Install the mechanical seal – Goulds Pumps VIC - IOM User Manual
Page 28
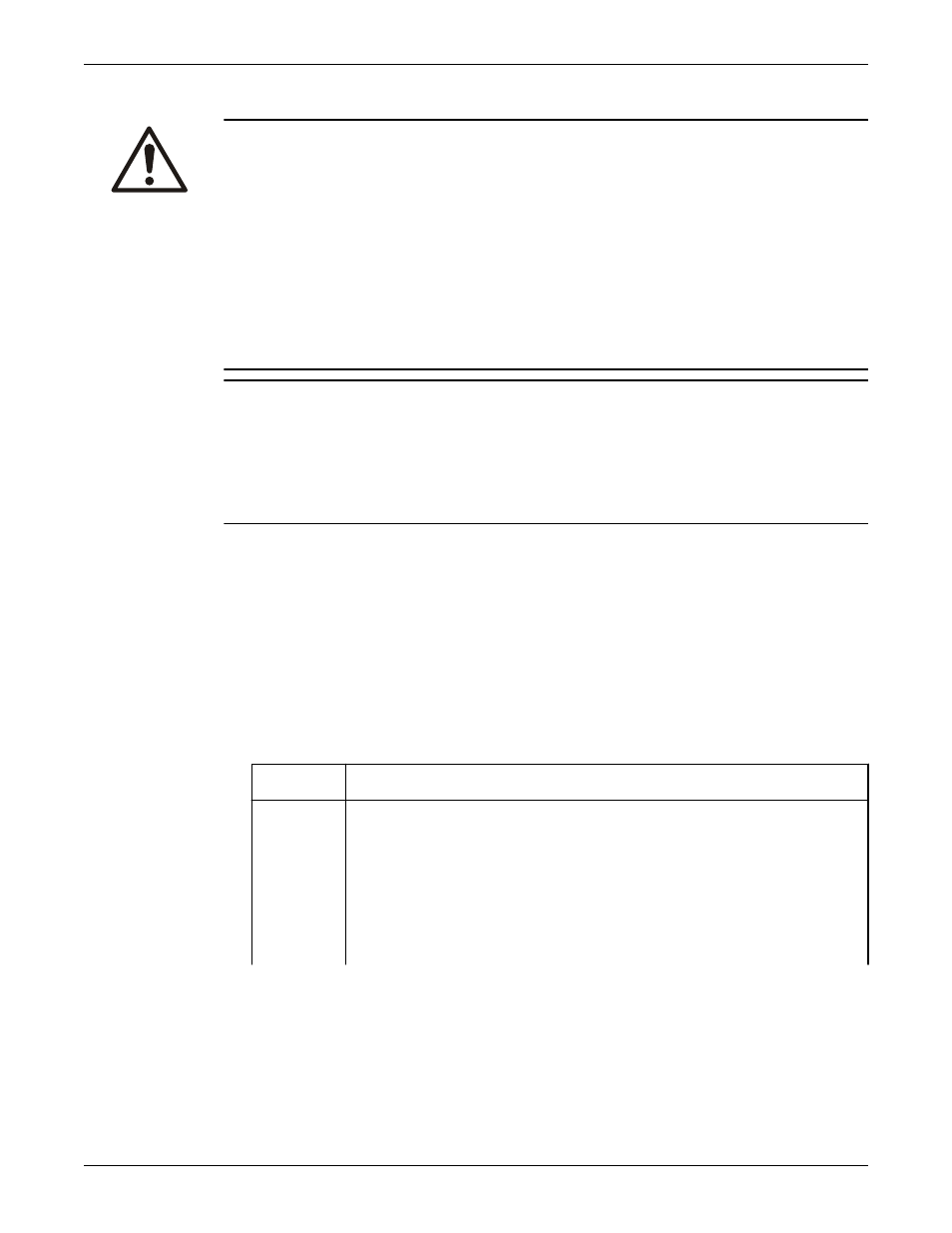
Install the mechanical seal
CAUTION:
Sparingly lubricate the shaft and sleeve ID with the lubricant included with the mechanical seal or
recommended by the mechanical seal manufacturer. You can use these lubricants for water service when
no lubricant is supplied or recommended by the mechanical seal manufacturer:
• Light oil (SAE #10 or 20)
• Dow Corning #4 grease
• Silicone lubricant
• Wax or clay
• Soapy water
Oil-based lubricants will damage EPR / EPDM elastomer O-rings. Silicone lube and soapy water are safe
for EPR / EPDM elastomer O-rings.
NOTICE:
• Do not bump carbon inserts against the shaft as they can chip, crack, or break.
• Do not overtighten the capscrews on the gland. This can distort the seal seat and cause seal failure.
• Do not remove the seal spacer or eccentric washer, adjust the seal, or tighten the setscrews until after
you adjust the impellers.
• Reset the seal after you adjust the impeller.
1. Install the O-ring or gasket between the seal housing and seal:
a) Install the seal over the shaft and ease it into position against the face of the seal box.
b) Take care when you pass the sleeve and O-ring over the keyways or threads in order to avoid
damage to the O-ring.
2. Position the seal gland on the discharge-head seal housing and secure it with capscrews.
3. Tighten the capscrews gradually and uniformly in a criss-cross pattern, taking two or three passes.
4. Install all seal piping as required.
5. Before you make the final connections of the sealing-liquid pressurizing lines, make sure the seal
housing and all sealing-liquid lines are flushed free of dirt, scale, and other particles.
6. Install the driver and coupling.
7. Take these flatness and concentricity measurements:
Runout of
driver shaft
Procedure
Concentricity
of driver shaft
1. Install the dial indicator as shown, with the base attached to the motor support.
2. Rotate the driver shaft by hand while you read the dial.
Make sure that the runout does not exceed NEMA standards, 0.002 in. (0.05
mm) maximum TIR.
3. If the indicator reads higher than 0.002 in. (0.05 mm) TIR, loosen the four driver
hold-down bolts and relocate the driver on the motor base register.
4. Obtain the desired position.
5. Tighten the hold-down bolts and repeat the indicator reading.
Installation (Continued)
26
Model VIC Installation, Operation, and Maintenance