Basic operation, Front panel features, Hardware features – Red Lion TCU User Manual
Page 4: Setpoint features, Input features, Output features, Auto-tune
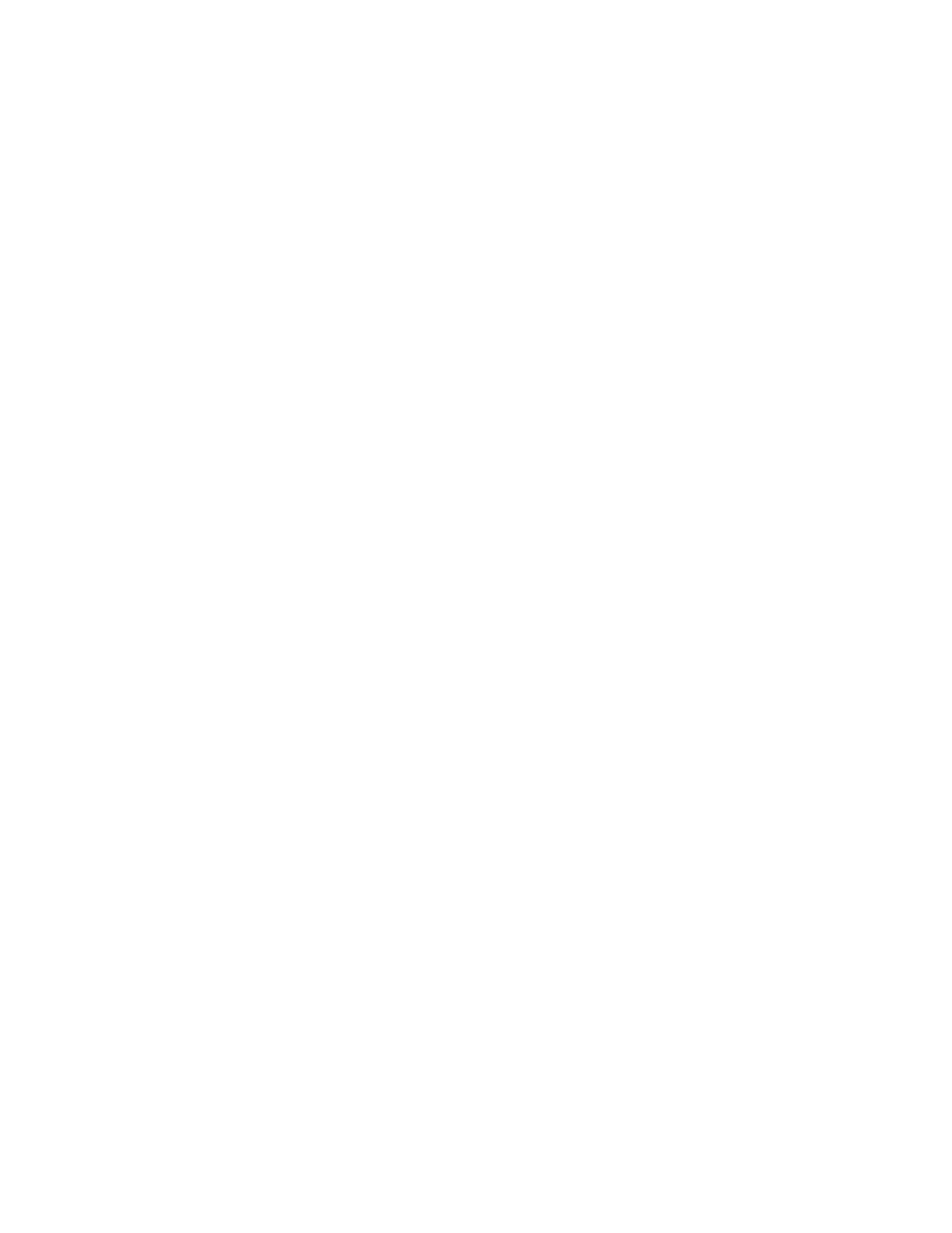
23. CONSTRUCTION:
Front Panel: Flame and scratch resistant tinted plastic
Case: High impact black plastic. (Mounting collar included)
Type 4X/IP65 model only: Sealed bezel utilizing two captive mounting
screws (panel gasket included). This unit is rated for Type 4X/IP65 indoor
use. Installation Category II, Pollution Degree 2
24. WEIGHT: 1.3 lbs (0.6 kgs)
ACCESSORIES:
External SSR Power Unit:
Switched Voltage Range: 50 to 280 VAC (Nominal: 240 VAC)
Load Current: 45 Amps @ 25°C ambient temperature
35 Amps @ 50°C ambient temperature
On State Input: 3 to 32 VDC @ 1500 Ω impedance. (isolated)
(Use Logic/SSR drive output module.)
Off State Input: 0.0 to 1.0 VDC
Size: 5.5" (14 cm) L x 4.75" (12 cm) W x 2.62" (6.6 cm) H
Current Transformer:
Current Ratio: 50:0.1 (Amperes)
Accuracy: ±5.0%
Operating Frequency: 50 to 400 Hz
Insulation Class: 0.6 Kv BIL 10 Kv full wave
Terminals: Brass studs No. 8-36, (flat washer, washer, nut)
Weight: 8.0 oz (226 g)
Approvals: UL recognized component
BASIC OPERATION
The TCU controls a process temperature by measuring the temperature via an
input probe, then calculating a control output power value by use of a modified
PID control algorithm. The unit controls the system with the new output power
value to keep the process temperature at setpoint. The PID control algorithm
incorporates features which provide for high control accuracy and low
temperature overshoot from process disturbances.
FRONT PANEL FEATURES
In the normal operating mode, the unit will display the process temperature
in the upper display. One of six other parameters can be viewed in the lower
display:
- Setpoint
- % Power Output
- Temperature Deviation
- Heater Current
- Second Input Process Value
- Temperature Symbol (F or C)
The six parameters can be scrolled through by pressing the DSP button. If
enabled, the control setpoint or power output (manual mode only) can be
directly modified in this mode.
In the normal operating mode, parameters are selected by use of the PAR
button and modified by use of the UP and DOWN buttons. Parameters are then
entered by the PAR button, which advances the user to the next parameter.
Pressing the DSP button immediately returns the controller to the normal
operating mode when making a parameter change. The controller’s configuration
and parameter settings are stored in an internal E
2
PROM device.
HARDWARE FEATURES
The fast 100 msec input sampling rate provides quick controller response to a
process disturbance, thus providing excellent temperature control. Measurement
accuracy of 0.15% or better, provides closer process control conforming to the
desired control setpoint value. One model accepts a variety of both thermocouple
or RTD temperature probes. The AC input power is switch selectable, allowing
the unit to operate from either 115 VAC or 230 VAC. Since the controller is
serviceable from the front of the panel, the output modules may be easily changed
or replaced without disturbing the wiring behind the panel. No re-programming is
required when changing or replacing modules.
The optional Type 4X/IP65 rated model utilizes two bezel securing screws
and a neoprene gasket to guarantee a water tight seal, when properly installed.
The standard model simply requires pressing a latch to remove the unit.
Low-drift, highly stable circuitry ensures years of reliable and accurate
temperature control. The recommended two-year re-calibration interval is easily
accomplished via the programming menu.
SETPOINT FEATURES
The controller setpoint can be protected from out of range values by
programming the setpoint range limit values. Additionally, safeguards from
inadvertent data entry can be programmed.
The setpoint ramp feature ramps the setpoint value at start-up or any time a
setpoint change is made, at a user programmable rate. This feature reduces
thermal shock to the process and helps to minimize temperature overshoot.The
setpoint may also be transmitted by the optional linear DC output for slave
control loops.
The second analog input may be configured as a remote setpoint. As such, the
controller is easily switched from local/remote setpoint operation via the front
panel or user input. Ratio and bias parameters provide on-line scaling of the
remote setpoint. Absolute limit values and maximum rate of change of the
remote setpoint further enhance controller flexibility.
INPUT FEATURES
A programmable input filter can be used to stabilize readings from a process
with varying or oscillating temperature characteristics, helping to provide better
temperature control. A programmable temperature shift and slope function can
be used to compensate for probe errors or to have multiple TCU units indicate
the same nominal temperature.
The programmable User Input can be used to control a variety of functions,
such as auto/manual transfer of the controller, reset alarm output(s), etc.
The second analog input has independent scaling parameters to match the
units of other processes or transmitters, or to match the controller’s range.
OUTPUT FEATURES
Programmable output power limits provide protection for processes where
excessive power can cause damage. Automatic sensor probe break detection, for
fail-safe operation, causes the controller to default to a programmed output
power (upscale or downscale burnout). With adjustable time proportioning-
cycle time, and programmable DC linear output, the controller can satisfy a
wide variety of output requirements.
Programmable dampening output hysteresis and output update time parameters
can dramatically reduce actuator activity without degrading control accuracy.
The RS485 Communication option allows the user to access various
controller parameters such as the setpoint, % output power, % proportional
band, etc. The controller may be setup to transmit various parameters at a
programmable automatic print rate.
AUTO-TUNE
The TCU has an auto-tune feature which, on demand, automatically
determines the PID control parameters for a particular thermal process. After
completion of auto-tune, the PID parameters are automatically optimized for
that process and loaded into nonvolatile memory. The operator may view and
modify the parameters as desired.
Auto-tune may be invoked either at start-up or at setpoint, depending on the
process requirements. An auto-tune programmable dampening factor produces
various levels of process control and response characteristics.
4