Installation of adjacently mounted units, Alignment – Rockwell Automation 42DR Intrinsically Safe Sensor User Manual
Page 4
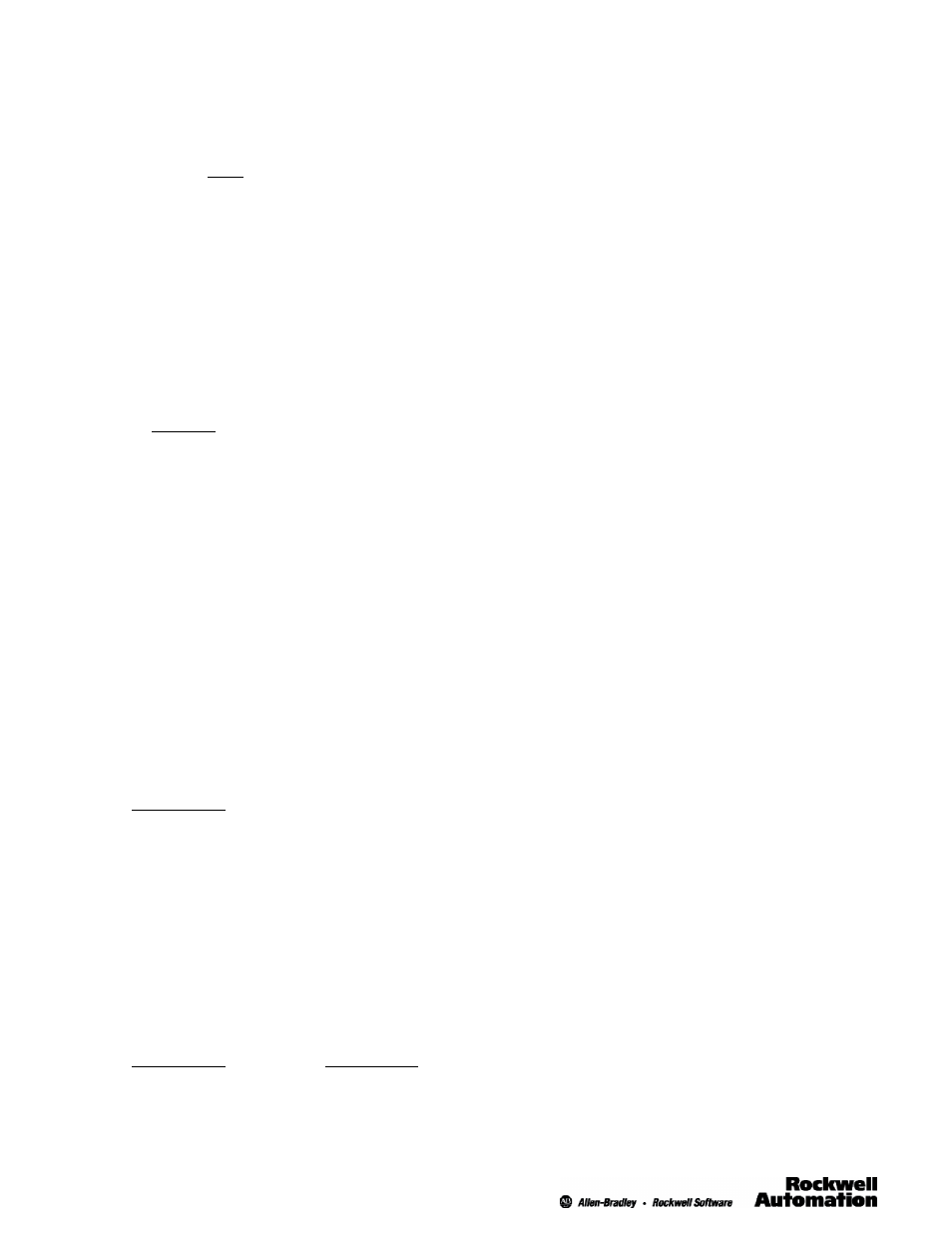
4
Power Supply Barrier
Intrinsic safety zener diode barrier #897H--S120 is recommended for FM
Approved and UL Listed locations. See page 8 for barrier details.
Alternatively, the user must select his own power supply barrier. It should be
noted that the Series 5500 control must have at least 13V DC at the + and --
terminals of the power base, Type 42DTB Model 5500. The supply current at
13V DC is 26mA. The maximum barrier resistance is then determined by the
following formula:
Vs -- 13
0.026
Rb max =
where:
Rb max = Maximum Barrier Resistance
Vs
= Voltage Supply
13
= Minimum Voltage Supply to Control
0.026
= Supply Current (26mA max. at 13V DC)
Load Supply Barrier
Intrinsic Safety Zener Diode Barrier #897H--S120 is recommended for FM
Approved and UL Listed locations. See page 8 for barrier details.
Alternatively, the user may select his own load supply barrier. When using the
NPN (current sink) open collector output of the Series 5500 Intrinsically Safe
controls, a load supply barrier must be selected in addition to the power supply
barrier. The maximum load supply barrier resistance can be determined by
using the following the formula. The user must provide values for the load
voltage drop, V
load
, and the load current, I
load
(20mA
max):
Vs -- V
load
-- 3.4
I
load
Rb max =
where:
Rb max = Maximum Barrier Resistance
Vs
= Voltage Supply
V1
= Load Voltage Drop
3.4
= Output Cir. Voltage Drop (3.4V)
I
load
= Load Current (20mA max.)
Note: The NPN and output configuration is not approved for
use in hazardous locations classified as Class I, Division 1,
Groups A or B.
Signal Return Barrier for Source (PNP) Output Only
Intrinsic Safety Zener Diode Barrier #897H--S140 is recommended for FM
Approved and UL Listed locations. See page 8 for barrier details.
Alternatively, the user may select his own signal return barrier when the PNP
(current source) open collector output of the Series 5500 Intrinsically Safe
controls. For PNP output applications in hazardous locations not classified as
Class I, Division 1, Groups A and B, signal barrier must be selected in addition
to the power supply barrier and the load supply barrier. For reference, see
Control Drawing for the three barrier PNP output configurations. The sum of the
maximum signal return barrier resistance and the maximum load supply barrier
resistance can be determined using the following the formula. The user must
provide values for the load voltage drop, V
load
, and the load current, I
load
(20mA
max):
Vs -- (V
load
+ V
brs
+ 0.4)
I
load
Rbls + Rbrs =
where:
Rbls
= Load Supply Barrier Resistance
Rbrs
= Signal Return Barrier Resistance
Vs
= Voltage Supply
V
load
= Load Voltage Drop
V
brs
= Signal Return Barrier Voltage Drop
0.4
= Output Switch Voltage Drop (0.4V)
I
load
= Load Current (20mA max.)
For PNP output applications in hazardous locations classified as Class I,
Division 1, Groups A and B, signal return barrier must be selected in addition to
the power supply barrier. For reference, see Control Drawing for the two barrier
PNP output configurations. The signal return barrier resistance and the power
supply barrier resistance must satisfy the following two formulas. The user must
provide values for the load voltage drop, V
load
, and the load current, I
load
.
Please note that I
load
is 10mA max in this configuration.
Vs -- 13
I
load
+ 0.026
Rbps =
Vs -- (o.4 + V
brs
+ V
load
)
I
load
+ 0.026
Rbps + Rbrs =
where:
Rbps
= Max. Power Supply Barrier Resistance
Rbrs
= Max. Signal Return Barrier Resistance
Vs
= Voltage Supply
V
load
= Load Voltage Drop
13
= Min. Voltage Supply to Control (13V)
0.026
= Supply Current (26mA max. at 13V)
I
load
= Load Current (10mA max.)
V
brs
= Signal Return Barrier Voltage Drop
0.4
= Output Switch Voltage Drop (0.4V)
Installation of Adjacently Mounted Units
Type 42DR Series 5500 Photoheads are supplied to operate at one of two
different frequency ranges, permitting Photoheads to be mounted close to each
other without generating interfering signals.
Units in open frequency range are marked with a dot (S). Units in the other
frequency range have no dot.
Accordingly, when two Type 42DR Series 5500 controls are mounted close
together and/or face each other, select Photoheads so that one is marked with a
dot (S) and the other has no dot.
Alignment
Alignment of the Type 42DR LED control can be accomplished by visually
sighting the control at the reflector using reflex operation or at the object using
proximity until the visible LED indicator on the top lights with switch in the “LT”
position or goes out when the switch is in “DK” position.
To insure that the beam is centered on the reflector, in Reflex or on the object
using proximity, sweep the beam across the reflector or object in the horizontal
plane and determine at what points the indicator light goes on and then goes off.
Set the beam half way between both points. Do the same in the vertical plane.