Front, Faults (continued), 1336 plus adjustable frequency ac drive w – Rockwell Automation 1336S ADJ FREQ AC DRIVE User Manual
Page 4
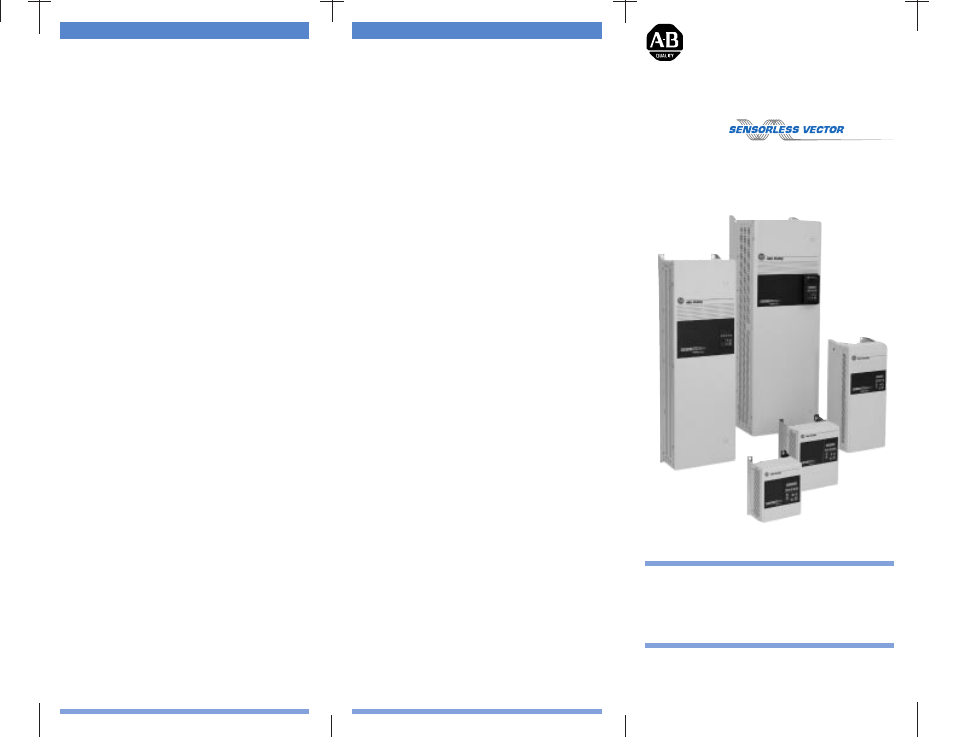
ATTENTION: This publication is designed as a reference
tool. The 1336 PLUS User Manual (publication 1336
PLUS-5.0) must be consulted for more detailed informa-
tion about parameters, faults and hazards of personal
injury.
1336 PLUS Adjustable
Frequency AC Drive w/
Reference Guide
Overload Fault
Excessive motor load exists. Reduce it
07
so output current does not exceed %
current set by the [Overload Current].
Overtemp Fault
Check for blocked or dirty heat sink
08
fins. Ambient temperature must not
exceed 40
°
C (104° F).
Overvolt Fault
Monitor AC line for high line voltage or
05
transient conditions. Can also be
caused by motor regeneration. Extend
decel time or install dynamic brake.
Phase U, V, W Fault
Check wiring between drive and motor.
38, 39, 40
Check motor for grounded phase.
P Jump Err Flt
Reserved for future use.
37
Poles Calc Flt
Calculated value of [Motor Poles] must
50
be between 2 and 32. Check program-
ming of [Motor NP RPM] & [Motor NP
Hertz].
Power Loss Fault
Monitor the incoming AC line for low
03
voltage or line power interruption.
Power Mode Fault
Check all connections to the Control
26
Board/Language Module.
Power Overload
2
Drive rating of 150% for 1 minute has
26
been exceeded. Reduce load.
Power Test Flt
Internal power mode variable received
46
incorrect value. Check Power/Driver Bd.
Precharge Fault
Check the precharge circuit.
19
Precharge Open
Check the precharge circuit.
56
Reprogram Fault
Occurs after drive has been reset to
48
factory default values. Clear fault or
cycle drive power. Reprogram.
ROM or RAM Flt
Internal ROM/RAM tests failed. Check
68
Language Module.
Run Boost Fault
[Run Boost] set greater than [Start
34
Boost]. Verify correct programming.
Serial Fault
Check for break in communications
10
line.
Shear Pin Fault
2
Programmed [Current Limit] exceeded
63
& [Shear Pin Fault] enabled. Check load
requirements & {Current Limit] setting.
Temp Sense Open
Heat sink thermistor open or malfunc-
55
tioning. Check thermistor/connections.
Undervolt Fault
Monitor the incoming AC line for low
04
voltage or line power interruption.
UV/UW/VW Short Fault Check motor and external wiring to
41, 42, 43
drive output terminals for a short.
Xsistr Desat Flt
One or more output transistors were
47
(Frame C & up only)
operating in active region, instead of
saturation. Check for damaged transis-
tors.
Drive Fault Reset
Power-up attempted with open Stop
22
contact or closed Start contact.
EE Init Read
Trouble reading EEPROM during
53
initialization. Check Power/Driver Bd.
EE Init Value
Stored parameter value out of range on
54
initialization. Check Power/Driver Bd.
EEprom Checksum
EEPROM checksum does not match.
66
Check connections to Power/Driver Bd.
EEprom Fault
EEPROM will not write a new value.
32
Check connections to Control Board.
FGND 10ms Over
Occurs if 10ms interrupt is pending
52
before current interrupt is complete.
Ground Fault
Check motor and external wiring to
13
drive output for a grounded condition.
Ground Warning
If enabled, indicates lower ground current
57
level than Ground Fault (see above).
Hertz Err Fault
No valid operating frequency. • Check
29
[Minimum/Maximum Freq] parameters
• Check [Skip Freq 1, 2, 3, Band] •
Check for loose connections or trans-
ducer loss at 4-20mA input, TB2.
Hertz Sel Fault
Reprogram [Freq Select 1] and/or
30
[Freq Select 2] with a correct value.
Loop Overrn Flt
Overrun of the 2.5ms control loop.
23
Check connections to the Driver Board.
Max Retries Fault
Check buffer for fault requiring reset.
33
Correct cause & clear by pressing local
Stop key or cycling TB3 Stop input.
Motor Mode Flt
Fault detected on Control Board. Check
24
connections to board/Language Module.
Motor Stall Fault
If motor is drawing excessive current
06
(over 150%), motor load is excessive
and will not allow the drive to acceler-
ate to set speed. A longer accel time or
a reduced load may be required.
Neg Slope Fault
Check programming. • [Maximum
35
Voltage] must be greater than [Base
Voltage]
1
• [Maximum Freq] must be
greater than [Base Frequency]
1
• [Base
Voltage] must be greater than [Start
Boost] • If [DC Boost Select] = “Full
Custom”, [Base Voltage] must be greater
than [Break Voltage] and [Break Voltage]
must be greater than [Start Boost].
Open Pot Fault
Check external pot. circuit at TB2 for an
09
open circuit.
Op Error Fault
• A SCANport™ device requests a read/
11
write of a data type not supported. •
[Motor Type] set to “Sync PM” & [Stop
Mode Used] set to “DC Brake” • [Motor
Type] set to “Sync Reluc” or “Sync PM”
& [Speed Control] set to “Slip Comp”.
Overcurrent Flt
Check for short circuit at drive output
12
or excessive load conditions at motor.
Publication 1336 PLUS-5.1 – May, 1997
Supersedes December, 1996
P/N 74001-004-01(K)
1
Firmware versions before 2.01 only.
2
Firmware versions 4.01 & up only.