Pump off setup, Initializing the pump stroke position – Rockwell Automation 20B PowerFlex 700 Custom Firmware - Pump Off User Manual
Page 3
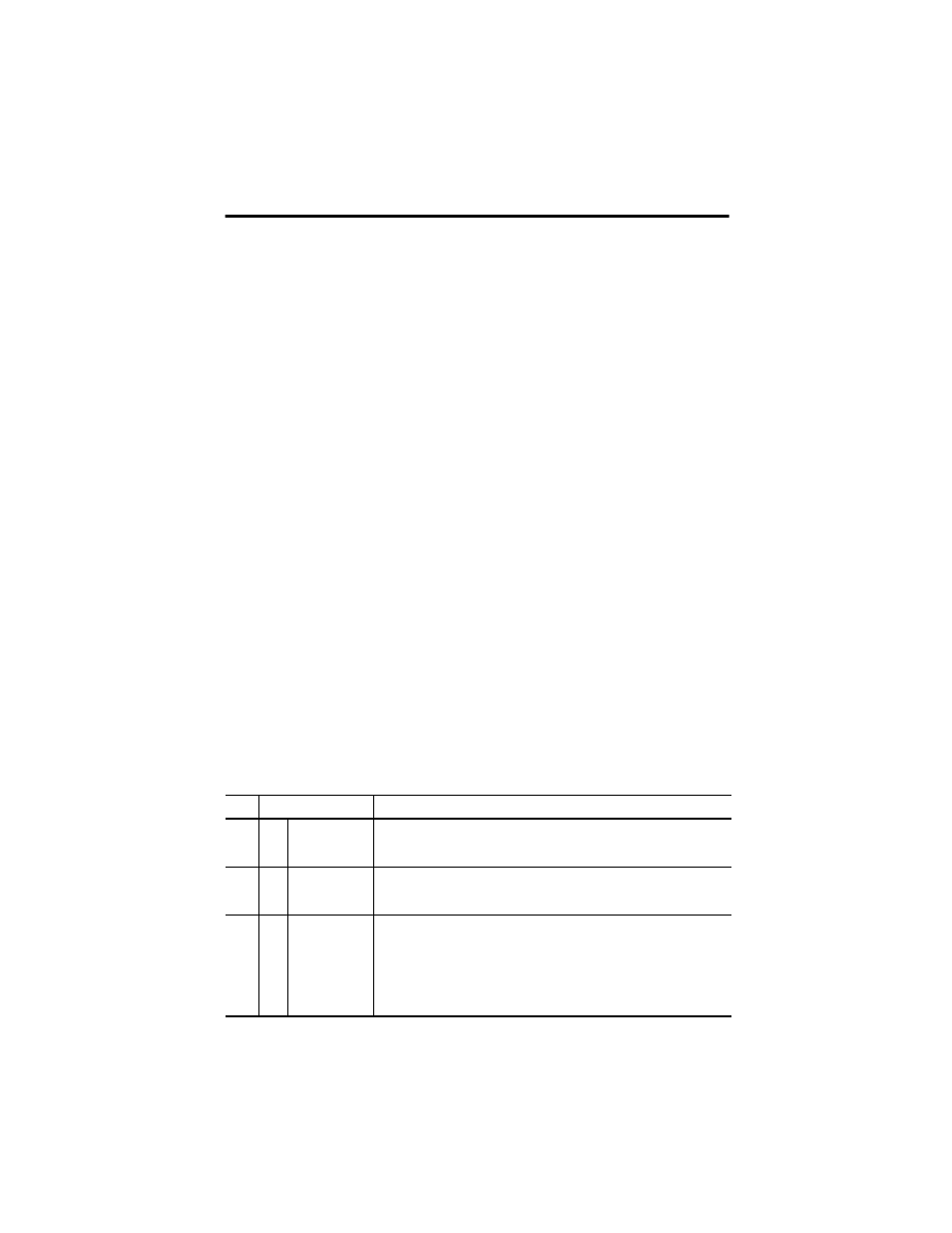
PowerFlex 700 with Vector Control Option Custom Firmware 3
Rockwell Automation Publication 20B-IN020C-EN-P - January 2014
Pump Off Setup
Follow these steps to set up the pump off function.
1. Set parameter 53 [Motor Cntl Sel] to 4, “FVC Vector.”
2. Set parameter 641 [OilWell Pump Sel] to 1, “Pump Jack.”
3. Set the following parameters according to your equipment. These settings are used to
calculate the torque limits based on the gearbox size:
•
Parameter 642[Gearbox Rating]
•
Parameter 643 [Gearbox Sheave]
•
Parameter 644 [Gearbox Ratio]
•
Parameter 645 [Motor Sheave]
4. Uncouple the motor and the load.
5. Run Autotune by setting parameter 61 [Autotune] to 2, “Rotate Tune.”
6. Raise parameter 83 [Overspeed Limit] to 20 Hz.
7. Set bit 6, Decel Inhibit, of parameter 238 [Fault Config 1]to disabled (0).
8. Adjust parameter 153 [Regen Power Lim] to limit the amount the system regenerates to
the DC bus.
Initializing the Pump Stroke Position
Follow these steps to initialize the pump stroke position.
TIP
If a DB resistor is not used, we recommend an initial setting of -5%.
Pump Stroke Position Initialization Steps
Step
Parameter
Description
1
680
[Pump Cycle Store]
Set with the drive operating at normal speed. The drive then calculates the peaks and
valleys of the torque signal. This is used to determine the downstroke the next time the
drive is started.
2
681
[Set Top of Strok]
Enable. Press Enter when the rod is at the top of the stroke. The parameter value changes
back to “Disabled” and the top of stroke position is stored in testpoint 688. Top of stroke
occurs when the horse head is at its highest point.
3
689
[Pump Off Setup]
Bit 1, Pos Filter – Sets the level of filtering on torque for position calculation.
• 0 = light (default)
• 1 = heavy (the effect on the filter can be seen at testpoint 680).
Bit 2, Pos Offset – Adjusts correction factor for motor slip in position calculator.
• 0 = 400 (default)
• 1 = 50 (to see the effect of this check the timing between the position and torque,
testpoint 635 and 636)