Bryant LEGACY 580J User Manual
Page 55
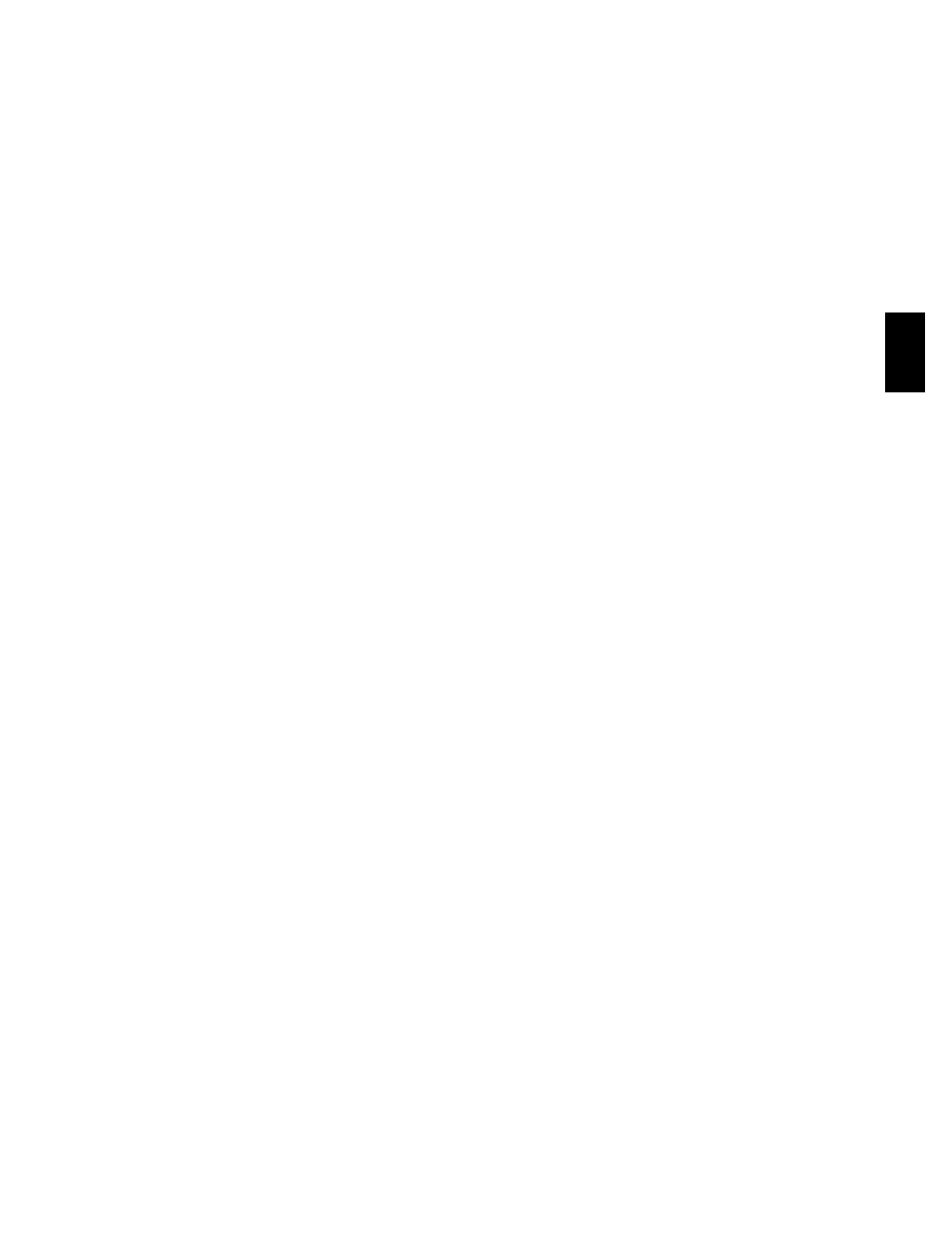
55
(1.) Standard unit shall have a thru--the--base electrical location(s) using a raised, embossed portion of the unit
basepan.
(2.) Optional, factory--approved, water--tight connection method must be used for thru--the--base electrical con-
nections.
(3.) No basepan penetration, other than those authorized by the manufacturer, is permitted.
10. Component access panels (standard)
a. Cabinet panels shall be easily removable for servicing.
b. Unit shall have one factory installed, tool--less, removable, filter access panel.
c. Panels covering control box and filter shall have molded composite handles while the blower access door shall
have an integrated flange for easy removal.
d. Handles shall be UV modified, composite. They shall be permanently attached, and recessed into the panel.
e. Screws on the vertical portion of all removable access panel shall engage into heat resistant, molded compos-
ite collars.
f. Collars shall be removable and easily replaceable using manufacturer recommended parts.
23 81 19.13.I.
Gas Heat
1. General
a. Heat exchanger shall be an induced draft design. Positive pressure heat exchanger designs shall not be al-
lowed.
b. Shall incorporate a direct--spark ignition system and redundant main gas valve.
c. Gas supply pressure at the inlet to the rooftop unit gas valve must match that required by the manufacturer.
2. The heat exchanger shall be controlled by an integrated gas controller (IGC) microprocessor.
a. IGC board shall notify users of fault using an LED (light--emitting diode).
b. The LED shall be visible without removing the control box access panel.
c. IGC board shall contain algorithms that modify evaporator--fan operation to prevent future cycling on high
temperature limit switch.
d. Unit shall be equipped with anti--cycle protection with one short cycle on unit flame rollout switch or 4 con-
tinuous short cycles on the high temperature limit switch. Fault indication shall be made using an LED.
3. Standard Heat Exchanger construction
a. Heat exchanger shall be of the tubular--section type constructed of a minimum of 20--gauge steel coated with a
nominal 1.2 mil aluminum--silicone alloy for corrosion resistance.
b. Burners shall be of the in--shot type constructed of aluminum--coated steel.
c. Burners shall incorporate orifices for rated heat output up to 2000 ft (610m) elevation. Additional accessory
kits may be required for applications above 2000 ft (610m) elevation, depending on local gas supply condi-
tions.
d. Each heat exchanger tube shall contain multiple dimples for increased heating effectiveness.
4. Optional Stainless Steel Heat Exchanger construction
a. Use energy saving, direct--spark ignition system.
b. Use a redundant main gas valve.
c. Burners shall be of the in--shot type constructed of aluminum--coated steel.
d. All gas piping shall enter the unit cabinet at a single location on side of unit (horizontal plane).
e. The optional stainless steel heat exchanger shall be of the tubular--section type, constructed of a minimum of
20--gauge type 409 stainless steel.
f. Type 409 stainless steel shall be used in heat exchanger tubes and vestibule plate.
g. Complete stainless steel heat exchanger allows for greater application flexibility.
5. Induced draft combustion motor and blower
a. Shall be a direct--drive, single inlet, forward--curved centrifugal type.
b. Shall be made from steel with a corrosion--resistant finish.
c. Shall have permanently lubricated sealed bearings.
d. Shall have inherent thermal overload protection.
e. Shall have an automatic reset feature.
23 81 19.13.J.
Coils
1. Standard Aluminum Fin -- Copper Tube Coils:
a. Standard evaporator and condenser coils shall have aluminum lanced plate fins mechanically bonded to seam-
less internally grooved copper tubes with all joints brazed.
580J