USG Drying Plaster Casts User Manual
Page 3
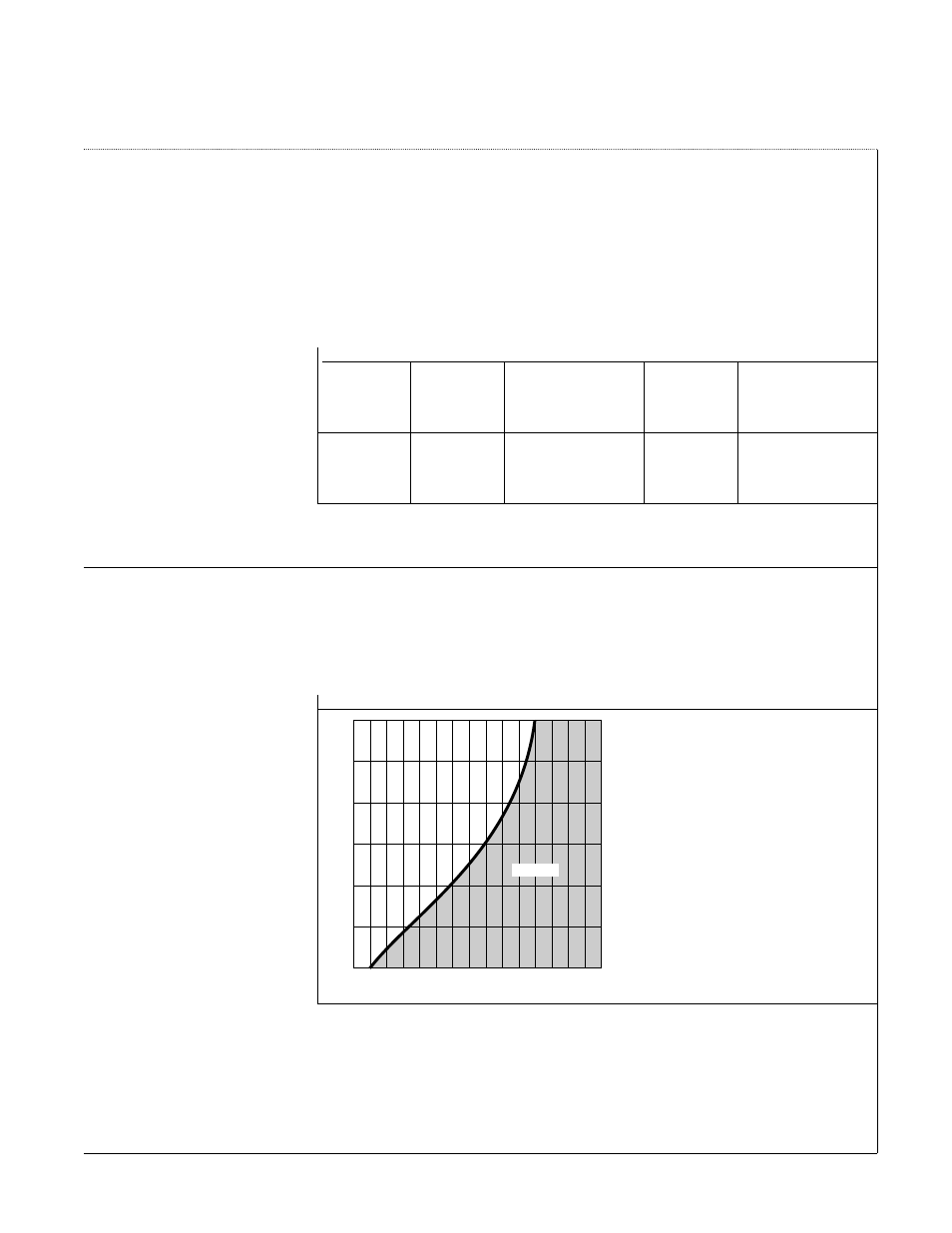
Designing the Dryer
In using the chart shown here, assume that maximum amount of plaster used per day will be 20 to 100 bags; then
design the drying room so that it is adequate for this volume. The chart will indicate how much air must pass
through the heater to supply the required heat energy while keeping the temperature of entering air at a safe level.
The column “Minimum Exhausted Air (B)” indicates how much moist air must be expelled to dry casts in one
day. More moist air can be exhausted if desired, but less than recommended would increase drying time. The vol-
ume of air exhausted must be replaced by fresh air introduced elsewhere in the system. Probably the best point to
bleed fresh, cool air into the recirculation system is just prior to the heater. Since total volume of air through the
heater (recirculated air plus fresh makeup air) is large, it needs to be heated only a few degrees to supply the nec-
essary energy to dry the plaster casts effectively. Even with this procedure, additional fans within the dryer will be
required for adequate air velocity of 15 fps.
Plaster Dryer Design Data (assumes 16-hr. cycle for Art & Moulding Plasters)
(A)
(B)
(C)
(D)
Minimum Exhausted
Recirculation
Total Air
Air & Makeup Air
(2)
of Humid Air
(3)
(Makeup plus recirculated)
Plaster Use
Burner Capacity
(1)
Standard
Standard
Through Heater
(3)
tons/day
Btu/hr.
cu. ft./min.
cu. ft./min.
Standard cu. ft./min.
5
600,000
1,800
22,000
23,800
4
480,000
1,450
17,600
19,050
3
360,000
1,100
13,200
14,300
2
250,000
800
8,800
9,600
1
125,000
400
4,400
4,800
(1) Based on a direct-fired heater. If an indirect-fired furnace is used, the stated figure must be bonnet or plenum capacity (usually 80% of the
burner capacity).
(2) Exhaust and dryer interior assumed at 120 °F.
(3) Recirculated and makeup air assumed to enter drying chamber at max. 150 °F.
Faster Drying
By using a humidity control as well as temperature control, drying ratio can be increased. Fig. 3 shows a curve
relating relative humidity (R.H.) and air temperature. As long as these two measurements give a point to the right
of this curve, drying will proceed without excessive burning of the plaster cast. The closer the control can be main-
tained to the line, the more rapid the rate of drying.
For example, 140 °F with 40% R.H. will result in faster drying than 140 °F with 50% R.H. If R.H. is 50%, tem-
perature should be increased to 150 °F.
Fig. 3—Minimum relative humidity at temperature to prevent calcination of gypsum casts.
130
0
percent relative humidity
air temperature
–
˚
F
50
140
150
160
10
20
30
40
60
70
SAFE ZONE