USG Drying Plaster Casts User Manual
Page 2
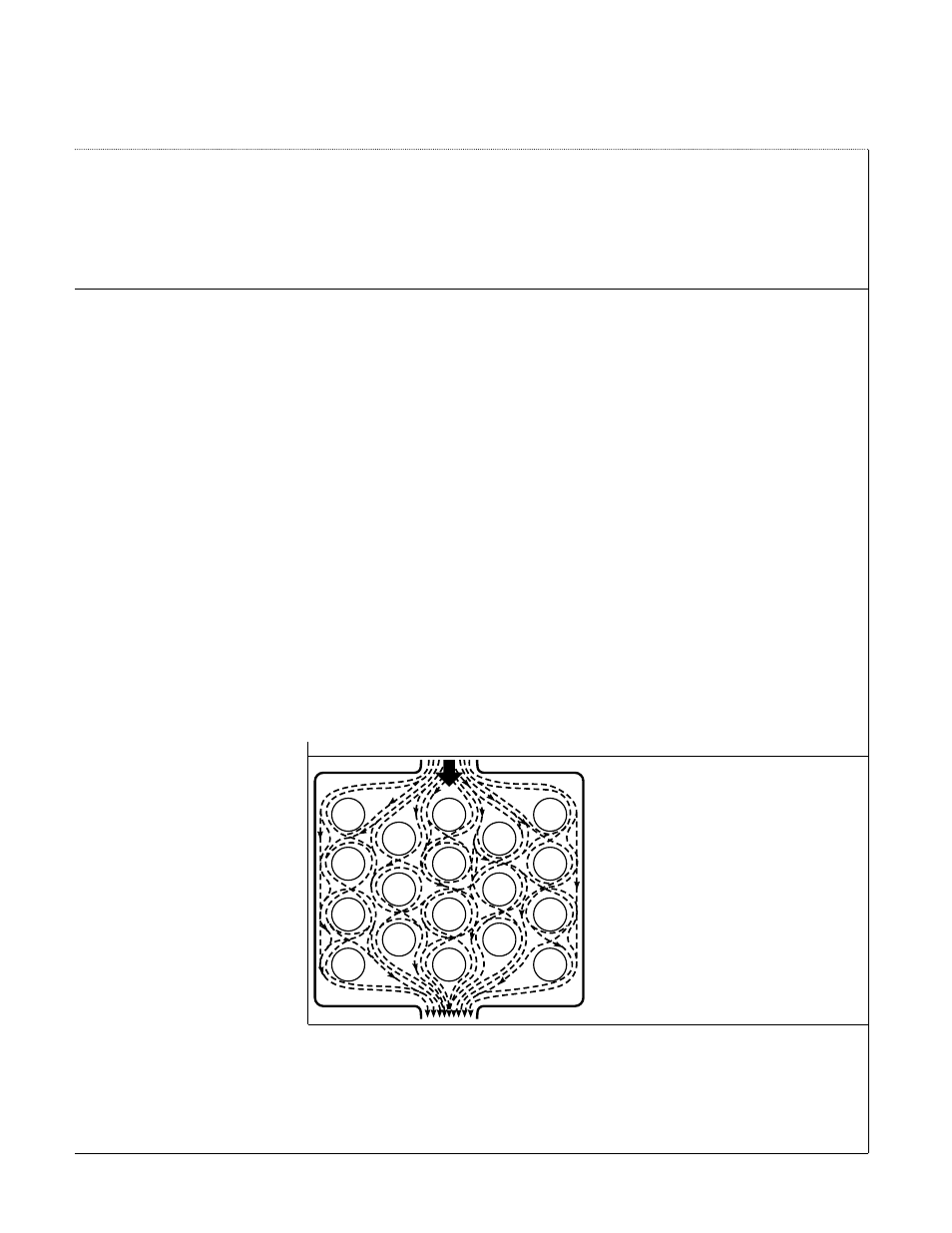
What is Best Dryer Temperature?
The main physical limitation in drying a plaster cast is the maximum temperature at which the dryer can operate
and not calcine the cast. Recommended temperatures are 110 to 120 °F for USG
®
White Art Plaster, No. 1 Casting
Plaster, Moulding Plaster, Pottery Plaster, H
YDROCAL
®
Brand White and H
YDRO
-S
TONE
®
Gypsum Cements; from 125
to 130 °F for Industrial Plaster PC. Operating much above these temperatures will result in surface calcination;
that is, surfaces of the casts, especially those in front of hot-air ducts, will become soft and powdery.
In the chart on the next page air volumes through the heater were calculated so that hot air entering would be
about 30 °F higher than the temperature in the dryer. This gives an adequate safety margin.
Air Circulation Within the Dryer
Drying studies of various materials show that increasing air speed over plaster casts reduces drying time. An air
speed of 15 fps (ft. per sec.) is recommended, and speeds up to about 30 fps are desirable. At speeds over 30 fps,
cost of moving the air can be greater than the value of time saved.
Here is an example of a drying problem in a 3,200-cu. ft. dryer. It was loaded daily with about 4.2 tons of casts
containing some 1.2 tons of water to be evaporated. Although the furnace supplied enough heat to evaporate the
water, and exhaust air volume was adequate to carry out the water vapor, casts were not drying. The solution was
to improve circulation in the drying chamber to 15 fps by adding four 20-in.-dia. supplementary fans. This pro-
vided a temperature differential of 2 or 3 °F throughout the dryer, indicating a uniformity of air flow.
Air must flow around each cast. (See figure 2.) If the casts are crowded together, they dry very slowly. They
should be placed on racks or separated by runners so that water vapor is able to escape.
Following is a summary of important points in designing and using equipment:
1. Is the burner large enough to supply necessary heat energy? (Use chart on next page for size.)
2. Is sufficient humid air being exhausted from the dryer’s system?
3. Is the outlet of the exhaust duct well away from the fresh air intake?
4. Is hot air entering the dryer chamber at 150 °F or below? That is the maximum for USG White Art, USG No. 1
Casting, USG Moulding, USG Pottery Plasters, H
YDROCAL
Brand White or H
YDRO
-S
TONE
Gypsum cements. Use 160
°F or below for Industrial Plaster PC.
5. Is air circulation within the dryer fast enough? Are fans within the dryer designed to operate at dryer’s tempera-
ture?
6. Are applicable building and safety codes being met?
7. Can the flame or heating element be seen from inside the drying chamber? They should not be visible.
8. Has production increased since the dryer was designed? If so, larger equipment may be needed.
9. Are spaces between the plaster casts great enough to allow adequate air circulation? (Approx. 1/2 in. on small
casts; 2 in. on casts of 100 lbs. or more.) Consider contacting a heating and ventilating engineer to check sys-
tem for proper air flow and temperature.
Fig. 2—Air-flow pattern for proper circulation in drying chamber.