Tune the pi loop, Tune the pi loop -18 – Rockwell Automation 160 SSC Series C FRN 7.xx User Manual
Page 56
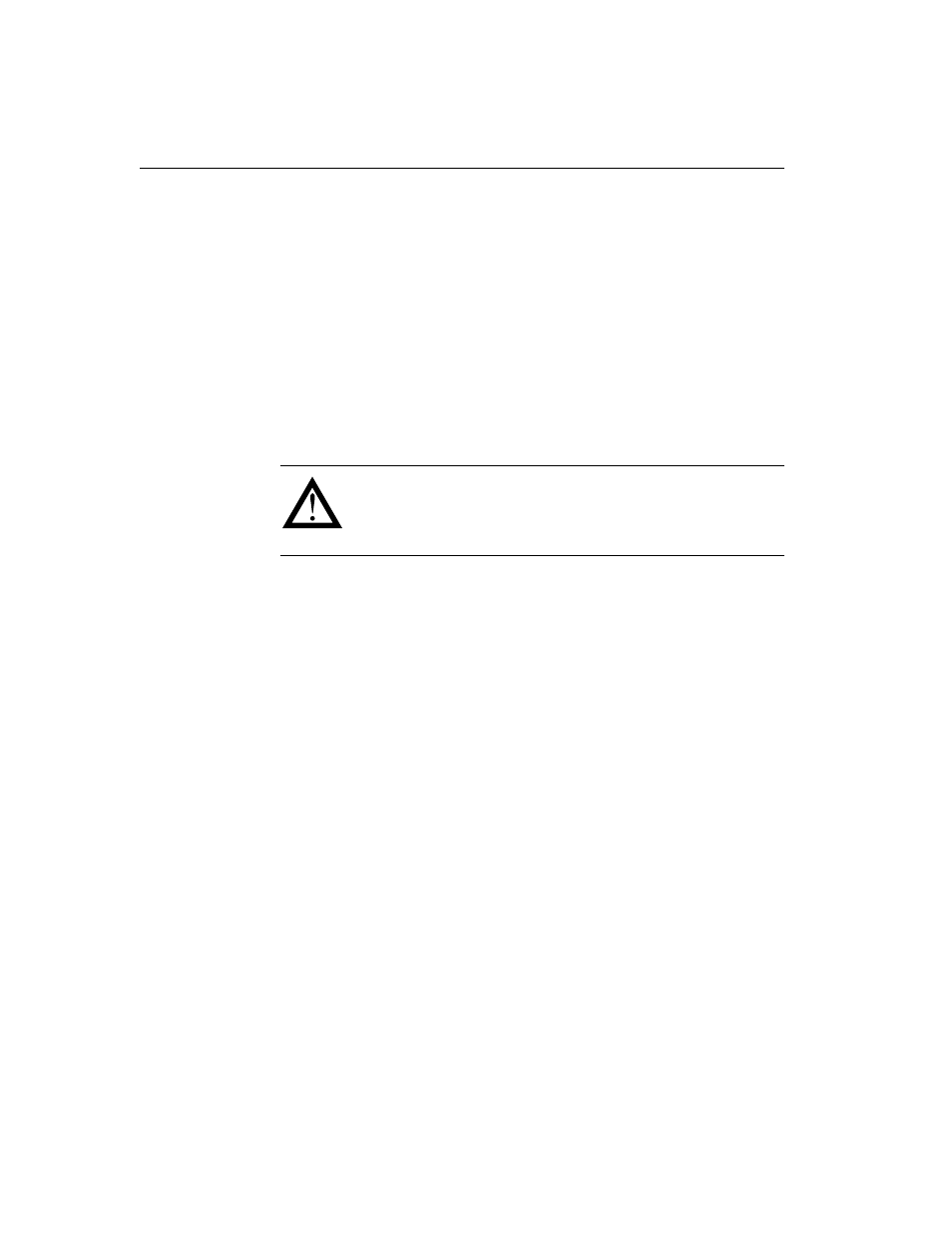
5-18
Parameters and Programming
5. Use P75 - [Analog Input Minimum] and P76 - [Analog Input Maximum] to scale
feedback to the process operating range. This may also be used to invert the
feedback so that increasing feedback signal produces decreasing output
frequency.
6. Set P83 - [PI Process Reference] to 20 as an initial setting.
This establishes the set point as 20% of the maximum analog input.
(This setting must be greater than zero to activate PI control in Firmware
Version FRN 7.06 except when using input mode 9.)
7. Connect TB3-8 with TB3-7. This will disable PI control and force the output
frequency to the P58 - [Internal Frequency] setting.
8. Connect TB3-6 with TB3-7 to start the drive. Verify motor operation and
direction.
9. Remove the connection between TB3-8 from TB3-7. This will place the drive
into PI control mode when using input modes 7 and 9.
Tune the PI Loop
Parameters P81 - [PI Proportional Gain] and P82 - [PI Integral Gain] are used to set how
the drive will respond to errors (fluctuations) in feedback.
• P81 - [PI Proportional Gain] corrects output frequency based on the magnitude of
the error.
• P82 - [PI Integral Gain] corrects output frequency based on the length of time an
error has been present.
1. Set P82 - [PI Integral Gain] to zero and P81 - [PI Proportional Gain] to some low
value.
2. Apply a step function command via P83 - [PI Process Reference] and monitor
the output response.
3. Increase P81 - [PI Proportional Gain] until the response of the output is
acceptably fast or the output becomes too noisy.
4. Reduce P81 - [PI Proportional Gain] back to the highest value at which the
response is still clean.
5. Set P82 - [PI Integral Gain] to a low value.
6. Apply a step function command and monitor the output response.
7. Increase P82 - [PI Integral Gain] until the response is acceptably fast without
overshoot.
Important:
If either the value of P81 or P82 is set too high, drive output will
oscillate around the set point entered in P83 - [PI Process Reference]
due to continually changing loads in the application. Use P84 -
[Dead Band] to limit the effects of this oscillation by blocking a
frequency count to either side of the set point frequency.
ATTENTION: Hazard of personal injury or equipment damage exists
due to unpredictable changes in motor speed. Do not use P72 - [Slip
Compensation] and P83 - [Process Reference] to disable PI control while
the drive is running. Disable PI control only when the drive is stopped.