Transducer interface, Transducer interface 31 – MTS SWIFT 40 Sensor User Manual
Page 31
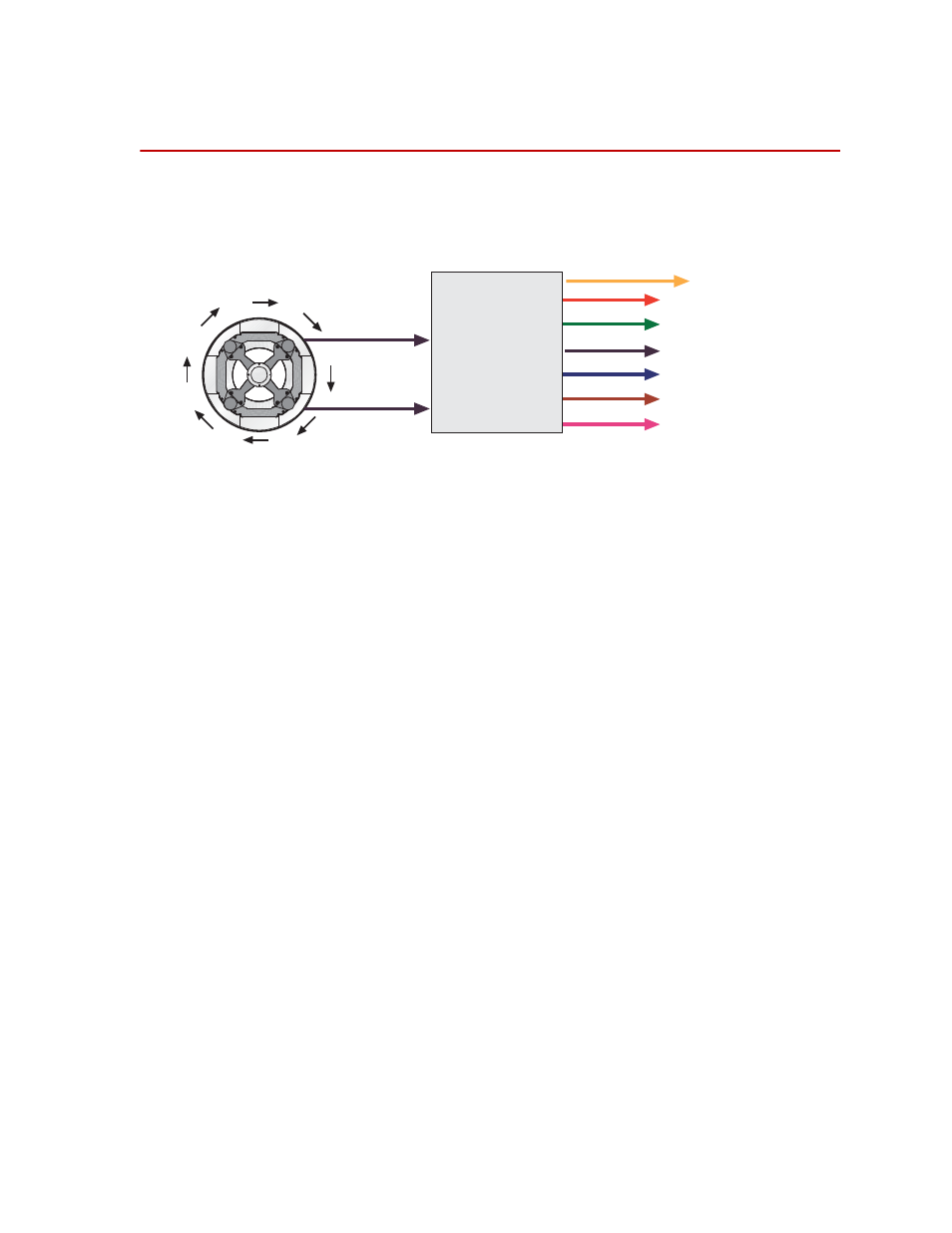
Transducer Interface
SWIFT 40 Sensors
Hardware Overview
31
Transducer Interface
The TI performs cross talk compensation, transforms the loads from a rotating to
a non-rotating coordinate system, and produces an analog output signal suitable
for any data recorder.
Cross talk
compensation
Cross talk occurs when a force is applied to one axis, but a non-real force is
measured on another axis. The SWIFT sensor design has very low inherent cross
talk. The TI compensates for any cross talk by subtracting the non-real forces
when the amount of cross talk is known.
The amount of known cross talk is determined during the calibration process.
Cross talk values will vary slightly for different rims. For example, a steel rim
will have slightly different cross talk errors than a less rigid aluminum rim.
Signal conditioning
The TI is specifically designed to be used for both spinning and non-spinning
applications. The TI performs signal conditioning and communications
functions. The output from the TI is a high-level signal suitable for input into a
multichannel data recorder or an MTS Automated Site Controller (ASC).
Fx
Fy
Fz
Mz
Mx
My
Transducer
Interface
Output signals
(± 10 Volts)
Angular
Position
Bridge
Outputs
Transducer bridge output
signals and encoder
angular position signal are
sent through slip ring
Transducer Interface
converts signals to non-
spinning vehicle coordinates,
applies calibration gains and
cross talk compensation
Force, moment, and
angle analog signals
are output from
Transducer Interface
q Angle signal
(05 Volts)
S20-08