FasTest ME01 Series User Manual
Operating instructions, Installation of seals, Mounting of connector
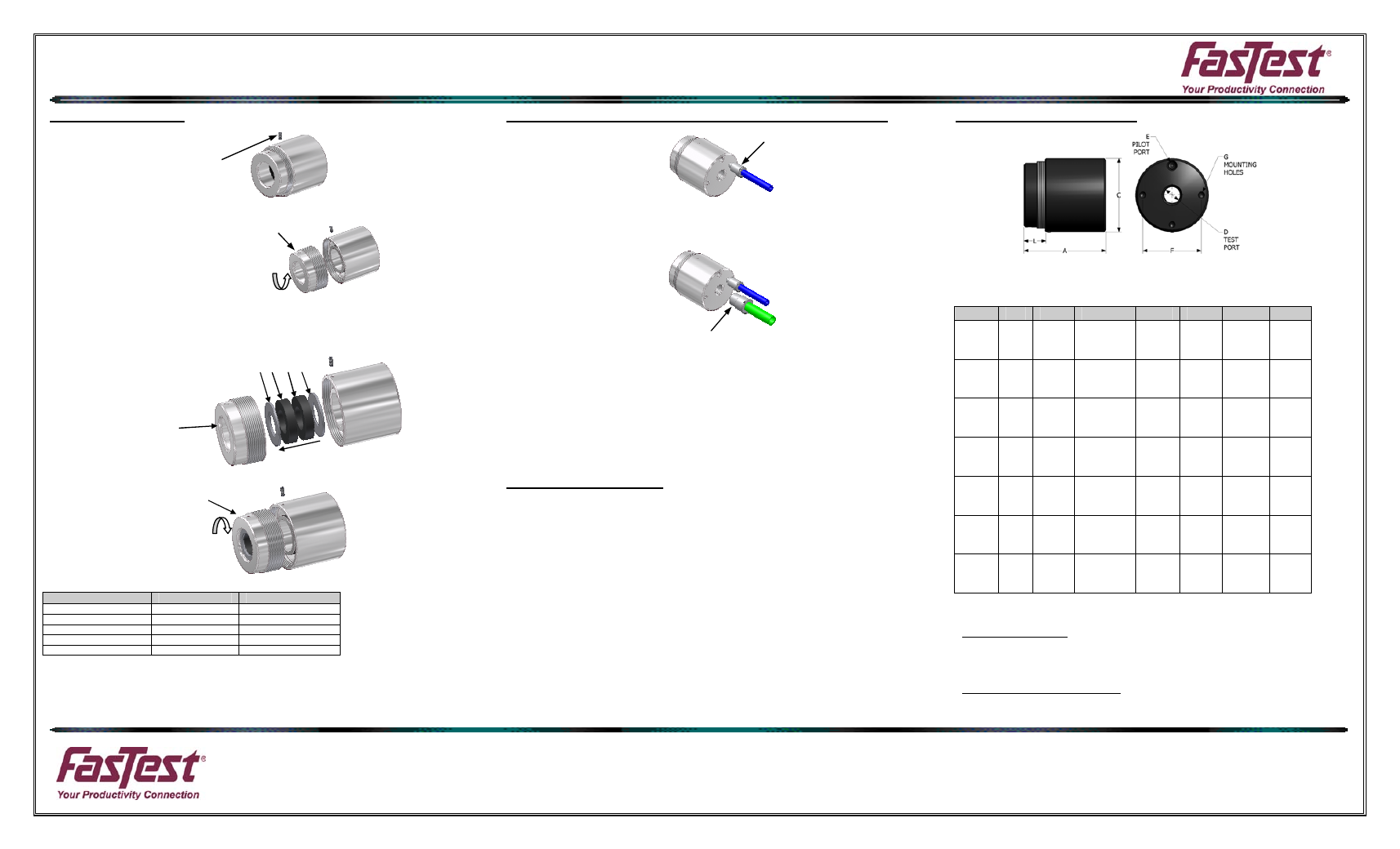
OPERATING INSTRUCTIONS
www.fastestinc.com
Roseville, MN
Ph 1-800-444-2373
Fax 651-645-7390
WP089 9/27/2010
SET SCREW
SPANNER
WRENCH
HOLE
CCW
ME SEAL SET
SEE CHART 1
ASSEMBLY DIRECTION
OF SEALS & WASHERS
SEAL
CASING
CW
SEAL CASING
WITH SEAL SET
FITTING/TUBING
TO PILOT PORT “E”
FITTING/TUBING
TO TEST PORT “D”
Installation of Seals:
• For seal install or replacement
loosen set screw on side of housing.
• Unscrew (counterclockwise) and
remove seal casing. NOTE: A spanner
wrench hole is provided for breaking
the seal casing loose if required.
• Seal sets contain elastomer seals and backup washers per Chart 1. For complete
listing of seal set size ranges see catalog.
• Verify that seals and washers are the same size.
• Assemble seal set into seal casing.
See Chart 1.
• Reassemble and tighten seal casing w/seal set to housing.
• Retighten set screw.
*Seal Set Parts Required CHART 1
Connector
Number of Seals
Number of Washers
ME01, ME01M
1
2
ME1, ME1M
1
2
ME2, ME2M
2
2
ME3, ME4, ME3M, ME4M
3
2
ME5, ME6, ME5M, ME6M
3
2
• Use of less than the listed number of seals (for less insertion depth) requires a spacer. See
FasTest
catalog. Seal Installation Instructions included with seal sets.
•
WARNING: Seals and washers must have the same size outside and inside diameters. Use of the
incorrect size seals or washers will result in loss of seal ability.
Attachment of Pilot Pressure and Test Media Supply Line:
ME MODEL CONNECTOR
• Attach pilot pressure line
to pilot port “E” from Diagram 2.
• A pneumatic regulated source is required to maximize seal life and assure optimum
seal ability for the application. The pilot pressure should be minimized to maintain
sealing on the test piece without excessive compression of the seal.
• Attach test media line to
test port “D” from Diagram 2.
• Provide a means whereby test pressure will not be introduced until the pilot
pressure required to seal is reached. The means should also provide quick exhaust
of test pressure in the event pilot pressure falls below the minimum required to seal.
Mounting of Connector:
The ME Connector must be SECURED to the test piece by a mechanical device
before proceeding.
• The test connector must be secured with a mechanical or other device to assure the
connector is not uncoupled from the test piece. The test itself will provide an un-
coupling force. The securing or holding device may be a fixture, clamp, cylinder or
other appropriate means that prevents ejection of the test piece from the connector.
Uncoupling force example:
If the test piece has a ½” O.D. and is tested at 400 psi maximum. The uncoupling force = area(πr²) x
pressure) = π x .25² x 400 = 79 lbs.
• Secured device should be designed to withstand this force and include an adequate margin for
safety.
• Do not activate the connector without an adequate and safe securing mechanism.
• Mount the FasTest ME connector to the fixture or appropriate device using either threaded
mounting holes on the rear of the connector body, (“G” Diagram 2), or appropriate adapter.
ME Connector Dimensions:
Maximum test pressure: Vacuum to 500 psi
Flow capability: Limited by “D” below
CHART 2
FE
A
C
D
E
F
G*
L**
ME01
ME01M
2.05
1.49
1/8
NPTF
1/8
BSPP
10-32
UNF
M5x.8
1.10
10-32
UNF
M5x.8
.58
ME1
ME1M
2.72
2.22
¼
NPTF
¼
BSPP
1/8
NPTF
1/8
BSPP
1.62
¼-28
UNF
M6x1
1.06
ME2
ME2M
3.50
3.11
½
NPTF
½
BSPP
1/8
NPTF
1/8
BSPP
2.50
¼-28
UNF
M6x1
1.06
ME3
ME3M
4.48
4.23
1 NPTF
1 BSPP
1/8
NPTF
1/8
BSPP
3.25
¼-28
UNF
M6x1
1.64
ME4
ME4M
4.60
5.48
1-1/2
NPTF
1-1/2
BSPP
1/8
NPTF
1/8
BSPP
4.25
¼-28
UNF
M6x1
1.64
ME5
ME5M
4.60
6.98
2 NPTF
2 BSPP
1/8
NPTF
1/8
BSPP
5.50
3/8-24
UNF
M11x1.5
1.64
ME6
ME6M
4.97
7.48
2-1/2
NPTF
2-1/2
BSPP
1/8
NPTF
1/8
BSPP
6.12
3/8-24
UNF
M11x1.5
1.64
* ME4, ME4M, ME5, ME5M, ME6, ME6M have 3 mounting holes.
**L = Minimum insertion length of test piece.
Material Specifications
Body, Housing, Piston:
Aluminum
Main Seal Washers:
Steel QPQ treated or Stainless Steel
Main Seal:
FDA approved Neoprene
O-Rings:
FDA approved Viton
Other materials available on request.
NOTE: All specifications subject to change without notice.
DIAGRAM 2