RMS Technologies IMCE23 INTERGRATED MOTOR+CONTROLLER +DRIVER+ENCOD User Manual
Page 21
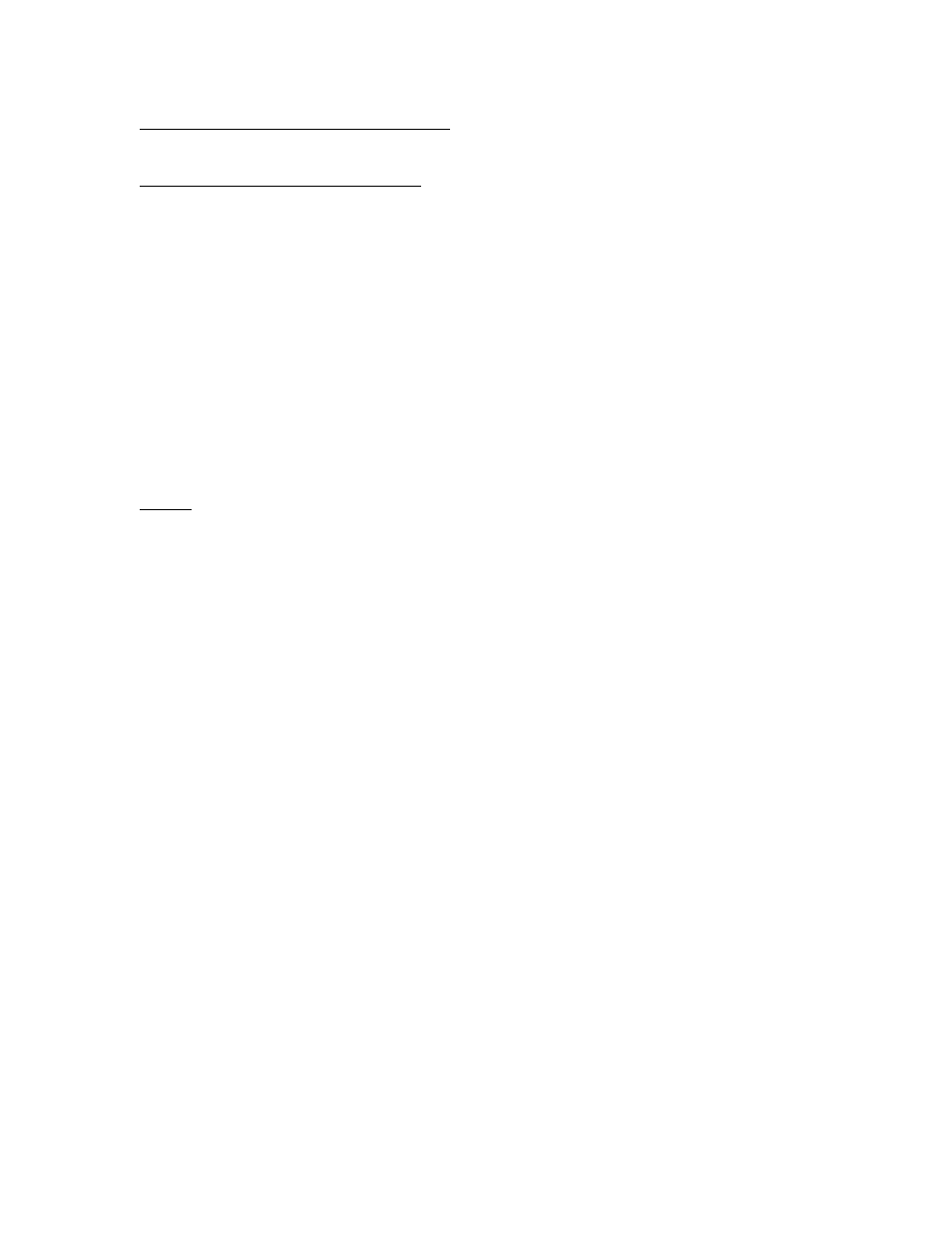
R356 Controller & Driver
Page 21
Version 1.06
RMS Technologies
2/17/2010
Third: Set the Overload Timeout Value:
This is is the number of re-tries allowed under a stall condition: /1au10000R
(default is 10)
Fourth: Enable the Feedback mode:
Zero the positions prior to enabling the feedback mode: /1z0R
Issue /1n8R to enable the feedback mode.
Overload Report Mode
Overload report mode when enabled, will compare the encoder value to the
commanded position at the end of a move and report an error if the two values do
not match within the range given by “aC”. When this error occurs the drive will exit
from any loops or strings it may be executing.
Overload report mode is enabled by /1n16R, and requires the encoder ratio to be
entered correctly via the “aE” command. Issue a /1zR to zero both the encoder and
position counter just prior to issuing /1n16R. Only the Position Correction mode or
the Overload Report mode may be turned on at one time.
Notes:
1. When any command is received by the drive it will always respond with its
status. The drive will only accept a command when it is not busy. This status
byte received must be checked to ensure that the unit was not busy and that
the command was accepted. This is especially important when position
correction mode is enabled, because the drive may be attempting to correct
position all by itself, and will reject an externally (via RS232) received
command if it is busy in the middle of a correction move.
2. When position correction mode is enabled, /1n8R, then the drive will keep
retrying any stalled moves, and will NOT halt any strings or loops upon
detection of a stall.
3. During position correction mode /1T will halt any move, but there is a
possibility that the drive may instantly reissue itself a position correction
command, especially if it is fighting a constant disturbance. It may be
necessary to issue a /1n0R to positively halt a move in progress.
4. Position correction mode is inhibited if the encoder underflows and goes
negative (but will automatically resume if a move is made into the positive
range). If position correction is required at the zero point, please redefine
zero to be a slightly positive number with the “z” command. Eg /1z10000R
5. If the encoder ratio is changed from its default of 1000, the allowed max
position will be decreased from +2^31 by the same ratio.
Peak current versus Amps/Phase
Where does the 1.4 times come from? Current is continuously changing when a
motor steps. If the motor is rated for 1.0 A/Ph, it may receive 0 Amps, 1 Amp, 1.4
Amps, or anything in between if you are microstepping. For ease of explanation, we
will look at the current waveform when we half step, or set the driver/controller to
2x microstepping.
If we take a look at both the A and B phases, and plot on an X-Y chart of when each
phase receives current, and how much it receives, it will look like the chart below.