An150 – Cirrus Logic AN150 User Manual
Page 4
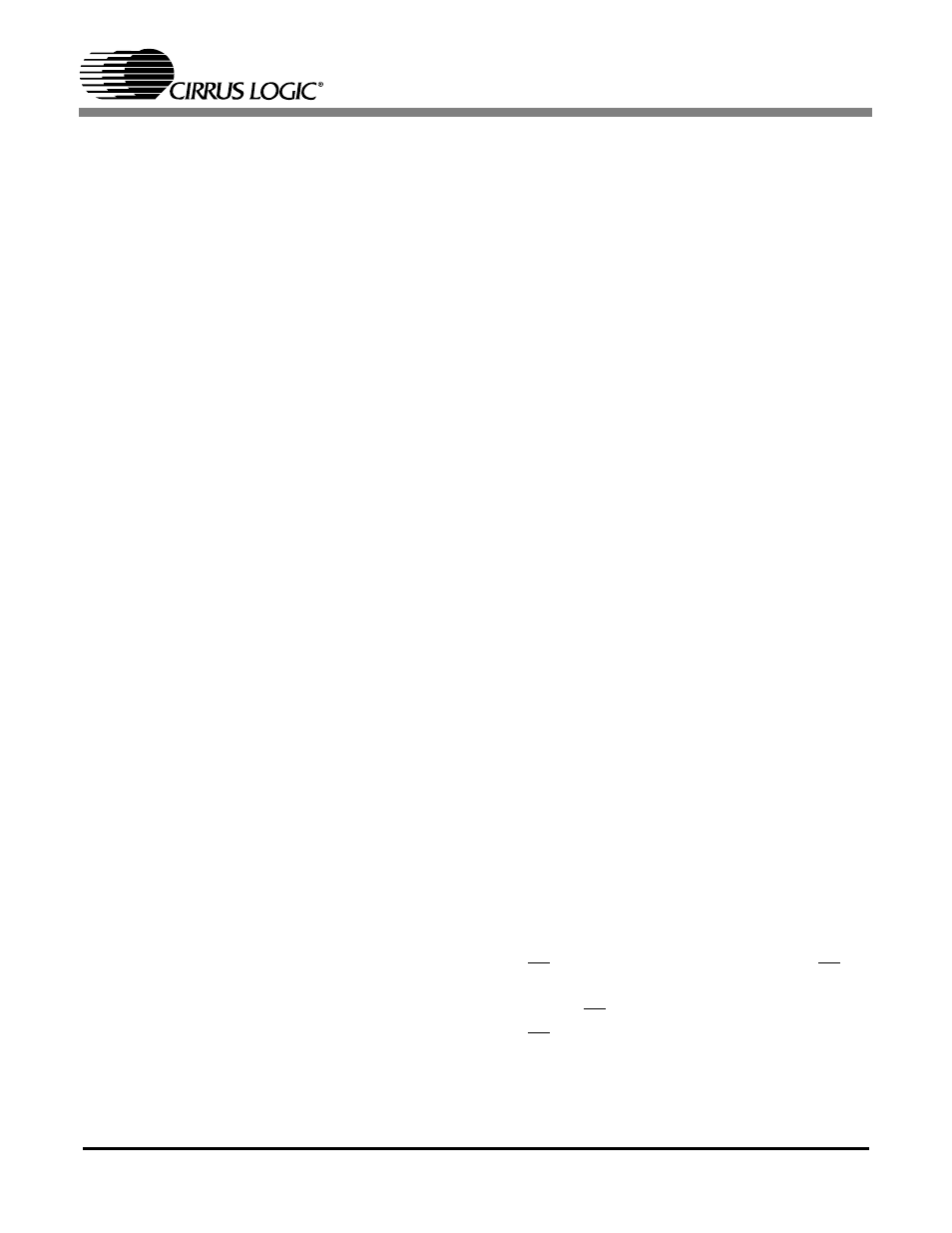
AN150
4
AN150REV2
of one LSB. For a 5 mV input signal when the LSB
size is 4 nV, the expected output code (decimal)
from the converter would be 1,250,000.
What is the relationship of the VREF input
voltage and the VRS bit to the analog inputs
of the converter?
The voltage present on the VREF+ and VREF- in-
puts have a direct relationship to the input voltage
span of the converter. The differential voltage be-
tween the VREF inputs ((VREF+) - (VREF-))
scales the span of the analog input proportionally.
If the VREF voltage changes by 5%, the analog in-
put span will also change by 5%. The VREF input
voltage does not limit the absolute magnitude of the
voltages on the analog inputs, but only sets the
slope of the transfer function (codes output vs. volt-
age input) of the converter. The analog input volt-
ages are only limited with respect to the supply
voltages (VA+ and VA-) on the part. See the
“Common-mode + signal on AIN+ or AIN-” dis-
cussion in this document for more details on these
limitations.
The VRS bit in the configuration register also has a
direct effect on the analog input span of the con-
verter. When the differential voltage on the VREF
pins is between 1 V and 2.5 V, the VRS bit should
be set to ‘1’. When this voltage is greater than 2.5
V, the VRS bit should be set to ‘0’. When set to ‘0’,
a different capacitor is used to sample the VREF
voltage, and the input span of the converter is
halved. The proper setting of this bit is crucial to
the optimal operation of the converter. If this bit is
set incorrectly, the converter will not meet the data
sheet noise specifications.
The purpose of the VRS bit is to optimize the per-
formance for two different types of systems. In
some systems, a precision 2.5 V reference is used
to get absolute accuracy of voltage measurement.
Other systems use a 5 V source to provide both the
reference voltage and an excitation voltage for a ra-
tiometric bridge sensor. The performance of the
system can be enhanced by selecting the appropri-
ate reference range.
In a system that is performing ratiometric measure-
ments, using a 5 V reference is usually the best op-
tion. Ratiometric bridge sensors typically have a
very low output voltage range that scales directly
with the excitation voltage to the sensor. Because
the converter’s input span can be the same with ei-
ther a 2.5 V reference or a 5 V reference, and the
voltage output from the ratiometric sensor will be
twice as large with a 5 V excitation, the system can
achieve higher signal to noise performance when
the sensor excitation and the voltage reference are
at 5 V.
For systems in which absolute voltage accuracy is
a concern, using a 2.5 V reference has some advan-
tages. There are a wide variety of precision 2.5 V
reference sources available which can be powered
from the same 5 V source as the ADC. However,
most precision 5 V references require more than 5
V on their power supplies, and a second supply
would be needed to provide the operating voltage
to a voltage reference. Since the same input ranges
are available with either reference voltage, a 2.5 V
reference provides a more cost and space-effective
solution. Additionally, for systems where the 1X
gain range is used, a 2.5 V reference voltage gives
the user the option of using the self gain calibration
function of the ADC, where a 5 V reference does
not.
What are the noise contributions from the
amplifier and the modulator?
The amplifier used in the 2X-64X gain ranges of
the part has typical input-referred noise of 6
nV/
√
Hz for the -BS versions, and 12 nV/
√
Hz for
the -AS versions. The modulator has typical noise
of 70 nV/
√
Hz for the -BS versions, and 110
nV/
√
Hz for the -AS versions at word rates of 120
samples/s and less. At word rates higher than 120
samples/s, the modulator noise begins to rise, and
is difficult to model with an equation. The