Maintenance/repair – Lenze MDxMA-MHxMA-MFxMA-MDERA-MHERA Three-phase AC motors User Manual
Page 47
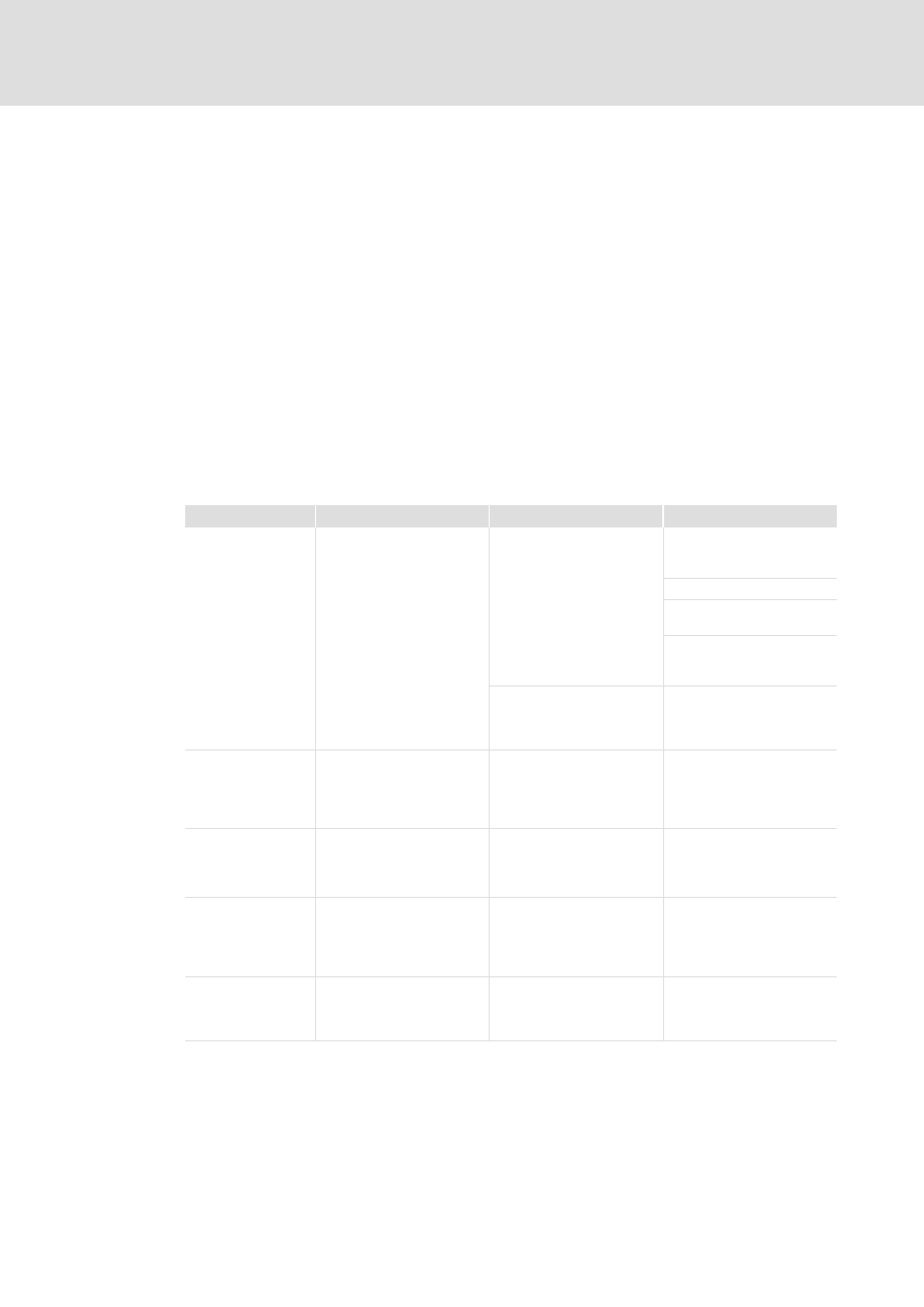
Maintenance/repair
Maintenance operations
Spring−operated brakes
l
47
BA 33.0005−EN 2.0
Wear on spring−applied brakes
The used spring−applied brakes have a low rate of wear and are designed for long
maintenance intervals.
However, the friction lining, the teeth between the brake rotor and the hub, and also the
braking mechanism are naturally subject to function−related wear which depends on the
application case (see table). In order to ensure safe and problem−free operation, the brake
must therefore be checked and maintained regularly and, if necessary, replaced (see brake
maintenance and inspection).
The following table describes the different causes of wear and their effect on the
components of the spring−applied brake. In order to calculate the useful life of the rotor
and brake and determine the maintenance intervals to be prescribed, the relevant
influencing factors must be quantified. The most important factors are the applied friction
energy, the starting speed of braking and the switching frequency. If several of the
indicated causes of wear on the friction lining occur in an application, their effects are to
be added together.
Component
Effect
Influencing factors
Cause
Friction lining
Wear on the friction lining
Applied friction energy
Braking during operation
(impermissible, holding
brakes!)
Emergency stops
Overlapping wear when the
drive starts and stops
Active braking by the drive
motor with the help of the
brake (quick stop)
Number of start−stop cycles
Starting wear if motor is
mounted in a position with
the shaft vertical, even if the
brake is open
Armature plate and
flange
Running−in of armature
plate and flange
Applied friction energy
Friction between the brake
lining and the armature
plate or flange e.g. during
emergency braking or
service brake operation
Teeth of the brake
rotor
Teeth wear (primarily at the
rotor end)
Number of start−stop cycles,
Level of the braking torque,
Dynamics of the application,
Speed fins in operation
Relative movement and
impacts between brake
rotor and brake hub
Armature plate
bracket
Armature plate, cap screws
and bolts are deflected
Number of start−stop cycles,
Level of braking torque
Load changes and impacts
due to reversal error during
interaction between
armature plate, cap screws
and guide bolts
Springs
Fatigue failure of the springs Number of switching
operations of the brake
Axial load cycle and shearing
stress on the springs due to
radial reversing error of the
armature plate
Tab. 1
Causes for wear