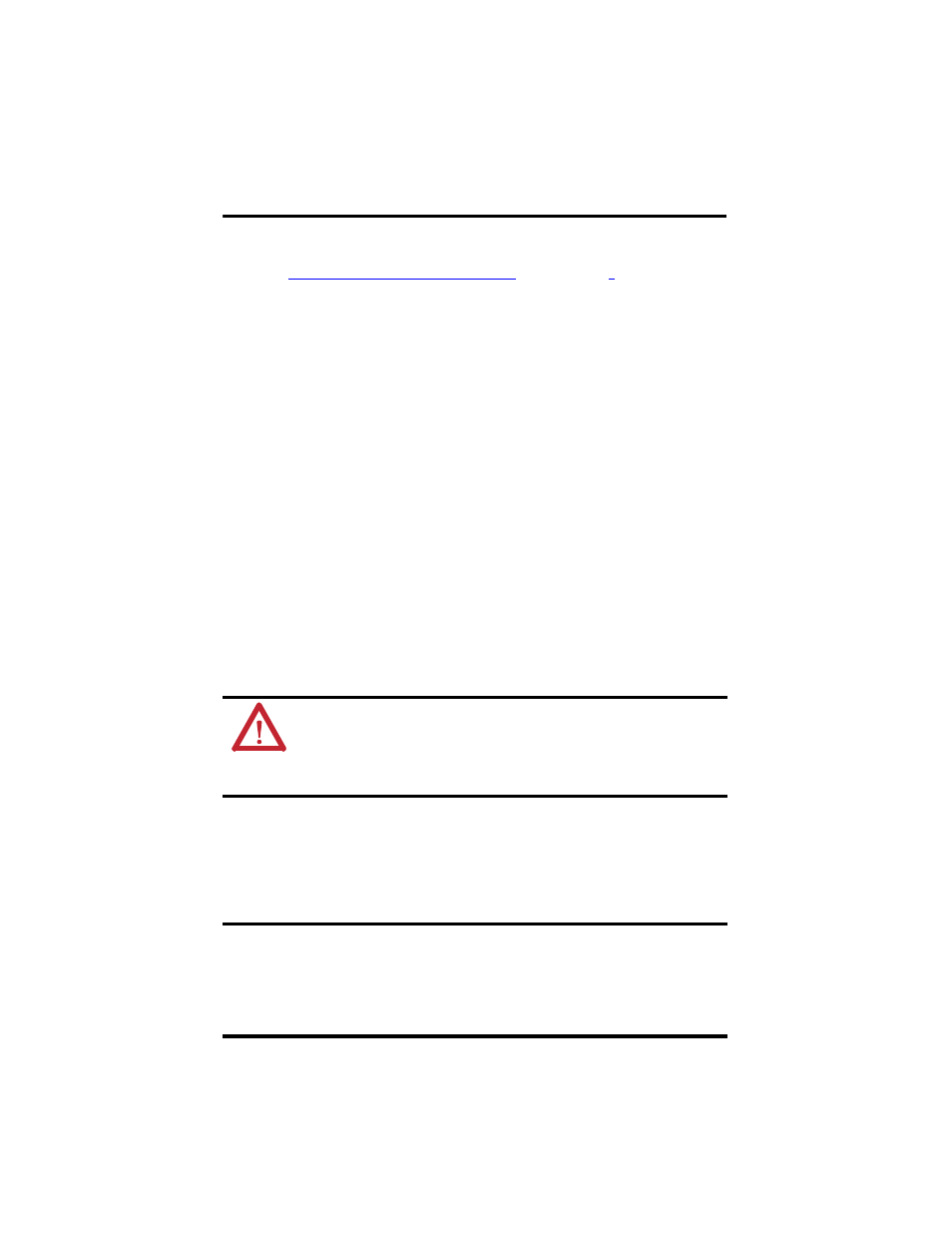
10 HPK-Series Motor Encoder Replacement Kit
Rockwell Automation Publication HPK-IN002C-EN-P - May 2012
Install the Replacement Encoder
Refer to the
HPK-Series Motor Encoder - Later Version
diagram on page
to identify specific
parts of the replacement encoder and their correct position when installed.
1. Verify the encoder replacement kit catalog number corresponds with the motor catalog
number listed on the motor nameplate.
2. Check the runout of the motor shaft, approximately 0.50 mm (0.02 in.) from the front
of the shaft.
If the runout exceeds 0.003 total indicator runout (TIR), correct it by tapping on the
motor shaft with a brass hammer.
3. Verify the plastic shaft sleeve (2) is installed in the encoder shaft (1), with the larger
diameter shoulder of the sleeve oriented at the same end of the encoder as the shaft
clamp screw (6).
4. Rotate the encoder shaft to an angular position that permits access to the shaft clamp
screw (6) when the encoder is installed.
5. Push the encoder (1) fully onto the motor shaft.
The encoder is fully seated when the plastic shaft sleeve (2) is tight against the motor
shaft shoulder, but the spring mounting plate is not bent.
6. Tighten the encoder shaft clamp screw (6) to 1.1 ± 0.1 N•m (9.7 ± 0.9 lb•in) with a
T10 Torx driver.
7. If a gap exists between the spring mounting plate and the motor frame when the encoder
is fully seated on the motor shaft, fill the gap by installing spacer washers (5) or stacked
flat washers.
8. Install screws (8) and washers (7) to hold the spring mounting plate (4) on the motor.
After all screws and washers are in place, tighten the screws to 0.28 N•m (2.5 lb•in).
TIP
Use a piece of soft wood or a thin rubber pad to protect the motor shaft from physical damage.
ATTENTION: The encoder shaft clamp can break if overtightened.
A broken shaft clamp could cause unexpected motor shaft rotation and corresponding machine
motion, due to loss of encoder feedback.
Failure to observe safety procedures could result in personal injury or damage to the motor and
other equipment.
IMPORTANT
Original version encoders use plastic washers to electrically isolate the encoder from the motor
frame at the spring mounting plate. Later version encoders have a plastic shaft sleeve, that
electrically isolates the encoder from the motor shaft.
When replacing an original version encoder with a later version encoder, do not use the plastic
washers to secure the spring mounting plate to the motor frame. Later version encoders use
metal screws (7) and washers (8) to ground the spring mounting plate to the motor frame.