Dow FROTH-PAK Refill Systems User Manual
Page 21
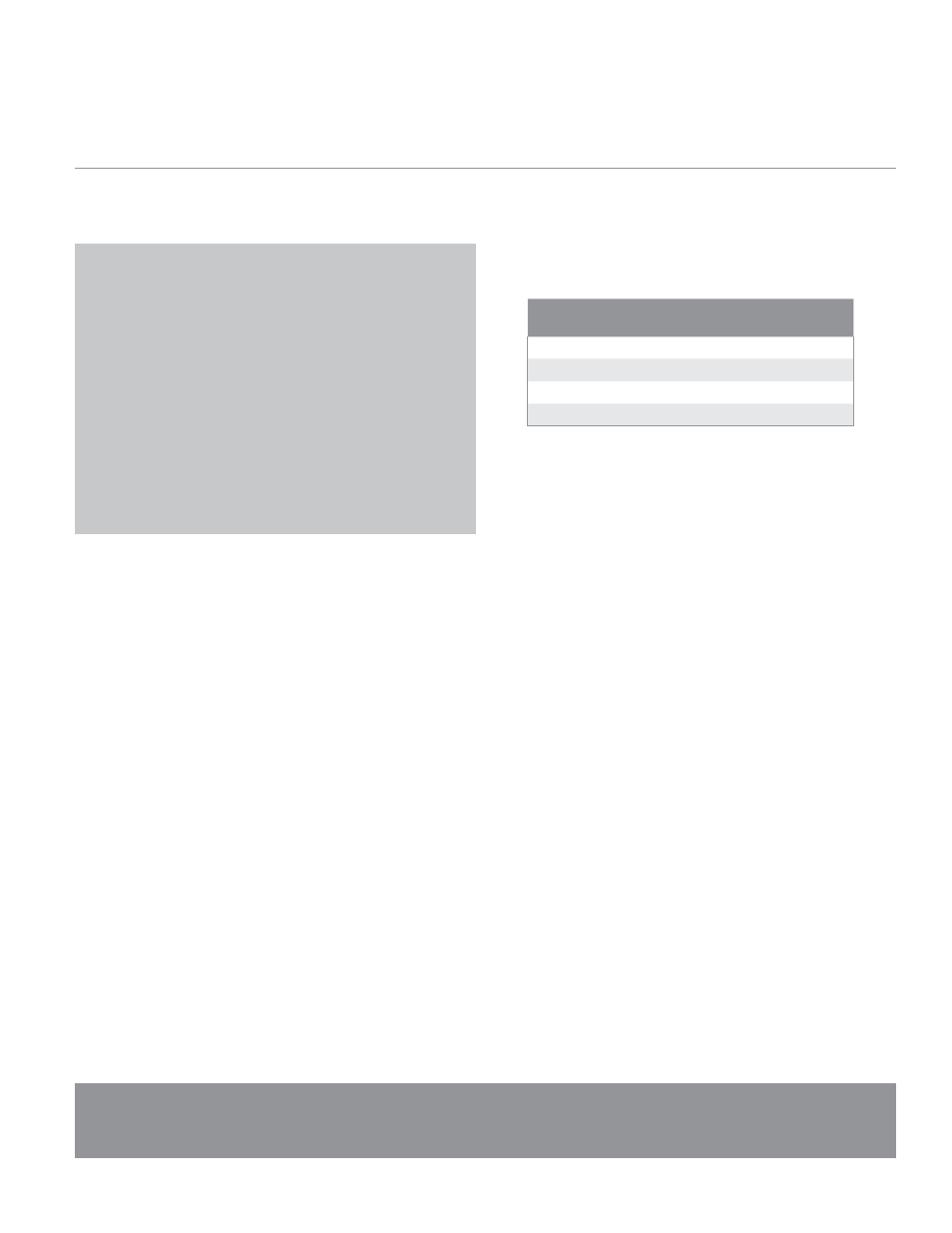
dow Building Solutions
This chart is for the cone and fan type nozzles . Other
specialty nozzles may have different elapsed paused times .
2 . To replace the used nozzle, push down the nozzle
ejector . The used nozzle should eject .
3 . Insert an unused nozzle with the key slot down .
Push in firmly until the nozzle ejector is seated over
the back rim of the nozzle . The refill system is ready
to operate .
Section 5
dO nOT breathe vapor or spray . Proper PPE and ventilation are
required . See product SDS and Section 2 of this manual for further
information . Follow all precautions for product .
5 .1 Spraying
1 . Once the calibration is complete, chose the nozzle with the
pattern and flow rate appropriate for the job . attached
the nozzle .
2 . Practice on scrap material or plastic sheet to get the feel
of spraying and to ensure you are making good foam .
3 . Hold the gun a consistent distance from the work and
perpendicular to the work . Move in a steady side to side
stroke . avoid swinging the gun, it will result in variable thick-
nesses of foam . The speed of your movement and the dis-
tance from the work will determine the thickness of the foam .
4 . always fully engage the trigger of the gun . Partial engage-
ment can result in off ratio foam .
Chemical Temp
elapsed Paused
Spraying Time
70°F (21°C)
35 Seconds
75°F (24°C)
30 Seconds
80°F (27°C)
25 Seconds
85°F (29°C)
20 Seconds
• Go back to the regulator for the hose you disconnected and turn the handle
counterclockwise all the way out.
• Reconnect the nitrogen line and tighten.
• Open the tank valve and read the pressure on the tank. It should be at least
40 – 50 PSI lower than when you started.
• Slowly turn the regulator handle clockwise until the pressure just starts to
increase. You are just bringing the regulator to the tank pressure. Now set the
pressure 20 – 30 PSI lower than when you last calibrated as a starting point.
When in doubt, go lower, you can easily increase it if needed.
Repeat as needed until the A to B ration is between 1.10 and 1.20.
Note: The pressure settings are just a starting point. There are many factors that
impact the actual ratio, including material temperature, hose age and possible partial
blockage, and gun condition. Likewise each set of gauges has a small range of
accuracy. The important thing to remember is that the ratio calculated during calibra-
tion is the FINAL WORD, the tank pressures are the means to get on ratio. If you need
to go outside the ranges listed above (assuming they are under 220 PSI MAX) that is
fine as long as you get the ratio in range.
4 .3 System Purging and Testing
1 .
dO nOT breathe vapor or spray . Proper PPE and ventilation
are required . See product SDS and Section 2 of this manual
for further information . Follow all precautions for product .
2 . Dispense chemicals in an appropriate container .
This is to verify proper chemical flow .
3 . Clean any chemical from the InSTa-FlO
™
Gun face
using a rag .
4 . Insert an unused nozzle with the key slot down .
Push in firmly until the nozzle ejector is seated over
the back rim of the nozzle .
5 . Dispense foam to verify proper chemical mixing .
If improper mixing or poor foam quality, refer to the
Troubleshooting section, Section 10 of this manual .
4 .4 Nozzle Replacement
1 . The life of a nozzle depends on elapsed paused
spraying time and chemical temperature . Replace a
previously used nozzle if the elapsed paused spraying
time is exceeded using the chart on the right as a guide .
13