Wesley BC-6200-8SA User Manual
Page 44
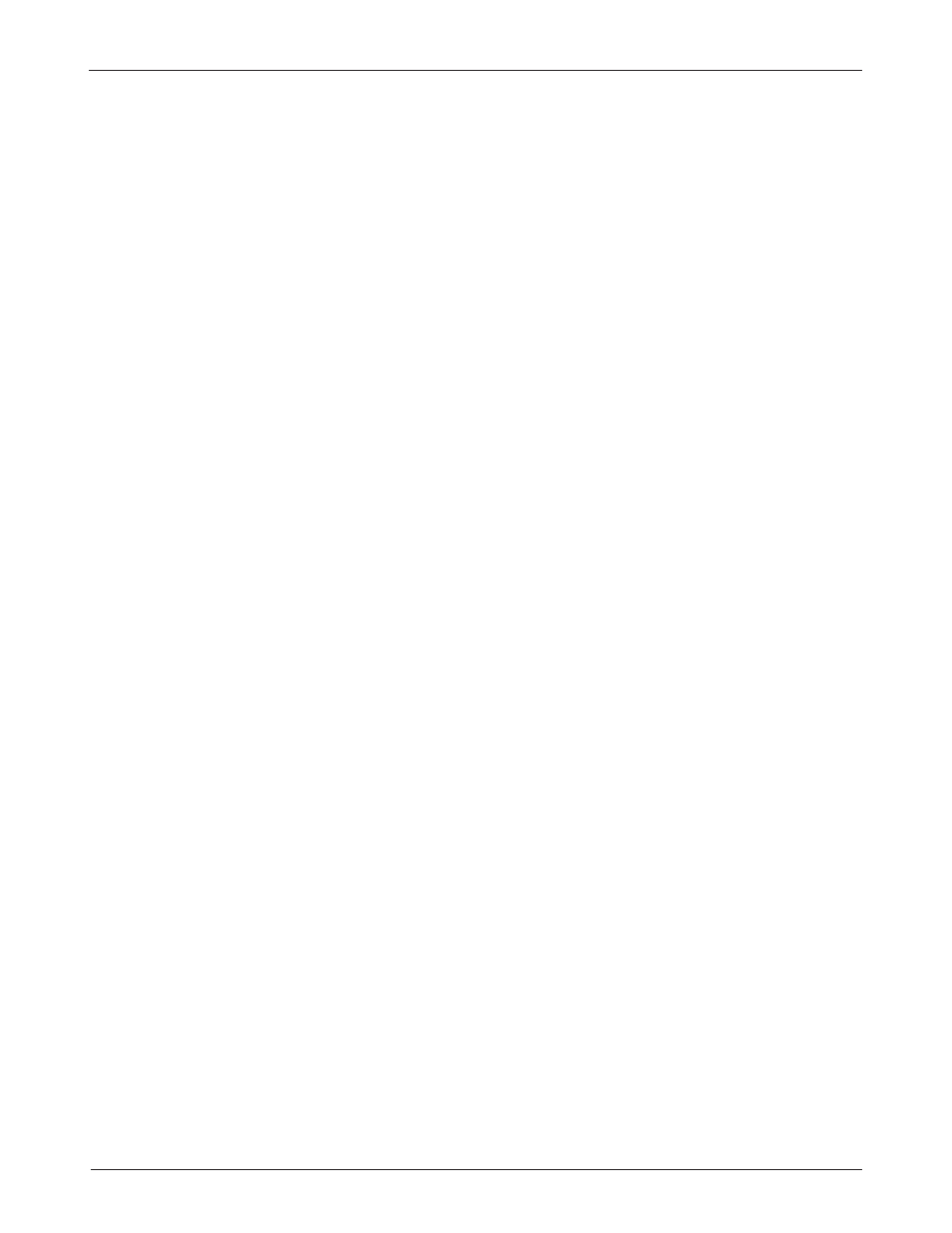
38
Curtis 1268 Manual,
Rev. D
4
Equalizing the Loaded/Unloaded Vehicle Top Speed
on Flat Ground
The controller and vehicle should be configured as follows prior to setting the
maximum vehicle speed:
•
DRIVE C/L
as established in tuning procedure 3
•
FIELD RAMP
= 50%
•
FLD MAP START
= 20% of the specified drive current limit
•
FIELD MIN
= manufacturer’s specified minimum or 3 amps
• The vehicle can be loaded or loaded
If full closed loop speed control is required in both loaded
and unloaded operation, conduct this procedure with the
vehicle loaded.
• The vehicle battery should be fully charged.
Drive the vehicle on a flat surface in a clear area during this procedure. Precautions
should be taken to ensure safety of test personnel and anyone in the test area.
step 1. Select the programmer’s Program menu and scroll down until
M1 FWD SPEED
parameter is displayed, and set this to the desired
top forward speed for Mode 1. Confirm that Mode 1 is selected
by reading the Mode value in the Monitor menu.
step 2. Turn on the keyswitch and the Forward switch and apply full
throttle. While driving the vehicle with full throttle applied, ob-
serve the Speed In and Arm PWM readings in the Monitor menu.
(Note: vehicle speed will display as 0.8 for speeds below 1.0.)
If the speed is being limited by the field map parameters,
the Arm PWM will be 100%. In this case, skip to Step 4.
If the vehicle is truly in closed loop speed control, the Arm
PWM will be less than 100%. The controller will be limiting the
vehicle speed to the programmed maximum speed by reducing
the applied armature voltage below the value commanded by
the throttle. In this case, proceed to Step 3.
step 3. Observe the Arm PWM and Arm Current readings while driving
at top speed. Set the
FLD MAP START
to a value above the Arm Cur-
rent reading. With the vehicle unloaded, increase the
M1 FWD FLD
MIN
until the Arm PWM is between 60–70%. When the vehicle
is loaded the controller will output a higher value of Arm PWM
to achieve this speed.
For slow speeds, a higher
FIELD MIN
is preferable, in order to
ensure a smooth transition between the drive and regen states.
For high speeds, a lower
FIELD MIN
is usually necessary to allow
the vehicle to achieve true closed loop speed control and not be
limited by the field current.
Skip to Step 5.
5 — TUNING GUIDE
- BC-6200-8CA BC-6000-8SA BC-6000-8CA BC-6200-8SAC BC-6250-8SA BC-6250-8CA BC-620-8SA BC-620-8CA BC-600-8SA BC-600-8CA BC-625-8SA BC-625-8CA SCT-7750-8AC SCT-7750-8SA SCT-7750-8CA SCT-7750-6AC SCT-7750-8AC-MTR SCT-7750-8CA-MTR PC-325-6SA PC-325-6CA PMT-5000-8CA PMT-5000-8SA PMT-4500-8SA PMT-4500-8CA SC-775-8CA SC-775-8SA SC-775-8AC