Marshalltown SG87SH SURFACE SHARK Floor Grinder User Manual
Page 24
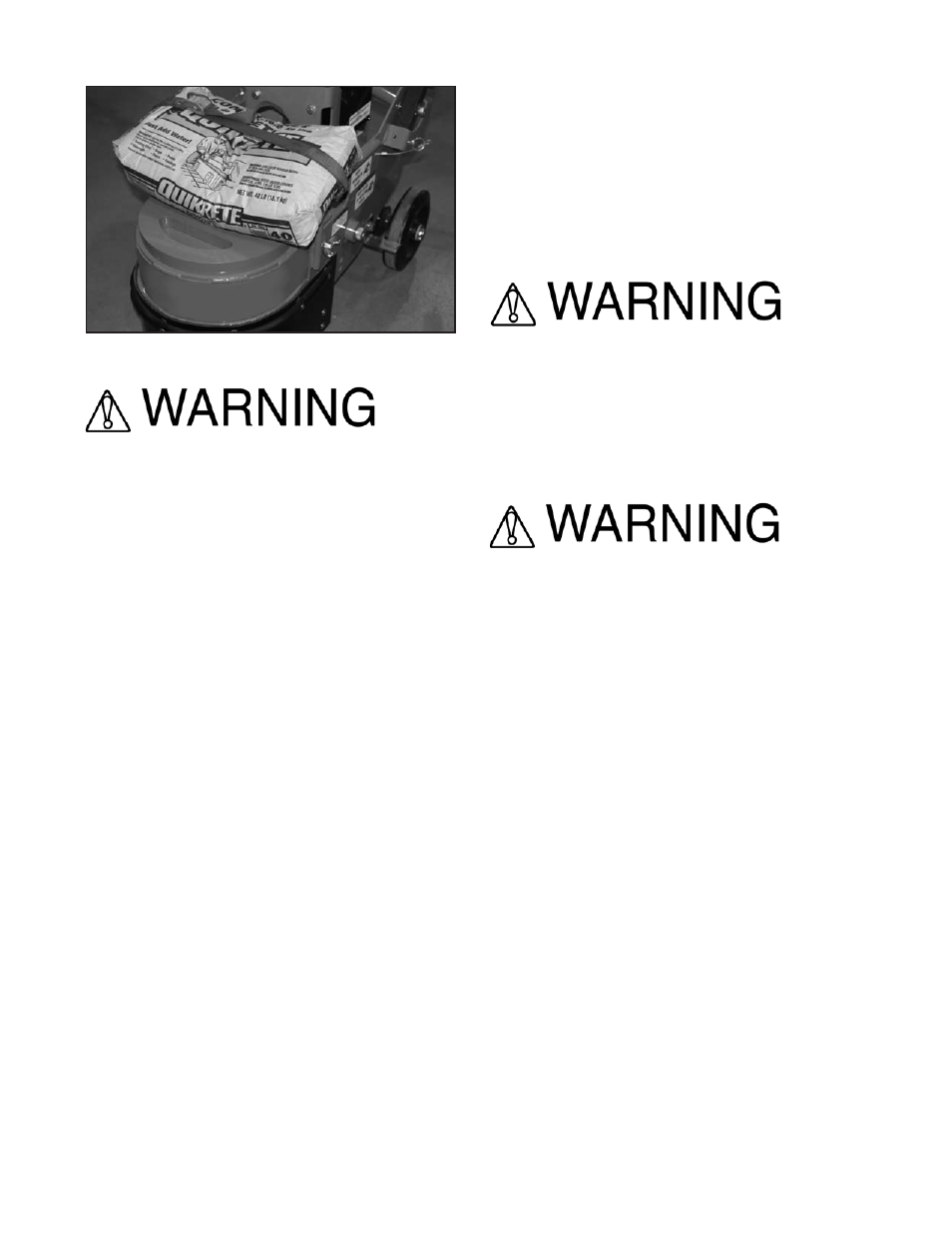
PAGE 24
SG87Sh SuRFACE ShARK FLooR GRINDER
FIGuRE 19
DO NOT OPERATE THE FLOOR GRINDER
WITHOUT ALL EXTERNAL WEIGHT PROPERLY
SECURED TO THE MAIN FRAME. A SUDDEN
CHANGE IN MOVEMENT OR DIRECTION CAN
ALLOW THE UNSECURED WEIGHT TO FALL
OFF THE FLOOR GRINDER, RESULTING IN LOSS
OFMACHINE CONTROL, PROPERTY DAMAGE
AND/ OR PERSONAL INJURY. THIS PROCEDURE
IS ESPECIALLY IMPORTANT WHEN OPERATING
THE FLOOR GRINDER ON FLOORS AND/OR
SURFACES ABOVE GROUND LEVEL.
6) The wide variety of potential work surface
materials along with the corresponding variety of job
site environments, makes it impossible to develop a
standardized operating procedure for the Floor Grinder.
use of the Floor Grinder will require constant trial and
error testing until satisfactory results are achieved.
Experience gained over time and common sense will
help minimize the amount of necessary testing. Many
factors will directly affect the operating parameters and/
or techniques utilized for a specialized job application.
Some of these factors include:
a) Work surface material yield and tensile values. As
a general rule, these values will determine material
removal rates per unit of time. Materials with high
yield and tensile values will characteristically resist/
limit material penetration. For such materials, the
accepted procedure is to make a number of multiple
passes over the work surface rather than attempt
to make a single, deep pass. The net effect is to
actually increase productivity: more material removed
in less time. other added benefits to this technique
are decreased vibration, less operator fatigue and
increased component service life.
b) higher material removal rates can sometimes be
achieved by making a series of shallow passes 90
degrees to each other to form a waffle like pattern. This
technique is especially useful when removing thicker
accumulations of rubber, paint, dirt debris, etc. from
industrial floors.
7) The grinding process on many work surface materials
can produce sparks, dust and other foreign particle
contamination.
SPARKS PRODUCED BY THE ACTIONS OF MULTI-
ACCESSORY OPTIONS AGAINST THE WORK
SURFACE (FOR EXAMPLE: STRIKING ANCHOR
BOLTS) MAY COME IN CONTACT WITH MATERIALS
THAT CAN RESULT IN A FIRE AND/OR EXPLOSION.
THIS OCCURRENCE CAN RESULT IN PROPERTY
DAMAGE AND/OR PERSONAL INJURY.
THE CREATION OF DUST AND OTHER FOREIGN
PARTICLE CONTAMINATION FROM THE
OPERATIONAL PROCESS CAN RESULT IN
PROPERTY DAMAGE AND/OR PERSONAL INJURY.
FOR SUCH OPERATING CONDITIONS, ALWAYS
WEAR A NIOSH/MSHA APPROVED DUST/MIST
RESPIRATOR. CONSULT APPLICABLE OSHA
REGULATIONS FOR SPECIFIC INFORMATION.
8) Dust and other particle contamination can be
controlled by the following methods:
a) The Floor Grinder is equipped with a 3 inch (76 mm)
outside diameter vacuum tube adapter located at the
rear of the machine. An industrial type vacuum system
and front shield assembly can be attached to the
Floor Grinder to remove/control dust and other particle
contamination from the work surface. A hose clamp
is sometimes required to properly secure the vacuum
hose to the vacuum tube. FIGuRE 20.