0 installation, 0 operation, 0 gauge replacement – Ashcroft 1036 Gauge with 1037 Fitting User Manual
Page 5
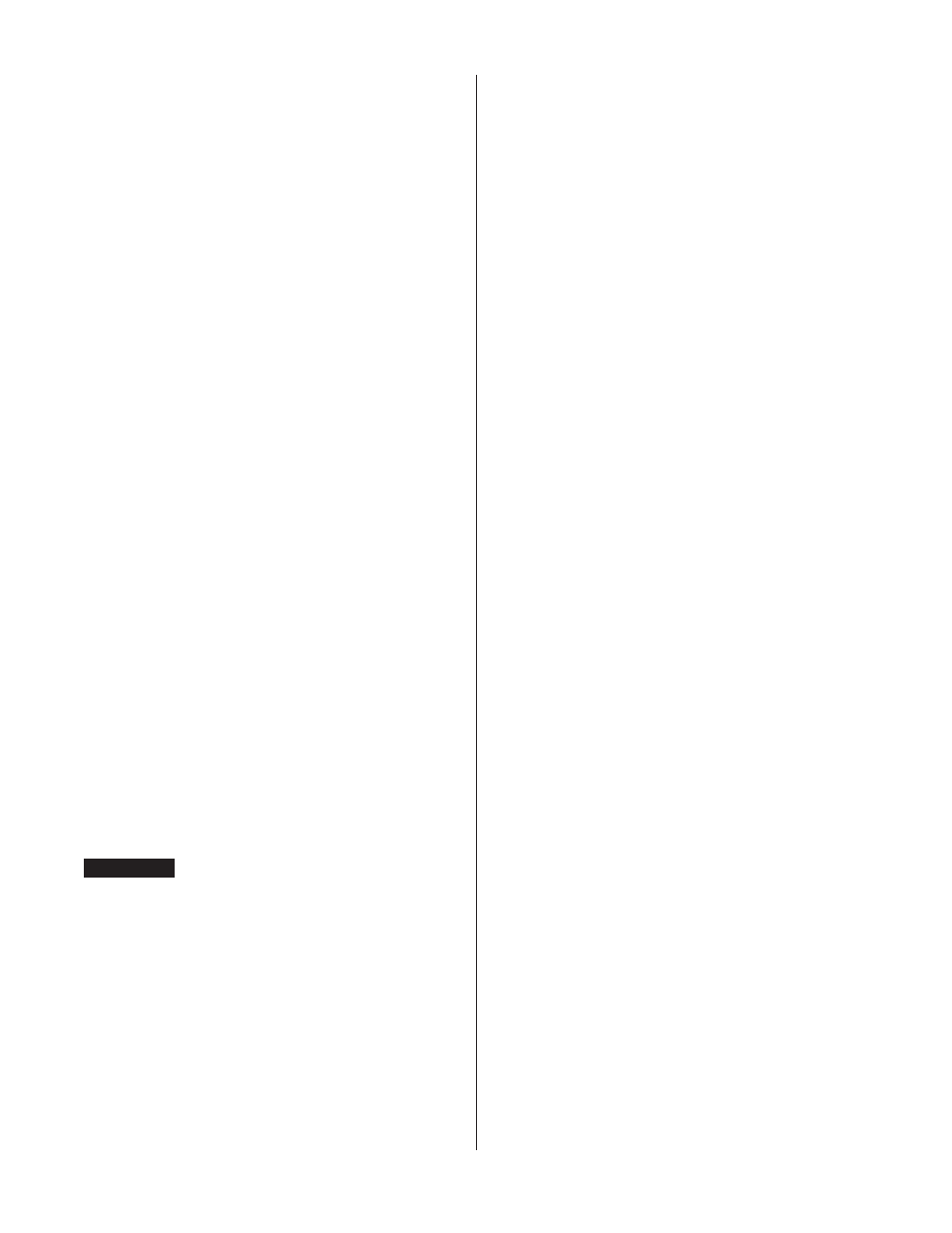
750°F (400°C) the customers should use their own small
diameter piping to avoid possible corrosion of the stainless steel.
The five foot capillary will protect the gauges used on the com-
mon cryogenic (less than –300°F (200°C) gases, liquid argon,
nitrogen, and oxygen.) The capillary and gauge must be cleaned
for oxygen service. The media must not be corrosive to stainless
steel, and must not plug the small bore of the capillary.
2.5 Diaphragm seals – A diaphragm seal should be used to
protect gauges from corrosive media, or media that will plug
the instrument. Diaphragm seals are offered in a wide variety
of designs and corrosion resistant materials to accommo-
date almost any application and most connections. Visit
www.ashcroft.com for details.
2.6 Autoclaving – Sanitary gauges with clamp type connec-
tions are frequently steam sterilized in an autoclave. Gauges
equipped with polysulfone windows will withstand more auto-
clave cycles than those equipped with polycarbonate win-
dows. Gauges equipped with plain glass or laminated safety
glass
should not be autoclaved. Gauge cases should be
vented to atmosphere (removing the rubber fill/safety plug if
necessary)
before autoclaving to prevent the plastic window
from cracking or excessively distorting. If the gauge is liquid
filled, the fill should be drained from the case and the front
ring loosened before autoclaving.
3.0 INSTALLATION
3.1 Location – Whenever possible, gauges should be locat-
ed to minimize the effects of vibration, extreme ambient tem-
peratures and moisture. Dry locations away from very high
thermal sources (ovens, boilers etc.) are preferred. If the
mechanical vibration level is extreme, the gauge should be
remotely located (usually on a wall) and connected to the
pressure source via flexible tubing.
3.2 Gauge reuse – ASME B40.100 recommends that
gauges not be moved indiscriminately from one application
to another. The cumulative number of pressure cycles on an
in-service or previously used gauge is generally unknown, so
it is generally safer to install a new gauge whenever and
wherever possible. This will also minimize the possibility of a
reaction with previous media.
3.3 Tightening of gauge – Torque should never be applied
to the gauge case. Instead, an open end or adjustable
wrench should always be used on the wrench flats of the
gauge socket to tighten the gauge into the fitting or pipe.
NPT threads require the use of a suitable thread sealant,
such as pipe dope or teflon tape, and must be tightened very
securely to ensure a leak tight seal.
CAUTION:
Torque applied to a diaphragm seal or its
attached gauge, that tends to loosen one relative to the
other, can cause loss of fill and subsequent inaccurate read-
ings. Always apply torque
only to the wrench flats on the
lower seal housing when installing filled, diaphragm seal
assemblies or removing same from process lines.
3.4 Process isolation – A shut-off valve should be installed
between the gauge and the process in order to be able to
isolate the gauge for inspection or replacement without shut-
ting down the process.
3.5 Surface mounting – Also known as wall mounting.
Gauges should be kept free of piping strains. The gauge case
mounting feet, if applicable, will ensure clearance between the
pressure relieving back and the mounting surface.
3.6 Flush mounting – Also known as panel mounting. The
applicable panel mounting cutout dimensions can be found
at www.ashcroft.com
4.0 OPERATION
4.1 Frequency of inspection – This is quite subjective and
depends upon the severity of the service and how critical the
accuracy of the indicated pressure is. For example, a month-
ly inspection frequency may be in order for critical, severe
service applications. Annual inspections, or even less fre-
quent schedules, are often employed in non-critical applica-
tions.
4.2 In-service inspection – If the accuracy of the gauge
cannot be checked in place, the user can at least look for (a)
erratic or random pointer motion; (b) readings that are sus-
pect – especially indications of pressure when the user
believes the true pressure is 0 psig. Any gauge which is
obviously not working or indicating erroneously, should be
immediately valved-off or removed from service to avoid a
possible pressure boundary failure.
4.3 When to check accuracy – Any suspicious behavior of
the gauge pointer warrants that a full accuracy check be per-
formed. Even if the gauge is not showing any symptoms of
abnormal performance, the user may want to establish a fre-
quency of bench type inspection.
4.4 When to recalibrate – This depends on the criticality of
the application. If the accuracy of a 3-2-3% commercial type
gauge is only 0.5% beyond specification, the user must
decide whether it’s worth the time and expense to bring the
gauge back into specification. Conversely if the accuracy of
a 0.25% test gauge is found to be 0.1% out of specification
then the gauge should be recalibrated.
4.5 Other considerations – These include (a) bent or unat-
tached pointers due to extreme pressure pulsation; (b) bro-
ken windows which should be replaced to keep dirt out of
the internals; (c) leakage of gauge fill; (d) case damage –
dents and/or cracks; (e) any signs of service media leakage
through the gauge including its connection; (f) discoloration
of gauge fill that impedes readability.
4.6 Spare parts – As a general rule it is recommended
that the user maintain in inventory one complete Ashcroft
®
instrument for every ten (or fraction thereof) of that
instrument type in service.
5.0 GAUGE REPLACEMENT
It is recommended that the user stock one complete
Ashcroft
®
instrument for every ten (or fraction thereof) of that
instrument type in service. With regard to gauges having a
service history, consideration should be given to discarding
rather than repairing them. Gauges in this category include
the following:
a.
Gauges that exhibit a span shift greater than 10%. It is
possible the Bourdon tube has suffered thinning of its
walls by corrosion.
b.
Gauges that exhibit a zero shift greater than 25%. It is
likely the Bourdon tube has seen significant overpres-
sure leaving residual stresses that may be detrimental
to the application.
c.
Gauges which have accumulated over 1,000,000 pres-
sure cycles with significant pointer excursion.
d.
Gauges showing any signs of corrosion and/or leakage
of the pressure system.
e.
Gauges which have been exposed to high temperature
or exhibit signs of having been exposed to high temper-
ature – specifically 250°F or greater for soft soldered
systems; 450°F or greater for brazed systems; and
750°F or greater for welded systems.
5
- 1009 - Stainless Steel Pressure Gauge 1008S/SL - Stainless Steel Pressure Gauge 1008S - Stainless Steel Pressure Gauge 1189 - Low Pressure Bellows Gauge 1188 - Low Pressure Bellows Gauge 1187 - Low Pressure Bellows Gauge 1150H - Reid Vapor Gauge 1122 - Industrial Gauge 1220 - Industrial Gauge 1017 - Industrial Gauge 1220 - Receiver Gauges 1017 - Receiver Gauges 1010 - Receiver Gauges 1009 - Receiver Gauges 1220 - Refrigeration Gauges 1017 - Refrigeration Gauges 1010 - Refrigeration Gauges 1009 - Refrigeration Gauges 1220 - Hydraulic Gauges 1017 - Hydraulic Gauges 1010 - Hydraulic Gauges 1009 - Hydraulic Gauges 1010 - Industrial Gauge 2462 - Duragauge® Pressure Gauge 1379 - Duragauge® Pressure Gauge 1377 - Duragauge® Pressure Gauge 2462 - Receiver Gauges 1377 - Receiver Gauges 1379 - Receiver Gauges 1279 - Receiver Gauges 1259 - Pressure Gauge 1082 - Pressure Test Gauge