Portatree timing systems – PortaTree Eliminator Asphalt Tracks User Manual
Page 5
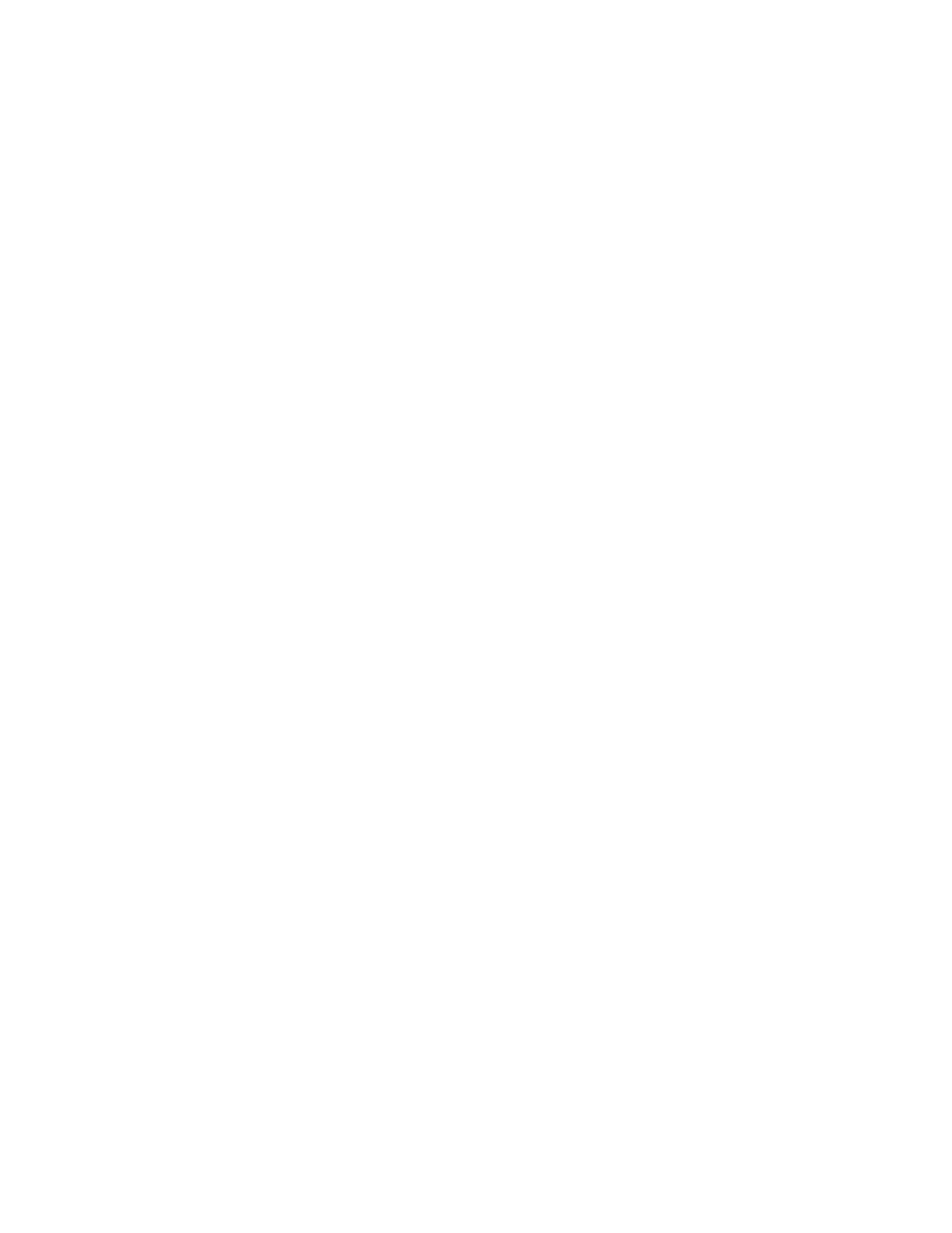
10. The Eliminator 2000 also has 2 serial ports so that you can operate a Time Slip Printer and
a large external L.E.D. Display at the same time.
PORTATREE TIMING SYSTEMS
GUIDE TO SETTING UP AN ACCURATE DRAG RACING
STARTING LINE
A Drag Track Starting Line must be setup accurately so that left and right lanes have the same
performance level. When a race vehicle leaves the starting line, it must leave from the same position
every time and both lanes must have the same starting beam locations. The vehicle starts the timing
clocks when the front tire rolls out of the stage beam (stage light on the tree goes out). The vehicle’s tire
must rollout of the stage photo cell beam in the same manner and position for both lanes every time.
In order to setup an accurate starting line, you must measure how far the vehicle’s tire rolls out
of the staging beams and you must set the photo cells and light sources so that the rollout is equal in
both lanes. This guide will give you insight into how rollout can be changed to meet the accuracy
required for any drag track layout.
Rollout is affected by the height of the photo cell beam off of the track surface. The photo cell
beam should have a consistent height off of the track surface all the way across the track. Photo cell
beam height can be measured by finding the beam center and sliding a triangle (30 – 60 degree) under
the beam and marking the point where the beam is blocked. The starting line beam height should be 2
inches off of the track surface. Diagram 1 will show you how a triangle is used to determine the beam
height.
Measuring the rollout of a wheel through the beam should be tested with a rollout wheel. The
rollout wheel should be 24 inches in diameter and of solid construction. A trailing arm should be
attached to the axis of the wheel and should have a marking block on the opposite end for placing on the
track surface and marking beam position. Diagram 2 shows the construction of a rollout wheel and
Diagram 3 shows a rollout wheel in use.
In order to simplify the procedure and finish your job with accurate results, only work on one
beam at a time. We recommend starting with the stage beam first. The rollout should be tested in the
racing groove on the track surface. We like to test the rollout in several locations but rely only on the
results taken in the groove. The rollout wheel should be rolled into the beam in the direction of travel of
the vehicle. When the beam is blocked, a mark should be placed on the track surface. The wheel should
be rolled in again until the beam is unblocked and again the track surface should be marked. The
distance between the two marks should be 12 inches but can vary either way be ¼ inch. It is always best
to get the best accuracy possible, but the last little bit can take many hours of work..
In order to adjust the beams for rollout, you must raise or lower the light source and or photo
detector. You may also have to limit the light source or detector viewing area. This can be done with
light shades or screens or even duct tape. We do recommend that the manner in which the light source
is blocked off be a permanent block.
After the stage beam has been positioned and the rollout has been measured and adjusted, the
prestage beam can be tested. Position the prestage beam 7 inches before the stage beam. Measure the