USG DIAMOND Veneer Basecoat Plaster User Manual
Page 2
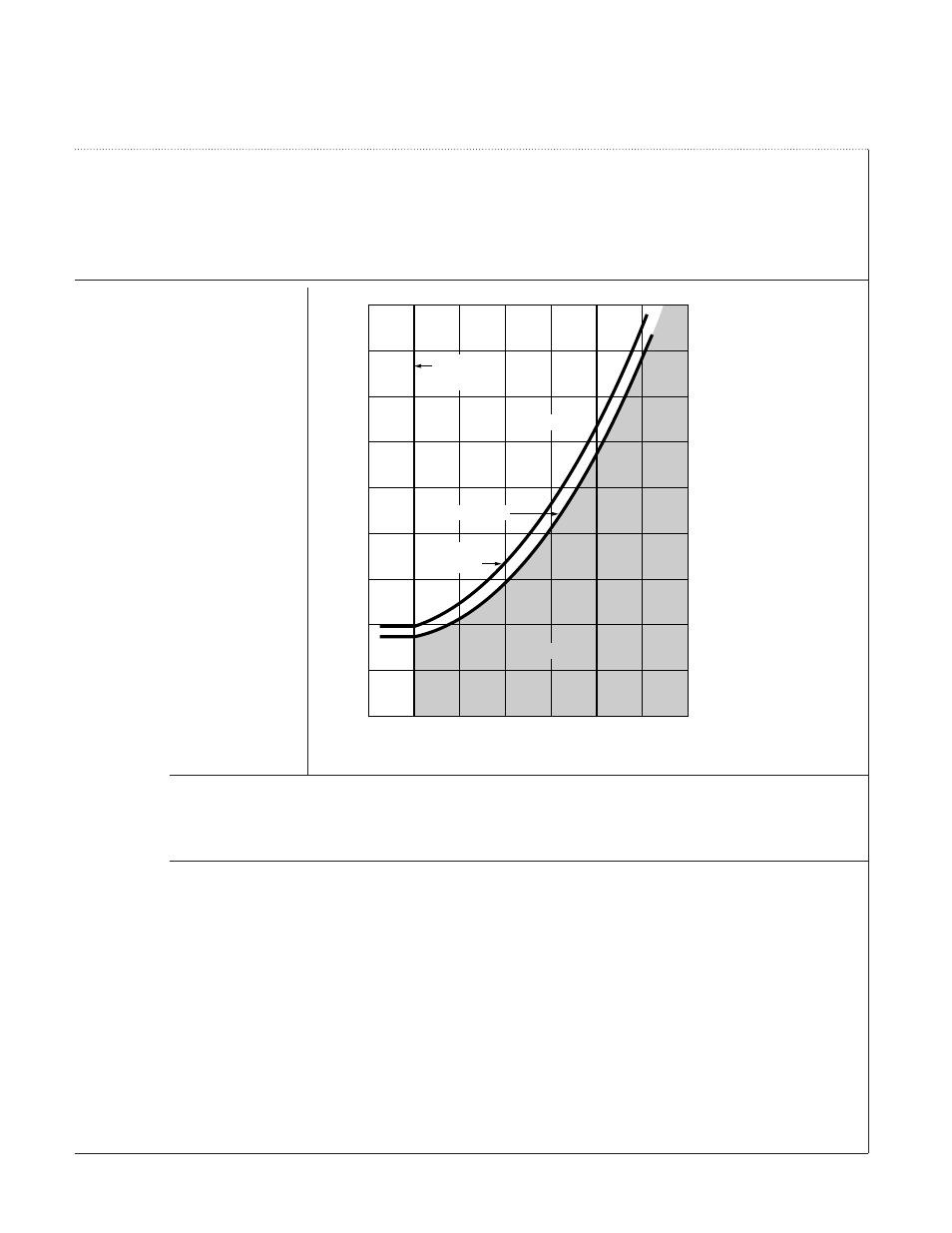
Application
(continued)
Mixing
Use a cage-type mixing paddle driven by a heavy duty electric drill producing a minimum speed of 900-1000 rpm
(no load). Place approximately 12 to 14 quarts (11 to 13 L) of clean water in a 12 to 15 gal. (45 to 57 L) smooth-
sided container, and with the mixer operating, slowly add one bag of plaster. Mix for a minimum of three minutes,
but no longer than five minutes, to disperse all lumps completely. Mixing equipment and all tools must be kept clean.
Plastering
Gypsum Base
Apply D
IAMOND
Brand Veneer Basecoat Plaster from 1/16
Љ to 3/32Љ thickness. Reinforce all joints and
interior angles with I
MPERIAL
Brand Type P or Type S Tape. Embed tape and fill beads with D
IAMOND
Brand Veneer
Basecoat Plaster and allow to set but not dry. When the alternate method of joint treatment is used, the paper tape
is embedded in S
HEETROCK
Brand Setting-Type Joint Compound and then recoated to conceal the paper tape com-
pletely. The joint compound is then allowed to set and dry. After beads and joints have been properly prepared,
apply a tight, thin coat of D
IAMOND
Brand Veneer Basecoat Plaster over the entire area, immediately doubling back
with plaster from the same batch to full thickness. Fill all voids and imperfections. Leave the surface rough and
open by roughing the surface with a sponge or fine broom once the surface has become somewhat firm. Allow the
basecoat to set and partially dry to provide proper suction for finish coat.
Concrete Block
The surface must be porous to develop proper suction as well as being rough enough to provide
adequate bond. Lightly spray the walls with water to provide uniform suction. Fill and level all voids, depressions
and joints with D
IAMOND
Brand Veneer Basecoat Plaster and allow it to set; then apply subsequent coats as with
the gypsum base application above, leaving the final surface rough and open to provide proper bonding of the
finish coat.
90%
80%
70%
60%
50%
40%
30%
20%
10%
40
50
60
70
80
90
100
110
°F
4
10
16
21
27
32
38
43
°C
Plaster Drying Conditions
Maximum Temperature
Minimum Relative Humidity
minimum temp.
for plastering
normal drying
no air movement
detectable air
movement
rapid drying
Page 2 of 4