Dwyer STFLO User Manual
Page 3
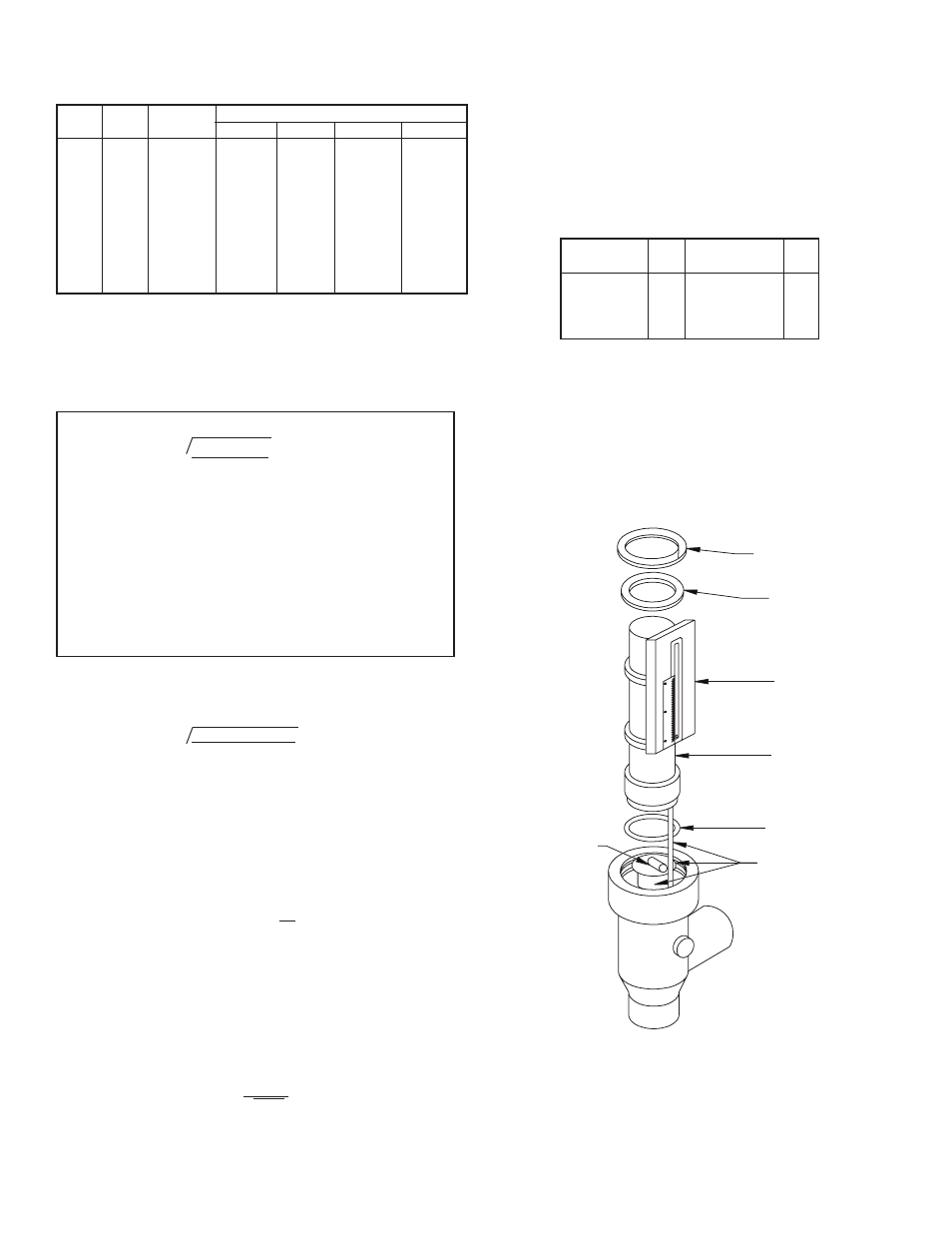
MAXIMUM FLOWS (WITHOUT EFFECTING ACCURACY)
FOR UNDERSIZED PIPES CONNECTED DIRECTLY TO
FLOWMETER INLETS
PIPE
NPS
1/4
3/8
1/2
3/4
1
1-1/4
1-1/2
2
2-1/2
3
DATA
(ID)
2
0.132
0.243
0.387
0.679
1.100
1.904
2.592
4.272
6.096
9.413
MAX. *
GPM LIQ.
1.72
2.98
4.74
8.31
13.47
23.32
31.74
52.29
74.56
115.2
ATMOS.
0.864
1.59
2.53
4.44
7.20
12.5
17.0
28.0
39.9
61.6
50 PSIG
3.80
7.00
11.1
19.5
31.7
58.8
74.6
123
176
271
100 PSIG
6.74
12.4
19.8
34.7
56.1
97.2
132
218
311
480
200 PSIG
12.6
23.2
37.2
64.9
105
182
248
408
582
804
MAX. SCFM AIR @ †
Data per Cameron Hydraulic Data. Based on 5 FPS max. liquid velocity having
no effect on flowmeters accuracy if the inlet pipe is smaller than the meter
connections.
SCFM=0.445 x (psig + 14.7) x (ID)
2
. Based on 20 FPS max. air velocity having
no effect on flowmeters accuracy if the inlet pipe is smaller than the meter
connections.
*
†
CORRECTING READINGS FOR NEW GAS CONDITIONS
Where:
Qg=SCFM, corrected to new conditions
Qs=SCFM read on meter scale
Pg=Operating pressure, psia (psig + 14.7)
Qs=Pressure stated on scale, psia (psig + 14.7)
Tg=Operating temperature, absolute (˚F +460)
Ts=Temperature stated on scale, absolute (˚F + 460)
Pg=Specific gravity of metered gas
Ps=Specific gravity stated on scale
Qg = Qs
√
Pg x Ts x Ps
Ps x Tg x Pg
EXAMPLE: If using a standard meter scaled for SCFM Dry Air @ 100
psig, 70˚F on argon (SP. GR.=1.378) at 50 psig, 100˚F, what would the
conversion factor be?
Thus, actual flow of the argon would be the observed scale reading
times 0.622.
STEAM
Series STFLO flowmeters are recommended for use with vapors,
especially steam. The conversion factor may be determined with the
following formula:
Mfh = Qm _______
Where:
Mfh=Actual flow, lbs/hr.
Qm=Meter scale reading, Std. (SCFM Dry Air @ 100 psig, 70˚F)
Sv=Specific volume of media (from steam table)
EXAMPLE: When using a standard gas meter scaled from SCFM Dry Air
@ 100 psig, 70˚F, what is the conversion factor for lbs/hr. steam at 50
psig, 300˚F?
Mfh =
Thus, actual flow of steam in lbs/hr. would be the observed scale reading
times 2.267.
VISCOSITY CONSIDERATIONS
Each liquid flowmeter has so-called “Viscosity Immunity Ceiling” (V.I.C.).
Usually, if the viscosity of the metered liquid is less than the V.I.C., the
meter will be influenced significantly, and must be calibrated for that
viscosity. Effects of viscosity on a given flowmeter are not always
predictable. Two apparently similar liquids with comparable densities
and viscosities may impact meter calibrations quite differently. The table
below provides general guidelines for the typical maximum viscosity for
meter models without affecting accuracy.
MAINTENANCE
Upon final installation of the Series STFLO Stainless Steel Flowmeters,
no routine maintenance is required. A periodic check of the system
calibration is recommended. The Series STFLO Stainless Steel
Flowmeters are not field serviceable and should be returned if repair is
needed (field repair should not be attempted and may void warranty). Be
sure to include a brief description of the problem plus any relevant
application notes. Contact customer service to receive a return goods
authorization number before shipping.
METER DISASSEMBLY
FIGURE 2: PARTIALLY EXPLODED DRAWING OF SERIES STFLO
STAINLESS STEEL FLOWMETERS
It is not necessary to remove the flowmeters from the pipeline for
cleaning or replacing parts. The body remains plumbed into the pipe,
allowing easy service and even installation of the different sensing
elements to accommodate new flow rates or fluids. Figure 2 shows some
of the major components. Step by step disassembly and reassembly
instructions and photos are included in the following.
Qa = 1.00
√
64.7 x1.00 x530
114.7 x1.378 x560
= 0.622
5.879
√Sv
5.879
√6.727
AVERAGE V.I.C., CENTISTOKES, FOR
STANDARD “THRU VIEW”FLOWMETERS
100% GPM,
3/4˝ METERS
0.54-0.80
1.20-2.60
3.80-7.00
10.0-23.0
100% GPM,
1-1/2˝ METERS
11.0-15.0
21.0-35.0
50.0
70.0-120
CTS
50
100
250
500
CTS
3
7
15
25
SPIRAL RETAINING
RING
INNER FLANGE
RING
READING
SCALE
SIGHT TUBE
ASSEMBLY
STATIC O-RING
SEAL
MAGNET(S)
CORE TUBE / FLOAT
ASSEMBLY