Flint & Walling Commander Pro 300 User Manual
Page 8
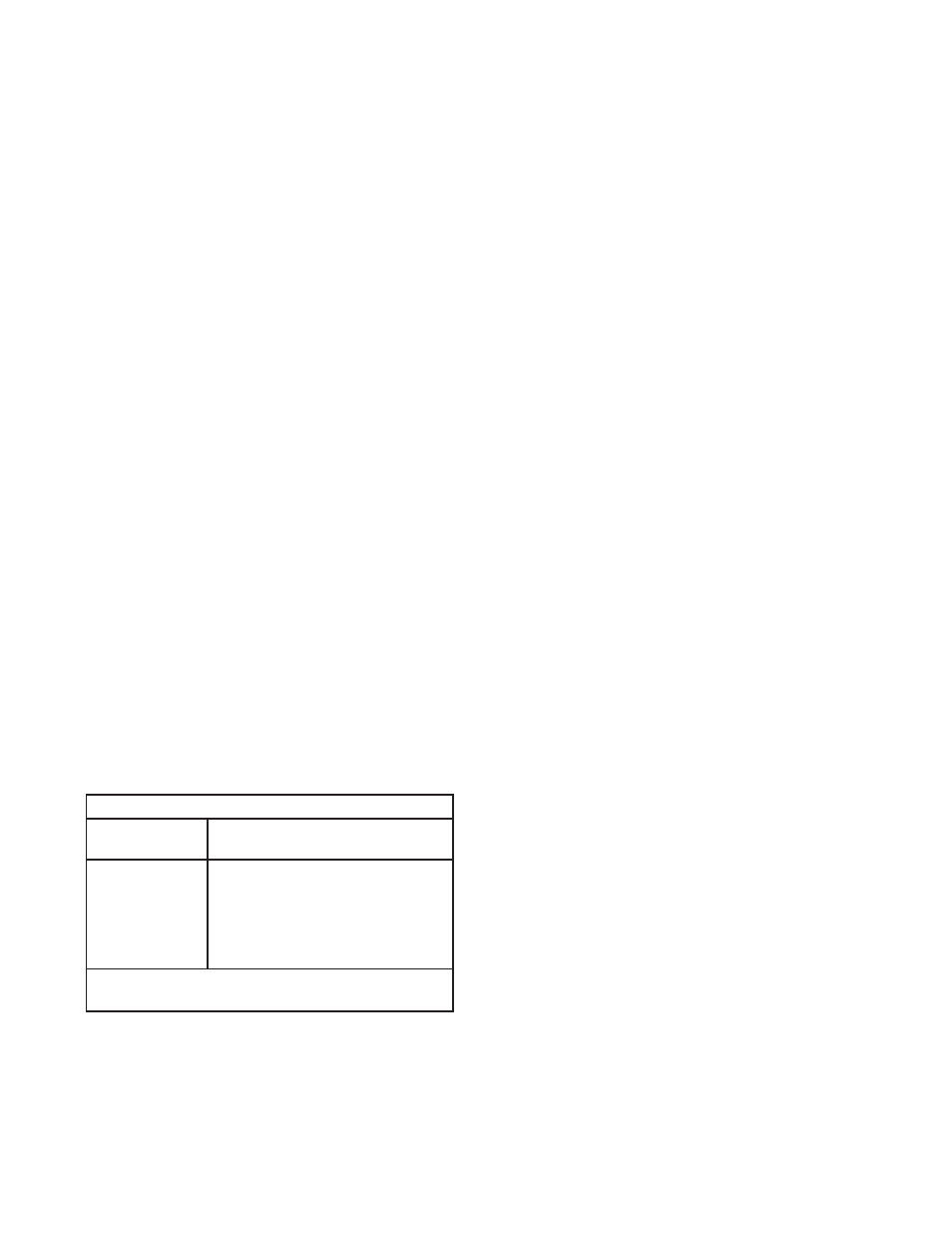
8
95 North Oak Street • Kendallville, IN 46755
pipe is installed first, rather than a long piece.
Install the check valve at the end of the first
piece of pipe prior to lowering the pump into the
well. Maintain alignment as the pump is placed
and lowered into the well, a torque arrester is
recommended. Position the torque arrestor
to within 6” of the pump discharge and clamp
arrestor to pipe. Wrap the pipe with enough tape
at top and bottom of torque arrestor to keep it
from sliding up the pipe while the pump is being
lowered into the well.
7. If not already done, splice the electrical cable
to the motor leads. The cable and ground wire
should be taped to the discharge pipe. Tape the
cable about 5 feet above the discharge and every
20 feet thereafter. Install cable guards if required
to eliminate rubbing against the well casing. Do
not let the cable drag over the edge of the well
casing. Never allow the weight of the pump to
hang on the cable alone.
8. Lower the pump into the well slowly without
forcing. Use a vise or foot clamp to hold the pipe
while connecting the next length. A boom, tripod
or pump setting rig is recommended. Lower
pump to approximately 10 feet below maximum
draw down of the water if possible and keep
approximately 10 feet from the bottom. DO NOT
set pump on bottom of well. Before each new
length of pipe is added, attach the coupling to the
top of the pipe length. This will provide a stop for
the foot clamp to hold while the next section of
pipe is being installed.
9. On a standard tank with an air volume control
a bleeder orifice is required. Install the bleeder
orifice in the discharge pipe 5 feet or more below
the snifter valve. See Figure 2 and the table
below.
WELL SEAL/PITLESS ADAPTER INSTALLATION
Distance Table
Tank Size
Gallons
Depth From Horizontal Check
Valve To Bleeder Orifice
42
82
120
220
315
525
5
10
15
15
20
20-35
Installations that use a pre-charged pressure tank
do not require a bleeder orifice.
1. All installations should have a well seal. Make
sure the seal is seated and tighten the bolts
evenly.
NOTE: Be sure to assemble the tee to the pipe
above the well seal to prevent dropping the pipe and
pump down the well as you lower it.
IMPORTANT: Well seal and piping must be
protected from freezing.
2. On a pitless adapter installation, the connection to
the system supply line is made below ground. Install
the pitless adapter following the instructions included
with particular brand or design being used in the
installation.
NOTE: Follow ALL applicable state and local
plumbing codes.
PRELIMINARY TEST RUN
1. When pump is at desired depth, install throttle
valve for preliminary test run. Wire single
phase motors through the control box, following
instructions in box regarding color coding of
wires, etc. Wire 3-phase motors through a
magnetic starter. Test cable for continuity with an
ohmmeter.
2. With pump discharge throttled, run pump until
water is clear of sand or any other impurities.
Gradually open discharge.
CAUTION: Be sure you do not stop pump before water
runs clear. This may take several hours. If pump
stops with sand in it, it will lock.
3. If pump lowers water in the well far enough
to lose prime, either lower pump in the well (if
possible) or throttle discharge to capacity of the
well.
4. If well is low capacity, use a low water level
control.
5. On 3-phase units, establish correct motor rotation
by running in both directions. Change rotation by
exchanging any two of the three motor leads. The
rotation that gives the most water flow is always
the correct rotation.
PRESSURE TANK INSTALLATION
1. On a new installation, install the pressure tank
along with the pressure switch, pressure gauge,
pressure relief valve, check valve, gate valves
and unions as shown in Figures 1 & 2.
2. On replacement pump installations be sure that
the tank system is in good operating condition, as
a water logged tank may cause pump failure.
ELECTRICAL HOOK-UP
WARNING: Since most submersible pump problems
are electrical, it is very important that all electrical
work be done properly. Therefore, all electrical hook-
up work or electrical service work should be done by a
qualified electrician or serviceman only!
WARNING: Always disconnect power source before
working on or near motor, its connected load or
control box and wiring. If the power disconnect is out
of sight, lock it in the open position and tag to prevent
unexpected application of power.