3 datalogger program structure and multiplexers – Campbell Scientific 229 Water Matric Potential Sensor and CE4/CE8 User Manual
Page 11
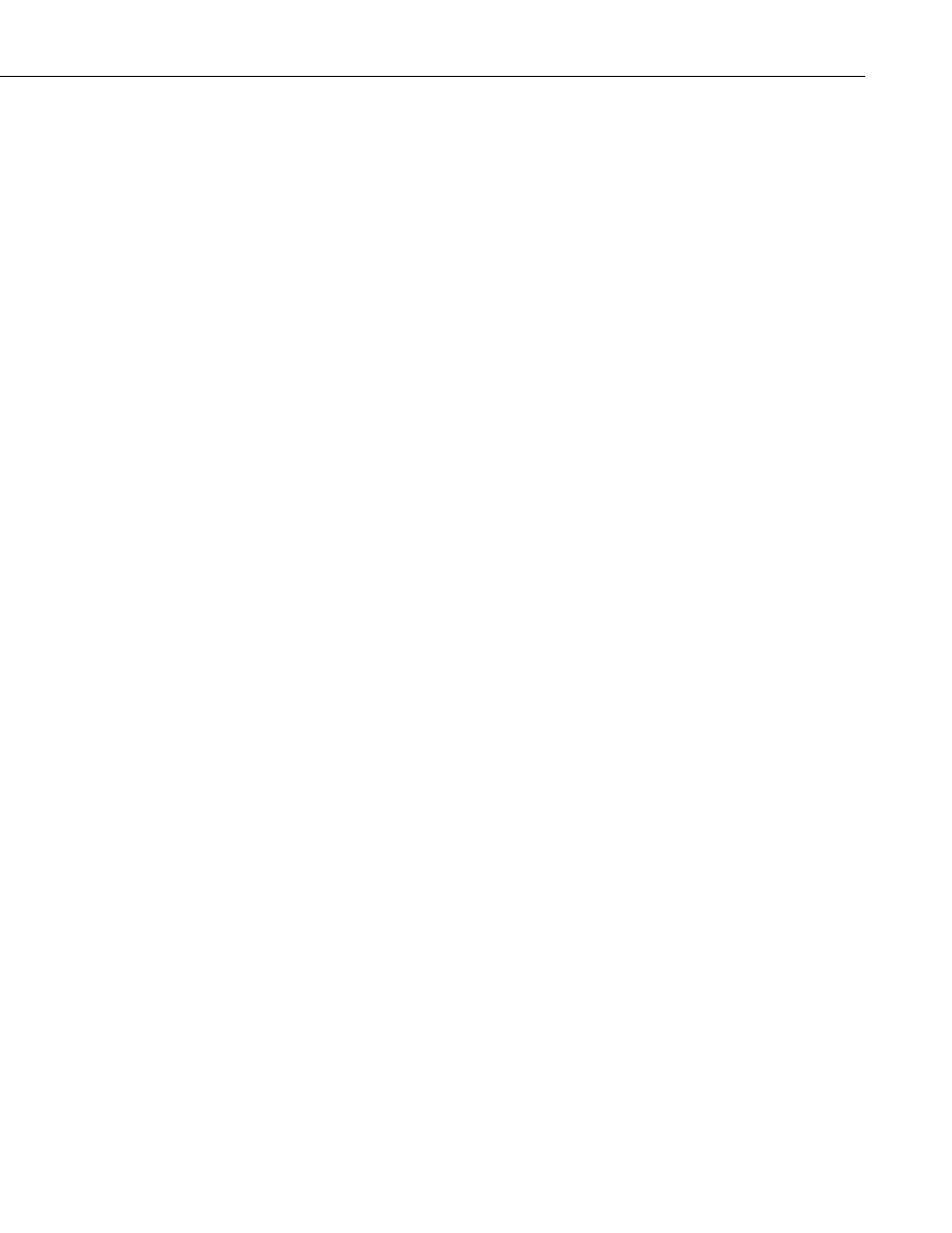
229 Heat Dissipation Matric Water Potential Sensor
5.2 Adjusting for Thermal Properties of Sensor During Early
Heating Times
The discussion presented at the beginning of the calibration section (Section 6)
describes how thermal properties can vary from sensor-to-sensor. The thermal
properties of the needle casing, wiring, and the amount of contact area between
the needle and the ceramic have a slight effect on the temperature response.
Most of the nonideal behavior of the sensor is manifest in the first second of
heating. The measurement is improved if the temperature after 1 s is
subtracted from some final temperature. A typical
ΔT would be T(30 s) -
T(1 s).
5.3 Datalogger Program Structure and Multiplexers
The sequence of datalogger instructions for a 229 measurement is as follows:
1) Measure sensor temperature prior to heating.
2) Set a control port high to enable constant current excitation module and
being heating.
3) Wait for one second of heating and measure sensor temperature.
4) Wait for 29 more seconds of heating and measure sensor temperature.
5) Set control port low to disable the constant current excitation module and
end heating.
6) Calculate temperature rise by subtracting T(1 s) from T(30 s).
Since all of the output channels of the CE4 or CE8 are activated when the
control terminal is set high, power will be applied to all of the 229 sensors
connected to the current source. Inaccurate measurements can result if the
temperature of multiple sensors is simply read sequentially. The inaccuracy
can occur because a finite amount of time is required to execute each of the
temperature measurement instructions.
For example, a CR10X making multiple differential thermocouple readings
with 60 Hz rejection takes 34.9 ms to read one thermocouple, and 30.9 ms
more for each additional thermocouple. In a configuration where six 229
sensors are connected to a CE8 with their thermocouple wires connected
sequentially to the CR10X wiring panel, the sixth 229 sensor will heat for
154.5 ms longer than the first sensor each time its temperature is measured.
The amount of time between temperature measurement of the first sensor and
the last sensor can be as long as 0.5 seconds under some measurement
configurations.
The error caused by this difference in heating times can be minimized if the
sensors are connected to the constant current excitation module and datalogger
during calibration in exactly the same order they will be wired during field
deployment. The difference in heating times can be eliminated altogether by
heating the sensors one at a time through a multiplexer such as the AM16/32B.
7