Actron CP7001 User Manual
Page 2
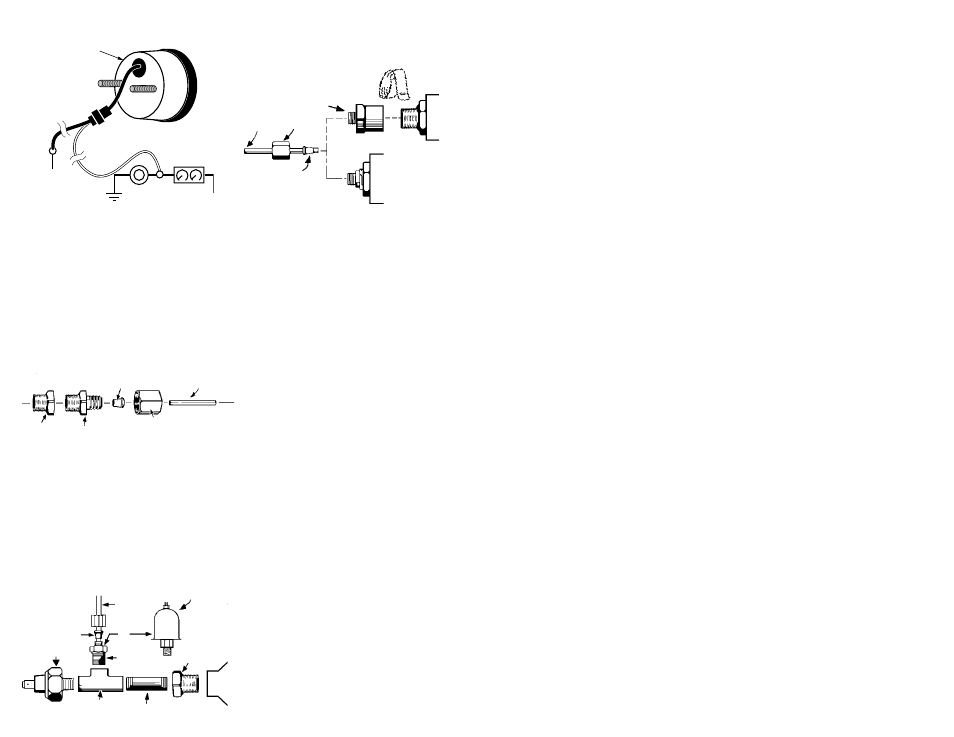
2
5. If the hex nut adapter is not attached to the
gauge, then wrap Teflon tape around the adapt-
er’s threads and attach the hex nut adapter.
Refer to Figure 5.
For Mechanical Gauges:
1. If you are monitoring a fluid system, drain the
fluid level to a level below the warning light
sender location.
2. Remove the warning light sender from the
engine and install the engine fitting in the same
location. If an adapter is required, first install the
adapter and then install the engine fitting.
3. uncoil a few feet of tubing and slide the hex nut
and ferrule over the end of the tubing as shown
in Figure 3. Insert the tubing into the engine
fitting, and then tighten the hex nut into the
engine fitting.
Figure 5
heX nuT ADAPTeR
heX nuT
TuBIng
FeRRule
1/8” nPT
gAuge
CoMPRessIon
FITTIng gAuge
TeFlon TAPe
Figure 4
To MeChAnICAl gAuge
eleCTRICAl gAuge
senDeR
hose
FeRRule
WARnIng lIghT
senDeR
T-FITTIng
nIPPle
engIne
BloCk
ADAPTeR
engIne
FITTIng
oR
4.
Optional T-Fitting (CP7556) (Figure 4) - Install
the nipple into the T-Fitting and tighten the
end of the other nipple into the warning light
sender location. Install an adapter fitting
first if needed. In one of the two remaining
openings in the T-Fitting, insert the engine fitting
and then follow step 3 to connect the pressure
tubing. Insert the warning light sender into the
remaining T-Fitting opening. Install an adapter
fitting first, if needed (we do not produce metric
fittings for the connection from a metric warning
light sender to the T-Fitting).
Figure 2b
For Negative Dimmer Controls
To
gRounD
DIMMeR
ConTRol
DAsh
lIghTIng
WhITe
Blue
+12V
+12V
gAuge
Figure 3
FeRRule
TuBIng
ADAPTeR
engIne FITTIng
heX nuT
6. Route the remaining tubing through the fire
wall to the gauge mounting location. leave at
least one 3” or longer loop in the tubing before
it enters the fire wall and protect the tubing from
rough edges of the fire wall hole.
7. Repeat step 3 to attach the tubing to the
gauge.
8. Complete the mounting of the gauge.
9. Refill the fluid level, if drained, to its normal
level.
10. Start the engine and observe the fitting con-
nections for leaks and the gauge for proper
operation.
For Electrical Gauges:
1. If you are monitoring a fluid system, drain the
fluid level to a level below the warning light
sender location.
2. Remove the warning light sender from the
engine and insulate the end of the sender wire if
a T-Fitting is not being used. Install the gauge’s
sender in the same location in the engine block.
If an adapter is required, first install the adapter
and then the gauge’s sender.
3.
Optional T-Fitting (CP7556) (Figure 4) -
Install the nipple into the T-Fitting and tighten
the other end of the nipple into the warning light
sender location in the engine block. Install an
adapter fitting first if needed. In one of the two
remaining openings in the T-Fitting, insert the
gauge sender. Insert the warning light into the
remaining T-Fitting opening. Install the adapter
fitting first, if needed. (we do not produce metric
fittings for the connection from a metric warning
light sender to the T-Fitting).
4. Run a length of 18-gauge insulated copper wire
from the gauge’s sender to the gauge’s mount-
ing location.
5. Connect the wire to the connection on top of the
gauge sender.
6. Connect the sender wire to the ”s” connec-
tion post as shown in Figure 6. Do not over
tighten.