Rockwell Automation 284G ArmorStart - Getting Started User Manual
Page 9
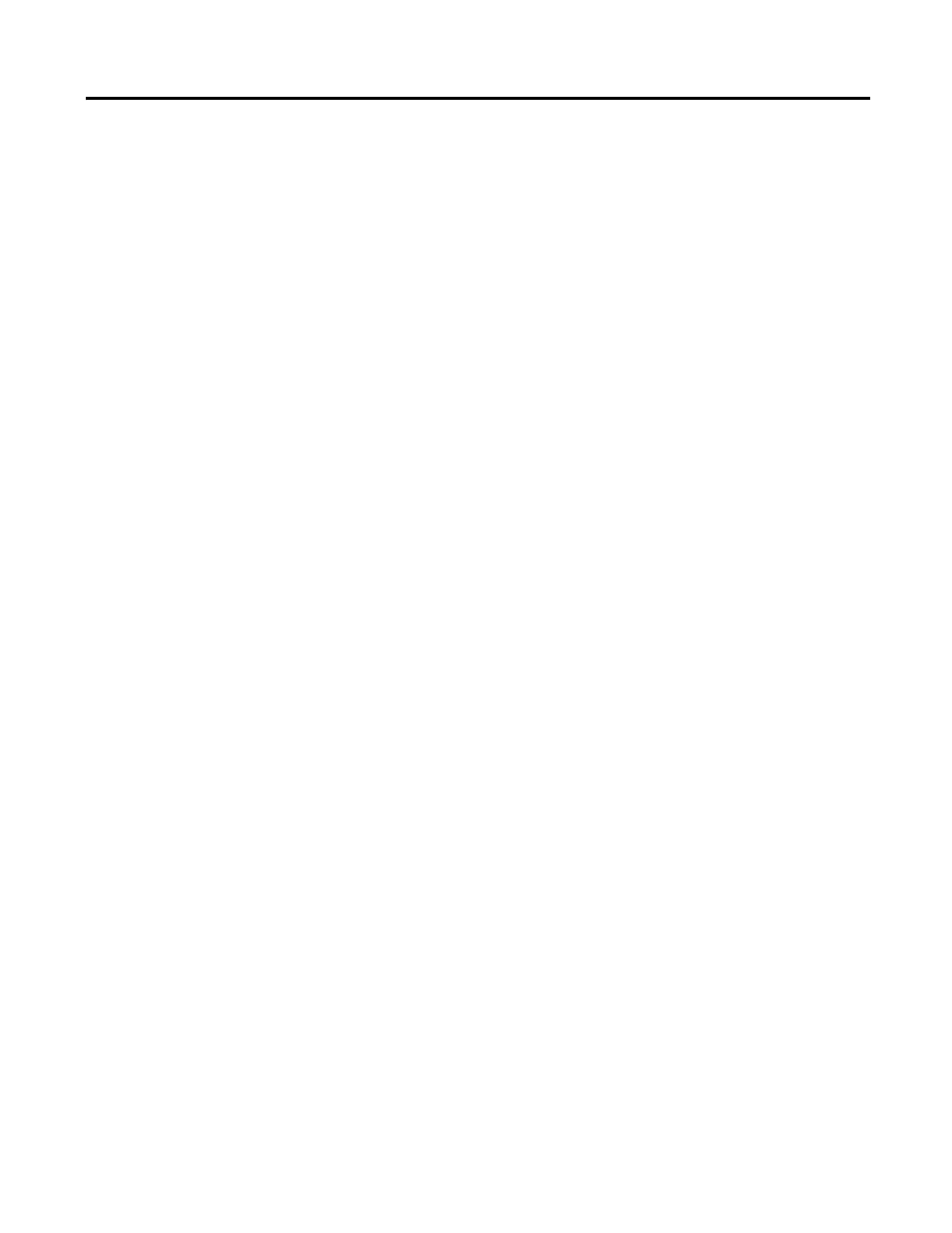
Publication 284G-QS001A-EN-P - December 2008
9
*Historically cable meeting these crush and impact requirements were
designated and marked “Open Wiring”. Cable so marked is equivalent to the
present Type TC-ER and can be used.
While the ArmorStart is intended for installation in factory floor
environments of industrial establishments, the following must be taken into
consideration when locating the ArmorStart in the application: Cables,
including those for control voltage including 24V DC and communications,
are not to be exposed to an operator or building traffic on a continuous
basis. Location of the ArmorStart to minimize exposure to continual traffic
is recommended. If location to minimize traffic flow is unavoidable, other
barriers to minimize inadvertent exposure to the cabling should be
considered. Routing cables should be done in such a manner to minimize
inadvertent exposure and/or damage.
Additionally, if conduit or other raceways are not used, it is recommended
that strain relief fittings be utilized when installing the cables for the control
and power wiring through the conduit openings.
The working space around the ArmorStart may be minimized as the
ArmorStart does not require examination, adjustment, servicing or
maintenance while energized. In lieu of this service, the ArmorStart is
meant to be unplugged and replaced after proper lockout/tag-out procedures
have been employed.
DeviceNet Network Installation
The ArmorStart Distributed Motor Controller contains the equivalent of
30 in. (0.76 m) of Device Net drop cable's electrical characteristics and
therefore 30 in. of drop cable must be included in the DeviceNet drop cable
budget for each ArmorStart in addition to actual drop cable required for the
installation.
Other DeviceNet System Design Considerations
The separation of the control power and DeviceNet power is recommended
as a good design practice. This minimizes the load on the DeviceNet supply,
and prevents transients which may be present on the control power system
from influencing the communication controls.
Electromagnetic
Compatibility
(EMC)
The following guidelines are provided for EMC installation compliance.
General Notes
•
The motor Cable should be kept as short as possible in order to avoid
electromagnetic emission as well as capacitive currents
•
Conformity of the drive with CE EMC requirements does not guarantee
an entire machine installation complies with CE EMC requirements.
Many factors can influence total machine/installation compliance.