RMS Technologies IMCE23 INTERGRATED MOTOR+CONTROLLER +DRIVER+ENCOD User Manual
Page 20
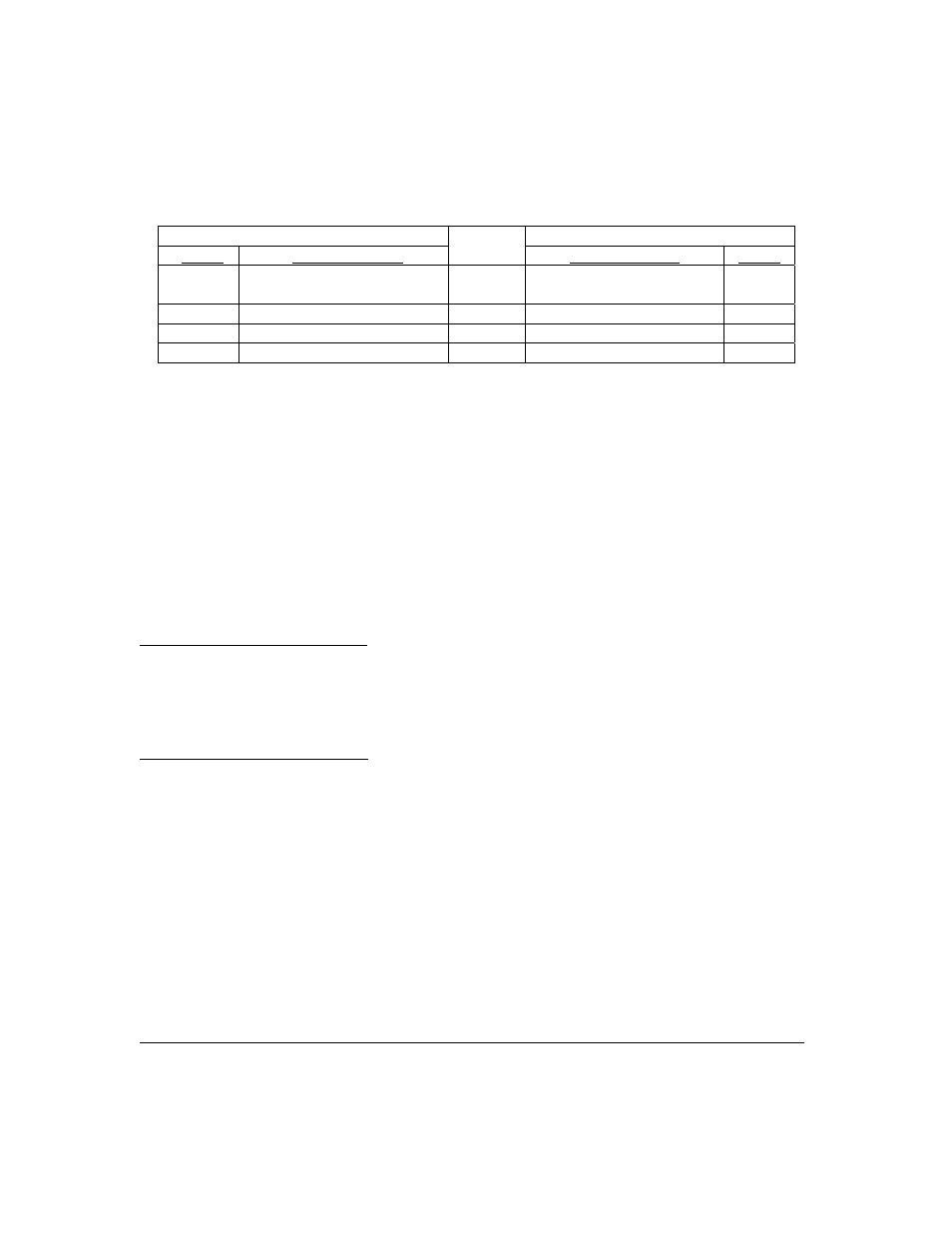
R356 Controller & Driver
Page 20
Version 1.06
RMS Technologies
2/17/2010
How to connect with old cable:
If you have a cable with a Red 4-Pin connector, simply cut off this connector,
strip the wires and reconnect to a 3-Pin connector in the following manner:
Old 4-Pin cable
Connect
to
New 3-Pin cable
Pin # Color/function Color/function
Pin #
Pin 1
Red (PWR)
Æ
Connect to main power
supply
--
Pin 2
Green (GND)
Æ
Green (GND)
Pin 2
Pin 3
Brown RS485 B (+)
Æ
Brown RS485 B (+)
Pin 3
Pin 4
Black/white RS485 A (-)
Æ
Black/white RS485 A (-) Pin 1
Encoder Usage
The R356 can do closed loop position correction. The encoder connects to the board
internally.
Position Correction Mode
Position correction mode, when enabled will issue steps to the motor until the
encoder reads the correct position. Once enabled, positions are given in
Quadrature encoder counts of the encoder – not in microsteps. If the motor
stalls during a move then this mode will reattempt the move until the encoder reads
the correct number, or until it has tried a certain number of times and times out.
First: Set The Encoder Ratio:
Encoder ratio = [(Microstep * 200 steps/rev) / (CPR *4)]*1000
This must be a whole number after you multiply by 1000.
For example: a 1.8° motor set to 256x microstepping with a 1000 count encoder:
Encoder ratio = ((200 * 256)/(1000*4))*1000 = 12800
Set encoder ratio: /1aE12800R
If Encoder Ratio is Unknown:
Follow these steps:
1. Issue a /1n0R to clear any special modes
2. Issue a /1z0R to set position of encoder and controller to zero
3. Issue a /1A100000R and ensure the move completes at a velocity that does
not stall.
4. Issue a /1?0 to read current position. This should be 100000.
5. Issue a /1?8 to read the encoder position
6. Issue a /1aE0R which auto divides these two numbers
7. Issue a /1?aE which read backs the encoder ratio computed
8. This value is a rough guide and may be a few counts off due to inaccuracies in
the motor position and run-out of the encoder, but use the EXACT number
that was returned and set it with a /1aEXXXXR. Or, please contact RMS
Technologies and provide us with your motor part number and we can look up
the encoder CPR for you.
Second: Set the Error in Quadrature Encoder Ticks allowed before correction begins:
/1aC50R (default is 50) Motor will move 50 encoder ticks away from desired position
before position correction takes place. If aC is set to too small of a value, the motor
may oscillate back and forth trying to locate the exact position. Use a larger aC
value.