Marshalltown SG87SH SURFACE SHARK Floor Grinder User Manual
Page 14
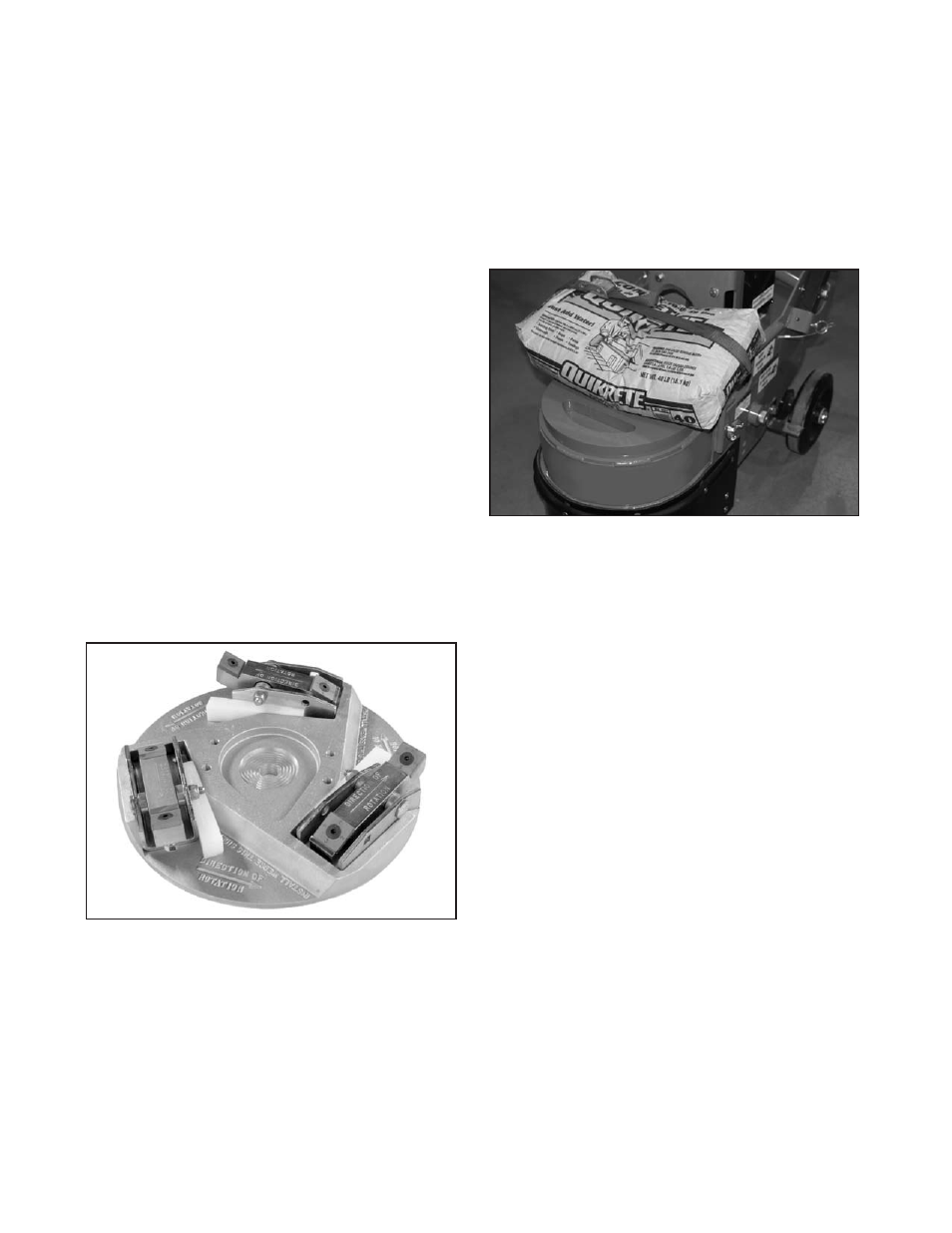
PAGE 14
SG87Sh SuRFACE ShARK FLooR GRINDER
The designation system for the grinding stones utilizes
a system similarly utilized for most abrasive products:
the larger the number, the finer the grain structure and
usually, the smoother the resulting finish.
C10 coarse grade stones are the most popular utilized
stones and result in maximum material removal
rates. They are utilized for general grinding and the
removal of trowel marks, high spots and rough sections
on concrete surfaces. The average service life is
approximately 4 to 10 hours.
SHARK TOOTH Industrial Floor Coatings Removal
System
This multi-accessory attachment is designed to remove
many urethanes, epoxies, paints, mastics and other,
similar material accumulations from concrete floor
surfaces. FIGuRE 2. Each assembly utilizes two
tungsten carbide inserts set at a precise angle. The
rotating inserts “cut and shave” against the work
surface material with a “scraping” action that removes
materials with highly productive results. To increase
the effectiveness of the inserts, the scraper block
design incorporates a Lord® type rubber mount that
helps absorb damaging shocks while allowing the
inserts to more easily follow local variations in the
surface contour. units are secured to the machine with
hardwood or plastic wedges.
FIGuRE 2
The productivity of the product is directly dependent
upon the yield and tensile strength of the material being
removed. Material thickness has also shown to have a
direct effect on overall productivity. For example, the
ShARK TooTh system is a highly productive method
for removing thick paint accumulations from factory
floors. Production rates of up to several hundred square
feet per hour can be realized. however, many thin film
(ie: 5 mill thickness and thinner) urethane coatings
present a much more difficult removal problem. Since
removal rates are also directly affected by applied
down force. up to 150 lbs of external weight can be
added to the Floor Grinder to increase productivity.
Cement blocks or stacked bags of cement make
excellent weights and can be secured with “bungy”
cords or other means with the provided holes in the top
cover. FIGuRE 3.
FIGuRE 3
Each insert provides eight scraping edges. As an edge
becomes dull and worn, the insert can be turned and
reinstalled to expose a new, sharp edge. FIGuRE 4.
When all four edges of one side become worn and dull,
the insert can be turned over to expose an additional
four edges.
Many materials such as adhesives, rubber deposits
and mastics have the tendency to extrude or smear
rather than shear from the concrete floor material.
The occurrence is also aggravated by higher ambient
temperatures. This problem can be significantly
reduced with the addition of various amounts of water
or a water saturated, fine sand combination placed
on the floor. The use of the SG87Sh Safety and
Dust Shield Assembly with the Floor Grinder is highly
recommended to contain the water/sand slurry mixture
from damaging surrounding walls and other vertical
surfaces. FIGuRE 5.