Maintenance, Checking trowel arm straightness, Trowel arm adjustment – Multiquip JTNSW20HTCSL User Manual
Page 34
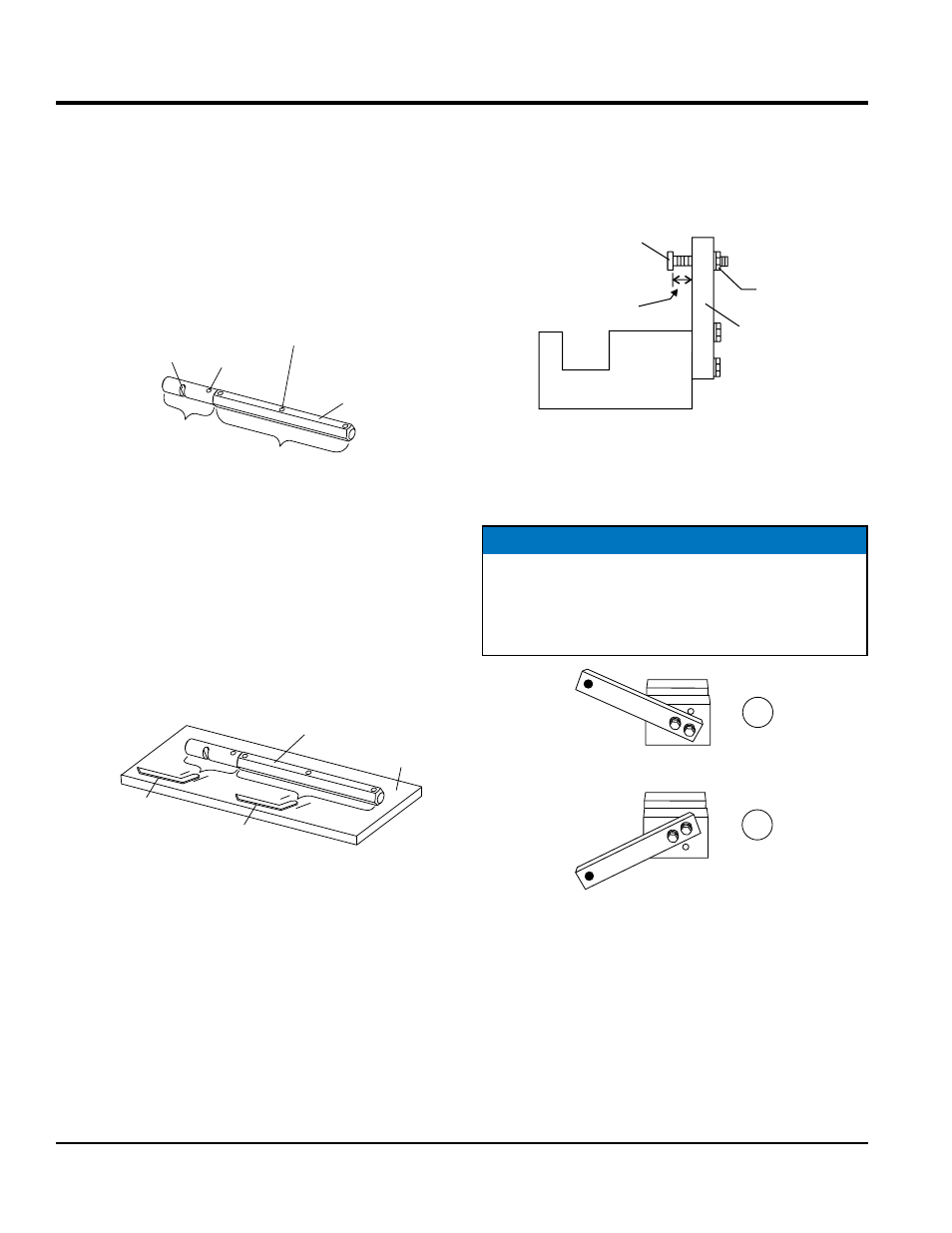
page 34 — JTNS20H/SW20H-SeRIeS RIDe-ON pOWeR TROWeL • OpeRaTION maNuaL — Rev. #4 (10/15/13)
maintenance
Checking Trowel arm Straightness
Trowel arms can be damaged by rough handling, (such as
dropping the trowel on the pad), or by striking exposed
plumbing, forms, or rebar while in operation. A bent trowel
arm will not allow the trowel to operate in a smooth fluid
rotation. If bent trowel arms are suspect, check for flatness
as follows, refer to Figure 35 and Figure 36.
Figure 35. Trowel Arm
1. Use a thick steel plate, granite slab or any surface
which is true and flat, to check all six sides of each
trowel arm for flatness.
2. Check each of the six sides of the trowel arm (hex section).
A feeler gauge of .004" (0.10 mm) should not pass
between the flat of the trowel arm and the test surface
along its length on the test surface. (Figure 36) .
Figure 36. Checking Trowel Arm Flatness
3. Next, check the clearance between the round shaft and
the test surface as one of the flat hex sections of the
arm rests on the test surface. Rotate the arm to each
of the flat hex sections and check the clearance of the
round shaft. Use a feeler gauge of .005" (0.127 mm).
Each section should have the same clearance between
the round of the trowel arm shaft and the test surface.
4. If the trowel arm is found to be uneven or bent, replace
the trowel arm.
Trowel Arm
Round Shaft Section
Trowel Arm
Hexagonal (Hex)
Shaft Section
Lever Mounting Slot
(Left Arm Shown)
Roll Pin
Hole
Blade
Attachment
Bolt Hole
(One of Three)
Flat of
Hexagonal
Shaft
(Top of Arm)
Trowel
Arm
Flat Test
Surface
Feeler Gauge
(.004 in. / 0.10 mm)
Feeler Gauge
(.005 in. / 0.127 mm)
Trowel arm adjustment
1. Locate the trowel arm adjustment tool (Figure 37) P/N
9177.
Figure 37. Trowel Arm Adjustment Tool
(Side View)
2. Ensure the fixture arm is in the proper setting (up or down)
for your trowel arm rotation as shown in Figure 38.
Figure 38. Trowel Arm Adjustment Setup
3. Shown in Figure 39 is the adjustment fixture with a
trowel arm inserted. As each trowel arm is locked into
the fixture, the arm bolt is adjusted to where it contacts
a stop on the fixture. This will consistently adjust all of
the trowel arms, keeping the finisher as flat and evenly
pitched as possible.
4. Unscrew the locking bolts on the adjustment tool and
place the trowel arm into the fixture channel as shown
Adjustment
Bolt
“Distance”
Locking
Nut
Fixture
Arm
NOTICE
Arms with
clock-wise blade rotation use the fixture arm
in the UP position (A in Figure 38). Arms with
counter
clock-wise blade rotation use the fixture with the fixture
arm in the DOWN position. (B in Figure 38).
A
B