1 device identification, Device identification, Software implementation and parameter setting – Lenze 931W User Manual
Page 30
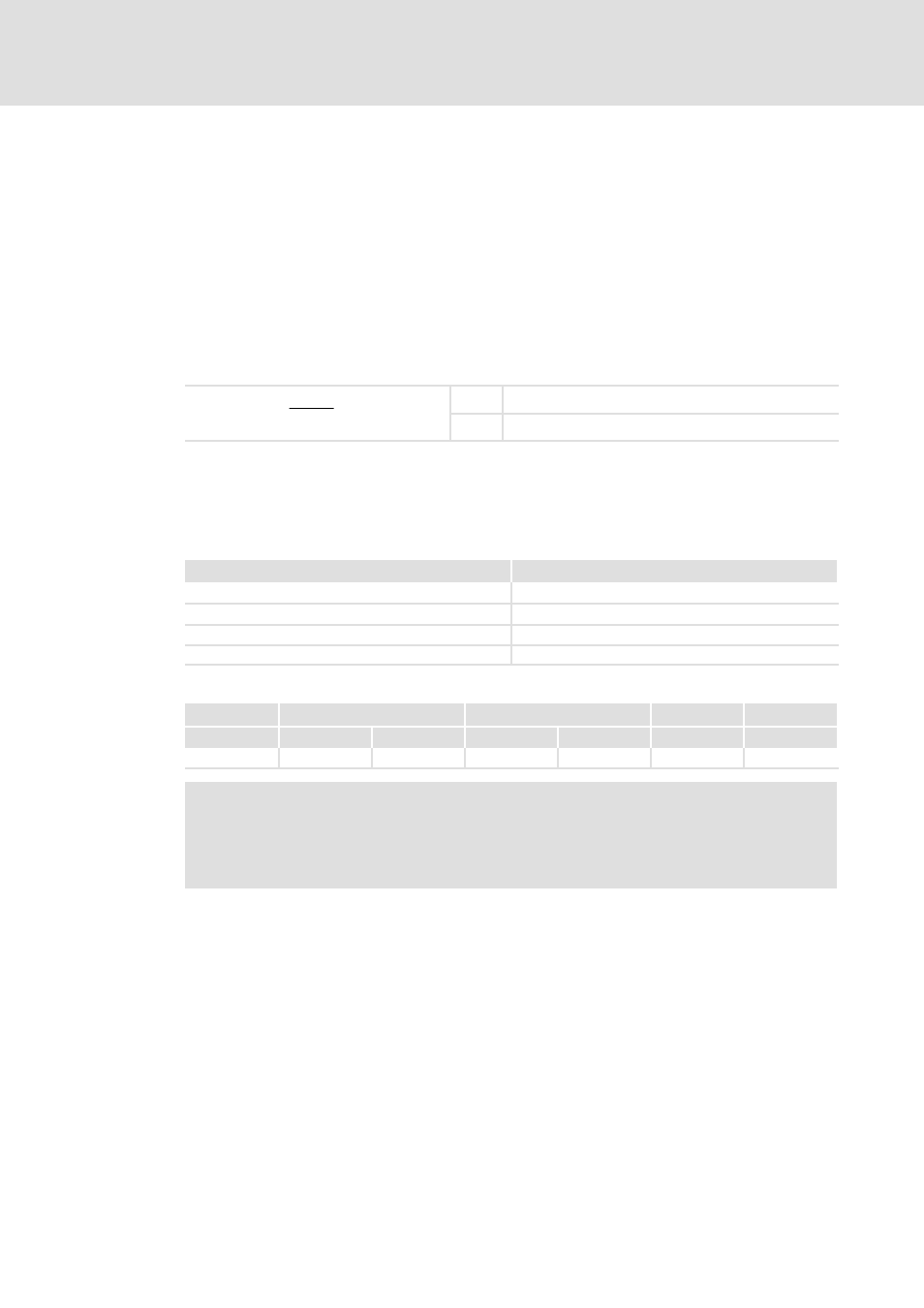
Software implementation and parameter setting
Service menu
Device identification
5
30
HB 13.0001-EN 3.0
5.3.1
Device identification
This field indicates the identification or the serial number of the drive. The specification of
the drive identification in particular is important for support requests.
Current factor
The current factor, which defines the ratio between the current and torque is a
characteristic constant of the motor. The current factor is calculated from the rated data
(rated torque and rated current of the motor and the rated current of the inverter attached)
of the drive system. This data is preset to the correct value by the factory and therefore
should not be altered:
Current factor =
M
Nmotor
I
Nmotor
x I
Ninverter
M
N
Rated torque [mNm]
I
N
Rated current [A]
Furthermore, the current factor has an impact on the maximum adjustable torque values
in the ”Service”, ”Controller” and ”Travel data sets” menus. In this connection, the torque
has to be entered in [mNm] and the current in [A]. The rated inverter currents can be
gathered from the following table. The rated data of the motor can be gathered from the
nameplate of the motor.
Inverter - supply voltage
Rated inverter current [A]
931M (24 V DC supply)
9
931M (42 V DC supply)
9
931M (230 V DC supply)
3
931M (320 V DC supply)
3
For the use of an SDS motor, the following current factors result:
Motor
SDS 035
SDS 047
SDS 056
SDS 063
Voltage
13V AC
25V AC
25V AC
210V AC
210V AC
210V AC
Current factor
426
880
1161
2182
2526
2575
Note!
For restoring the default setting, the current factor is overwritten. You can
recalculate the value by using the above-mentioned formula or gather it from
the above table.
Maximum motor torque
The maximum torque can be set. Due to the current limitation of the inverter, it can be
maximally 150 % of the current factor.
Maximum motor speed
Corresponding to the maximum torque, also a speed limitation below the maximum
speed can be effected. The maximum speed has to be selected between 0 and 6000 rpm.
Due to the mechanical loads of the rotor resulting from the centrifugal forces, speeds
above 6000 rpm are not permissible.