Lead/lag control, Trusted, Process control algorithms t8019 – Rockwell Automation T8019 Trusted Process Control Algorithm Software Package User Manual
Page 16
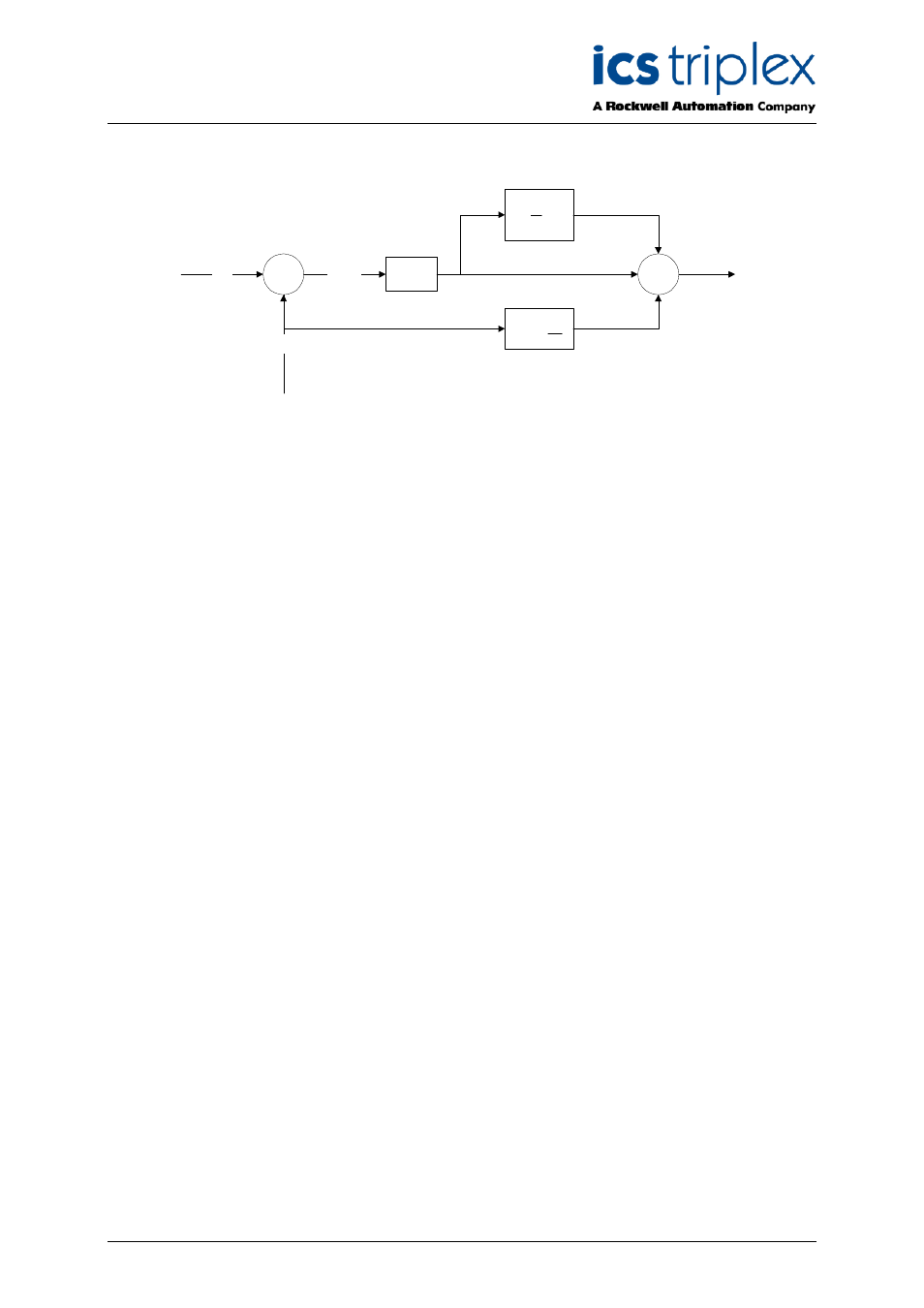
Trusted
TM
Process Control Algorithms T8019
Issue 8 Sep 07
PD-T8019
16
The figure 1 below gives a simplified overview of the PID function:
Figure 1 PID Function
At entry the error
S
is calculated as the difference between the set-point (SP) and the process variable
(PV). This error value is used in the calculation of the proportional and integral terms. The derivative
term is derived from PV as shown.
INC
STOP
prevents the output X
OUT
increasing when TRUE. When this input is TRUE and the PID is in
AUTO mode, the output is compared with the previous output and only values less than or equal to the
previous output will be returned and LIMIT
HI
will be set to TRUE. The integral term is also adjusted to
provide windup protection. Similarly, when DEC
STOP
is TRUE Xout will only return values greater than
or equal to the previous value, and LIMIT
LO
will be set to TRUE.
In manual mode (AUTO = False), the output (Xout) follows the input XO. The function provides
manual to automatic bumpless transfer by adjusting the integral term. If set-point tracking is required
then the MANTRK function should be used in conjunction with the PID_II function.
The PID function provides reset windup protection by allowing high and low limits (Xmax and Xmin) to
be specified and anti-reset windup on the integral term. If the PID output would have exceeded the
specified high or low limits, the corresponding limit output (LIMIT
HI
and LIMIT
LO
) is generated. Note
that the limit outputs are updated on each iteration of the PID function. The maximum and minimum
limits on Xout apply in both auto and manual modes.
In auto mode, the PID function will return only the proportional element on the first application scan,
and will the integral and derivative terms.
If Xmax < Xmin, the function assumes that the values have been reversed and “swaps” the values. On
each execution of the PID_II function with reversed parameters the ‘reversed’ error count will be
incremented. If an overflow condition occurs during the execution of the PID function the output Xout
will be set to Xmin in auto mode or XO in manual mode, and the integral term will be adjusted to
provide windup protection.
S
Kp
e
Error
SP
Integral
Derivative
Proportional
+
-
PV
dt
d
T
K
D
P
T
1
-
+
+
Xout