Electrical connection, Safety in case of faults, Setup – EUCHNER CMS-E-BR User Manual
Page 6: Led indicators, Service and inspection, Ec declaration of conformity
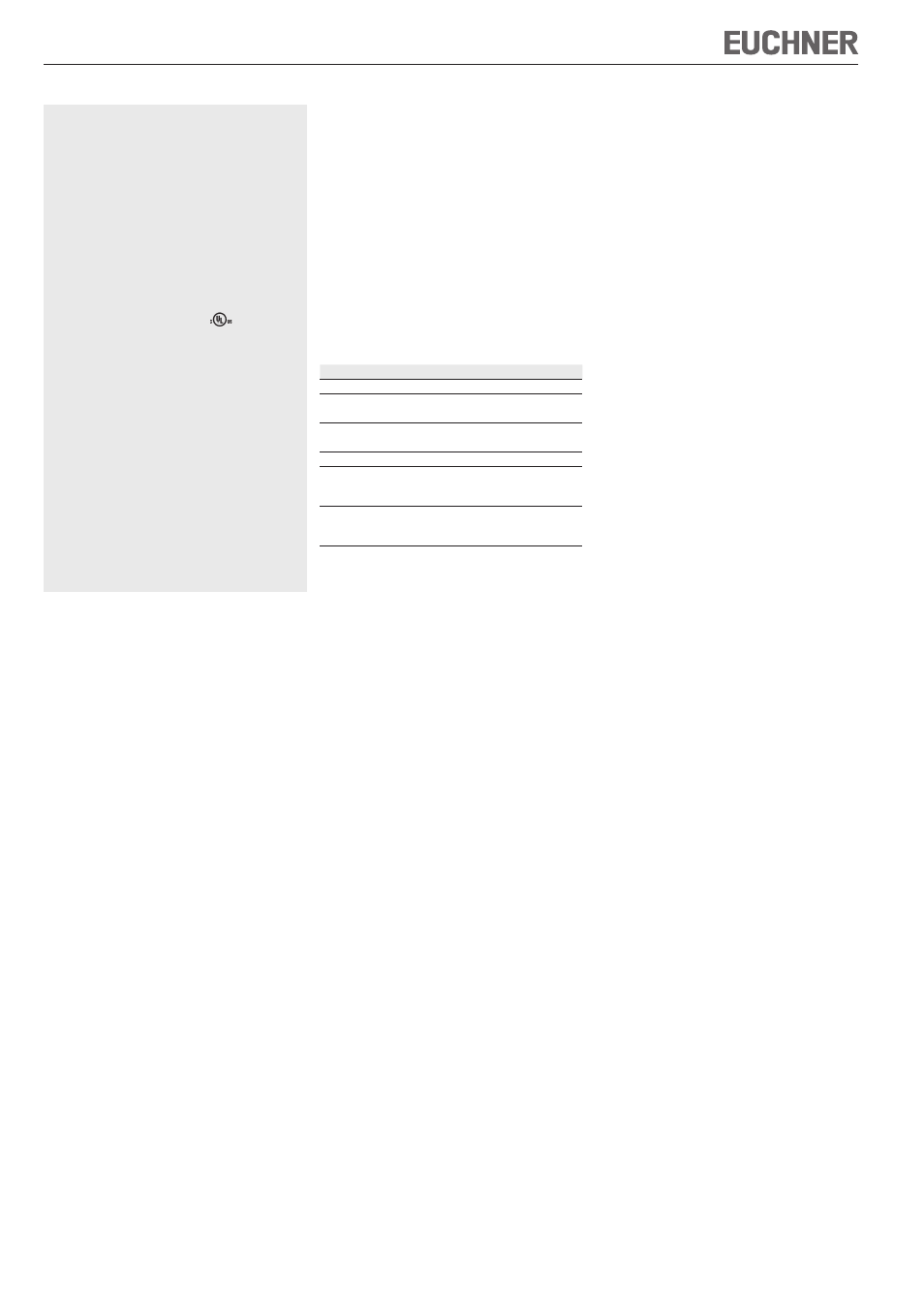
Operating Instructions Safety Switch Evaluation Units CMS-E-BR
EUCHNER GmbH + Co. KG Kohlhammerstraße 16 D-70771 Leinfelden-Echterdingen Tel. +49 711 7597-0 Fax +49 711 753316 [email protected] www.euchner.de
Subject to technical modifications; no r
esponsibility is accepted for the accuracy of this information.
© EUCHNER GmbH + Co. KG
099180-11-01/14 (translation of the original operating instructions)
Electrical connection
Warning! In case of an error, loss of the safety
function through incorrect connection.
The auxiliary contact 23/24 must not be used as
a safety output.
Lay the connection cables with protection to prevent
the risk of short circuits.
Caution! Risk of damage to equipment or malfunc-
tions as a result of incorrect connection.
All the electrical connections must either be isolated
from the mains supply by a safety transformer
according to EN 61558-2-6 with limited output volt-
age in the event of a fault, or by other equivalent
isolation measures.
For use and operation as per the
requirements,
a power supply with the feature "for use in class
2 circuits" must be used. The same requirement
applies to the safety outputs. Alternative solutions
must comply with the following requirements:
a) Electrically isolated power supply unit with a
max. open-circuit voltage of 30 V/DC and a limited
current of max. 8 A.
b) Electrically isolated power supply unit in combina-
tion with fuse as per UL 248. This fuse should be
designed for max. 3.3 A and should be integrated
into the 30 V/DC voltage section.
The devices are tested in accordance with UL 508
and are intended for mounting rail installation in the
control cabinet.
They are not tested as safety components in the
context of the UL definition (e. g. for potentially
explosive atmospheres).
All electrical outputs must have an adequate
protective circuit for inductive loads. The outputs
must be protected with a free-wheeling diode for
this purpose.
The tightening torque for the screws on the connec-
tion terminals must be 0.6 ... 0.8 Nm.
If no read heads are connected to the plug-in ter-
minals provided in the evaluation units, the bridges
supplied must be inserted in accordance with the
connection diagram.
Safety in case of faults
Terminals A1 and A2 for connection of the power
supply and all outputs (safety and door auxiliary
contact) are reverse polarity protected.
Setup
If the evaluation unit does not appear to function
when operating voltage is applied (green UB LED
does not illuminate), the unit must be returned
unopened to the manufacturer.
Check whether the safety contact is switched by
opening and closing the safety door.
LED indicators
The LEDs S1 and S2 indicate whether actuator and
read head are correctly aligned in relation to each
other. The status of the safety contact cannot be
seen from the LEDs.
Function
LED
Color
State
Operating voltage
U
B
green
ON
Contacts 23/24 and 13/14 open
OUT
red
ON
OUT
green
OFF
Contacts 23/24 and 13/14 closed
OUT
red
OFF
OUT
green
ON
Read head x (x = 1...4)
Actuator in operating distance
f
NC contact in read head is open
f
NO contact in read head is closed
Dx1
green
ON
Dx2
red
OFF
Actuator not in the operating distance
f
NC contact in read head is closed
f
NO contact in read head is open
Dx1
green
OFF
Dx2
red
ON
f
If the green and red LEDs light up simultaneously
(e.g. D11 and D22), the related actuator is not
fully in the operating distance.
f
If the actuators for all the connected read heads
are in the operating distance (or 2-pin bridges have
been fitted in the evaluation unit), safety contact
13/14 and auxiliary contact 23/24 are activated
(the green OUT LED illuminates).
f
In the evaluation unit the green LEDs are wired in
series in the following sequence: D11 - D21 - D31
- D41. This means that the green LED (e.g. D41)
can only illuminate if the upstream LEDs D11/D21/
D31 are also illuminated.
f
If the actuation speed falls below the minimum
speed, contacts 13/14 and 23/24 remain open.
Service and inspection
No servicing is required, but regular inspection
of the following is necessary to ensure trouble-free
long-term operation:
f
correct switching function
f
secure mounting of components
f
loose connections.
In the event of damage or wear and tear, the dam-
aged system component must be replaced.
If the safety doors are not frequently used, the
system must be subjected to a regular function
test as part of the inspection schedule.
EC declaration of conformity
The manufacturer named below herewith declares
that the product fulfills the provisions of the
directive(s) listed below and that the related stan-
dards have been applied.
EUCHNER GmbH + Co. KG
Kohlhammerstraße 16
70771 Leinfelden-Echterdingen, Germany
Directives applied:
f
Machinery directive 2006/42/EC
f
EMC directive 2004/108/EC
Standards applied:
f
EN ISO 13849-1:2008-12
f
EN 61000-6-3:2007
f
EN 50178:1997
f
EN 60947-5-1:2004+Cor.:2005+A1:2009
f
EN 60947-5-2:2007
f
EN 60947-5-3:1999+A1:2005
Leinfelden, January 2014
Dipl.-Ing. Stefan Euchner
Managing Director
Duc Binh Nguyen
Authorized representative empowered to draw up
documentation
The signed EC declaration of conformity is included
with the product.