EUCHNER CMS-E-BR User Manual
Page 5
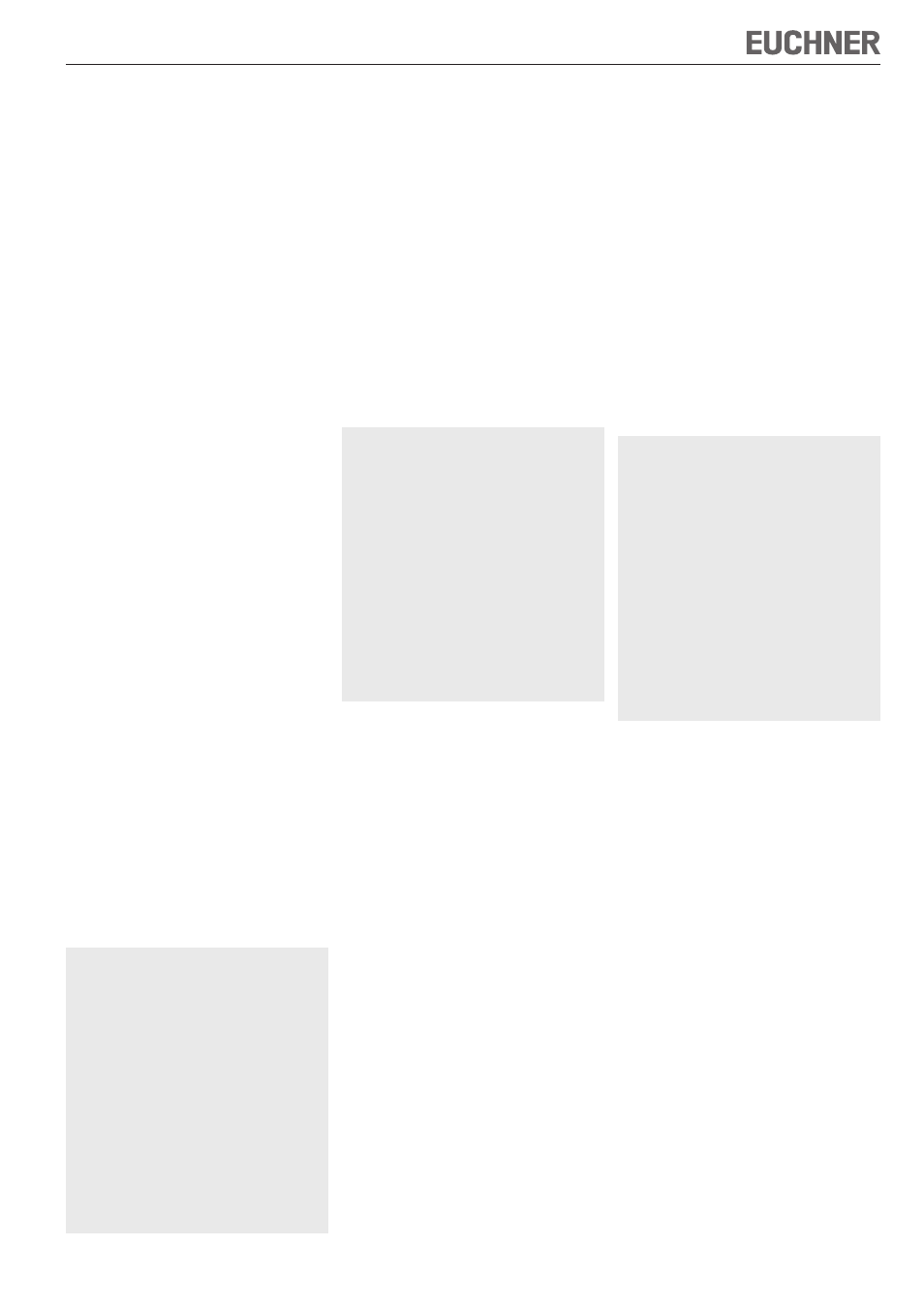
Operating Instructions Safety Switch Evaluation Units CMS-E-BR
These operating instructions are only valid
in conjunction with the operating instructions
for the relevant CMS-R-... read heads and
CMS-M-... actuators!
Correct use
Evaluation units series CMS are technical safety
devices for monitoring moveable safety guards.
Special read heads are connected for this purpose.
The system consists of evaluation unit, read head
and actuator. It forms a non-contact, magnetically
coded interlocking device with low coding level
(type 4).
In combination with a safety guard, this system
prevents dangerous machine functions from being
performed for as long as the safety guard is opened.
A stop command is triggered if the safety guard is
opened during the dangerous machine function.
This means:
f
Starting commands that cause a dangerous ma-
chine function must become active only when the
safety guard is closed.
f
Opening the safety guard triggers a stop com-
mand.
f
Closing the safety guard must not cause auto-
matic starting of a dangerous machine function.
A separate start command must be issued. For
exceptions, refer to EN ISO 12100 or relevant
C-standards.
Before safety switches are used, a risk assessment
must be performed on the machine, e.g. in accor-
dance with the following standards:
f
EN ISO 13849-1, Safety of machinery. Safety re-
lated parts of control systems. General principles
for design
f
EN ISO 12100, Safety of machinery – General
principles for design – Risk assessment and risk
reduction
f
EN 62061, Safety of machinery – Functional safety
of safety-related electrical, electronic and program-
mable electronic control systems.
Correct use includes observing the relevant require-
ments for installation and operation, e.g. based on
the following standards:
f
EN ISO 13849-1, Safety of machinery. Safety re-
lated parts of control systems. General principles
for design
f
EN ISO 14119 (supersedes EN 1088), Safety of
machinery. Interlocking devices associated with
guards. Principles for design and selection
f
EN 60204-1, Safety of machinery. Electrical equip-
ment of machines. General requirements
The evaluation unit must be used only in conjunc-
tion with the designated read heads and actuators
from EUCHNER. On the use of different read heads
or actuators, EUCHNER provides no warranty for
safe function.
Important! Important! The devices permit a safe-
ty-related stop function, initiated by a safety guard
according to Table 8 - EN ISO 13849-1: 2008-12.
The safety-related function of the safety system is
the opening of the output contacts (13/14, 23/24)
when the actuator is absent.
The user is responsible for the integration of
the device into a safe overall system. For this
purpose, the overall system must be validated,
e.g. in accordance with EN ISO 13849-2. Correct
use requires observing the permissible operating
parameters (see Technical data). If a product data
sheet is included with the product, the information
on the data sheet applies in case of discrepancies
with the operating instructions. Only components
may be used that are permissible in accordance
with the following combination options table. Refer
to the operating instructions of the corresponding
component for further information.
Exclusion of liability and warranty
In case of failure to comply with the conditions for
correct use stated above, or if the safety instruc-
tions are not followed, or if any servicing is not
performed as required, liability will be excluded and
the warranty void.
General safety instructions
Safety switches fulfill personal protection functions.
Incorrect installation or tampering can lead to severe
injuries to personnel.
Check the safe function of the safety guard par-
ticularly
f
after any setup work
f
each time after replacement of a CMS component
f
after an extended period without use
f
after every fault
Independent of these checks, the safe function of the
safety guard should be checked at suitable intervals
as part of the maintenance schedule.
For information about possible time intervals, refer
to EN ISO 14119: 2013, section 8.2.
Warning! Danger of fatal injury in the event of
incorrect connection or incorrect use.
Safety switches must not be bypassed (bridging
of contacts), turned away, removed or otherwise
rendered ineffective. Pay particular attention to
EN ISO 14119: 2013, section 7, regarding the
possibilities for bypassing an interlocking device.
The device is only allowed to be installed and placed
in operation by authorized personnel
f
who are familiar with the correct handling of safety
components
f
who are familiar with the applicable EMC regula-
tions
f
who are familiar with the applicable regulations on
health and safety and accident prevention
f
who have read and understood the operating
instructions.
Function
The safety switch CMS consists of an evalua-
tion unit, read head and actuator and is only
functional in specific combinations (see com-
bination options)!
The evaluation unit CMS-E-BR is used for monitoring
from one to four safety doors.
The read heads CMS-R-… have electrically separate
reed contacts with NC contacts and NO contacts.
If the actuator is in the operating distance, the
contacts in the read head are switched by the
magnetic field. The switching status of the contacts
is displayed on the evaluation unit's LEDs (see sec-
tion LED indicators). Due to the NC/NO contact
combination in the read head, the evaluation unit
expects to receive antivalent signal changes. The
evaluation unit converts this information and trans-
fers the safety guard state to the control system
via a safety contact.
If the actuators for all the read heads connected are
in the operating distance, safety contact 13/14 is
closed. The additional auxiliary contact 23/24 is
also closed.
When the safety door is opened or closed, the evalu-
ation unit is checked to ensure that it is functional.
In this way internal errors from the read head to the
control unit output can be detected.
If an error is detected, the evaluation unit changes
to a blocked state. The safety contact remains in
the open state.
The auxiliary contact is electrically isolated from the
safety contacts.
If contactors are used, the switching contacts can be
monitored for a possible malfunction by the evalua-
tion unit via a feedback loop. A start button can also
be connected to the evaluation unit.
The evaluation unit status is displayed visually by
means of LED indicators.
f
In the case of a monitored feedback loop, safety
contact 13/14 is only activated if feedback loop
Y1/Y2 was closed before the actuators were
moved into the read heads’ operating distance.
f
A start button must not be incorporated into the
feedback loop.
f
In the case of unmonitored feedback loops, the
2-pole bridge supplied with the evaluation unit must
be connected to terminals Y1/Y2.
f
When the actuator is moved out of the switch-off
distance, it is ensured that safety contact 13/14
and auxiliary contact 23/24 switch only when the
actuator is moved back into switch-on distance
s
ao
after having exceeded the switch-off distance
(see combination options table)
f
If the actuator is moved slowly toward the read
head in lateral approach direction Z, the evaluation
unit changes to the blocked state. To cancel the
blocked state, the actuator must again be moved
beyond the switch-off distance.
Mounting
Caution! The evaluation unit must be mounted in a
control cabinet with a minimum degree of protec-
tion of IP 54. A snap-in element on the rear of the
device is used for fastening to mounting rails. If
several evaluation units are mounted side by side
in a control cabinet without air circulation (e.g. fan),
a minimum distance of 10 mm must be maintained
between the evaluation units. This distance enables
the heat from the evaluation unit to dissipate.
Caution! Risk of damage to equipment as a result
of incorrect installation. Read heads or actuators
must not be used as a mechanical end stop. Fit
an additional end stop for the movable part of the
safety guard.
Important! From the assured switch-off distance
s
ar
, the safety outputs are safely shut down. If the
actuator is installed flush, the switching distance
changes as a function of the installation depth and
the safety guard material.
Note the following points:
Actuator and read head must be easily accessible
for inspection and replacement.
The switching operation must only be triggered by
the specific actuator designated for this purpose.
Actuator and read head must be fitted
f
so that when the safety guard is open up to the
distance Sar (assured switch-off distance), a
hazard is excluded.
f
the actuator is positively mounted on the safety
guard, e.g. by using the safety screws included.
f
they cannot be removed or tampered with using
simple means. Pay particular attention to EN ISO
14119: 2013, section 7, regarding the possibili-
ties for bypassing an interlocking device.